Table of Contents
What is Hard Anodizing of Aluminum Alloy
Hard anodizing of aluminum alloy is an electrochemical treatment process.
In a specific electrolyte solution, the aluminum alloy serves as the anode. Through the application of an external electric current, a thick and dense oxide film is formed on the surface of the aluminum alloy.
Compared with ordinary anodizing, the oxide film formed by hard anodizing is thicker and has a higher hardness, exhibiting superior properties such as wear resistance, corrosion resistance, and insulation.
Process Flow of Hard Anodizing of Aluminum Alloy
Pretreatment:
First, degrease the aluminum alloy to remove the oil stains and impurities on the surface. Then, carry out alkali etching to remove the natural oxide film and other impurities on the surface of the aluminum alloy. Finally, conduct a neutralization treatment to remove the residual lye after alkali etching and prevent adverse effects during the subsequent anodizing process.
Anodizing:
Place the pretreated aluminum alloy as the anode into a specific electrolyte solution. At the same time, set up a suitable cathode. Under certain conditions of voltage, current density, and temperature, an anodizing reaction will occur on the surface of the aluminum alloy, generating an oxide film.
Post-treatment:
After the anodizing is completed, seal the aluminum alloy. This can effectively seal the pores of the oxide film and improve its corrosion resistance and wear resistance.
Common sealing methods include hot water sealing, steam sealing, inorganic salt sealing, etc.
Finally, clean and dry it.
Figure No.1 Hard Anodizing of Aluminum Alloy Workflow
The Advantages of Hard Anodizing of Aluminum Alloy
Strong Bonding Ability:
The oxide film is formed by the growth on the surface of the aluminum alloy itself, and its bonding force with the substrate is extremely firm, making it not easy to peel off. In contrast, the bonding force between the electroplated layer and the paint film and the substrate is relatively weak, and they are prone to peeling off when subjected to external forces.
Good Wear Resistance:
The hard anodized oxide film layer has a high hardness, which can effectively resist friction and wear, making it suitable for occasions with high requirements for wear resistance.
In comparison, the coatings formed by processes such as painting have relatively poor wear resistance.
High Corrosion Resistance:
The dense oxide film can effectively block the intrusion of external corrosive media, providing good corrosion resistance, especially showing more prominent performance under harsh environmental conditions.
By contrast, problems such as corrosion perforation may occur in the electroplated layer during long-term use.
Excellent Insulation Performance:
The hard anodized oxide film has good insulation performance and can be applied to some electronic and electrical equipment with insulation requirements. Other surface treatment processes generally do not possess this insulation characteristic.
Aesthetically Pleasing:
The color and texture of the oxide film are relatively natural, and it has a unique metallic luster. It can meet certain aesthetic requirements without the need for additional decorative treatments.
>>> Back to Surface Treatment Guide
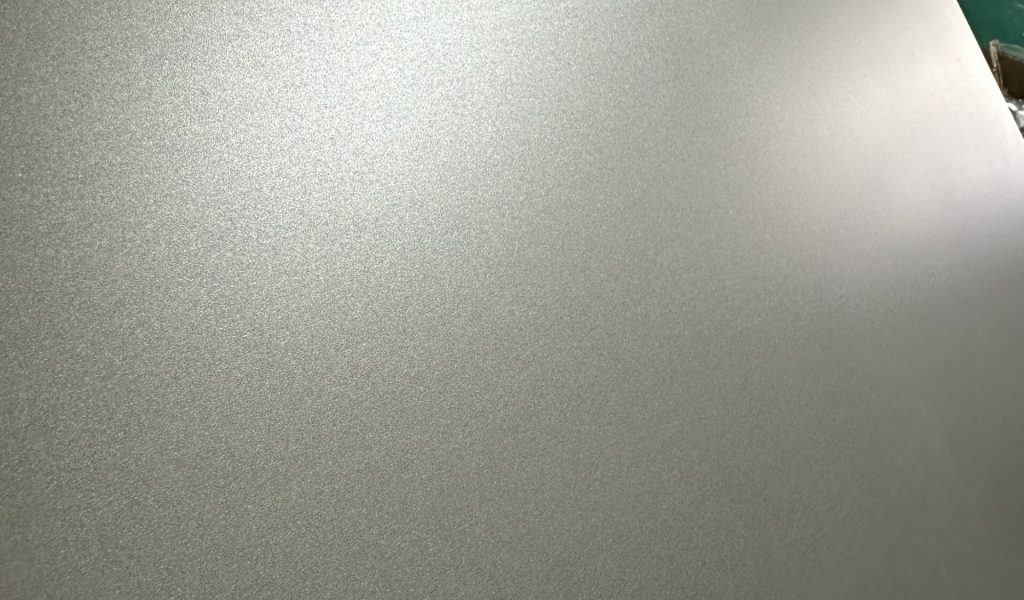
Figure No.2 Hard Anodizing of Aluminum Alloy Effect
FAQ about Hard Anodizing of Aluminum Alloy
Table of Contents
How High a Hardness can the Hard Anodizing of Aluminum Alloy Achieve?
