Quality to achieve the future
In today’s highly competitive manufacturing field, the quality of sheet metal processing products is extremely important. As a professional sheet metal processing enterprise, we deeply understand that quality is the lifeline of an enterprise and the key to winning customer trust. At Yinlu, from the selection of raw materials to the delivery of final products, we strictly control quality in every link of sheet metal processing production and are committed to providing customers with high-quality and reliable sheet metal products.
Quality management policy and objectives
·Customer-centric, committed to providing high quality custom sheet metal products
·Continuous improvement, the pursuit of excellent quality
·Ensure product compliance with relevant standards and regulations
Document management system
Quality manual
·Clarify the quality policy and quality objectives of the enterprise, and determine the direction for the quality development of the enterprise
·Standardize the management of production equipment and facilities and ensure that personnel engaged in sheet metal processing have the corresponding skills and knowledge to perform their jobs.
·Standardize the process flow of sheet metal processing, including the operation requirements and technical standards of each link such as cutting, stamping, bending, welding, surface treatment, etc., to ensure the stable and reliable processing quality of the products.
·Specify the methods, standards and equipment for quality inspection to ensure the accuracy and reliability of inspection results
Program Files
·It stores all the links from order receipt to product delivery, including contract review, design control, procurement management, production process control, inspection and testing, non-conforming product control, corrective and preventive measures and other procedures.
Record File
·Keep various records in quality management activities, such as inspection reports, daily production reports, equipment maintenance records, etc., for traceability and analysis