Due to the differences in the specific materials of the aluminum alloy and the process parameters, the hardness of the aluminum alloy after hard anodizing will also vary. Generally speaking, it can reach around HV300-1200.
How About the Corrosion Resistance of the Aluminum Alloy after Hard Anodizing?
Hard anodizing significantly enhances the corrosion resistance of aluminum alloy. The thick and dense oxide film formed on its surface can effectively prevent the contact between external corrosive media and the aluminum alloy matrix.
In a general atmospheric environment, the aluminum alloy after hard anodizing can maintain good appearance and performance for a long time. Yinlu has specifically carried out professional salt spray tests on the aluminum alloy that has undergone hard anodizing.
Aluminum alloys with different film thicknesses and different materials can respectively withstand hundreds or even thousands of hours of salt spray corrosion without obvious corrosion phenomena.
However, in some extreme environments, additional protective measures are still required to further enhance its corrosion resistance.
What Color Options Are There for the Hard Anodizing of Aluminum Alloy?
Common colors include black, gray, golden yellow, etc., and black is a color that is used relatively frequently.
Will Hard Anodizing Affect the Dimensional Accuracy of Aluminum Alloy?
During the hard anodizing process, an oxide film will grow on the surface of the aluminum alloy, so it will definitely cause a change in the size of the aluminum alloy.
It should be noted that the growth of the oxide film is uniform. Generally, experienced sheet metal fabrication manufacturers will reserve a certain machining allowance in advance during the design and processing to compensate for the dimensional changes.
For the processing of precision parts, it is necessary to precisely control the thickness of the oxide film to meet the requirements of dimensional accuracy.
Under normal circumstances, for every 10μm increase in the thickness of the hard anodized oxide film layer, the size of the aluminum alloy part will increase by approximately 10μm on a single side.
What is the General Thickness of the Hard Anodized Oxide Film Layer of Aluminum Alloy?
In general industrial applications, the film thickness is usually between 25μm and 150μm.
If a higher wear resistance is required, the thickness is typically selected within the range of 50μm to 150μm.
In special fields such as aerospace, the thickness may even exceed 150μm.
Is the Cost of Hard Anodizing of Aluminum Alloy High?
There are many factors that affect the cost.
Firstly, it is the material. The costs of hard anodizing of aluminum alloys with different grades are different.
Secondly, it is the thickness of the oxide film layer. The thicker the film layer is, the more processing time and raw material consumption are required, and thus the higher the cost will be.
If it is mass production in large quantities, the cost will be relatively lower.
Generally speaking, compared with ordinary anodizing, the cost of hard anodizing is about 20% to 50% higher. The specific cost still needs to be determined according to the actual processing requirements.
Can the Surface of the Aluminum Alloy after Hard Anodizing Undergo Other Processing?
You can perform other processing, such as grinding and polishing. However, note that excessive mechanical processing may damage the integrity of the oxide film and affect its performance.
In addition, you can also apply painting treatment to further improve the decorative and protective properties. But remember to perform proper surface pretreatment before painting to ensure good adhesion between the coating and the oxide film.
How to Maintain the Surface of the Aluminum Alloy After Hard Anodizing?
Regular cleaning is required. You can use a soft cloth or sponge dipped in a neutral cleaning agent to gently wipe the surface to remove dust, dirt, and other pollutants.
Avoid touching sharp objects to prevent scratching the oxide film and causing mechanical damage.
After cleaning, rinse it thoroughly with clean water and dry it promptly to prevent corrosion caused by water residue.
If there are slight scratches on the surface, you can use fine sandpaper to gently sand it, and then perform a polishing treatment to restore the smoothness of the surface.
Conclusion
Whether you are seeking high-wear-resistant surface treatment solutions for components or require custom sheet metal fabrication project development, our professional team is committed to combining cutting-edge R&D capabilities with proven production experience to deliver one-stop solutions, ensuring every detail meets your requirements.
We welcome you to contact us : [email protected]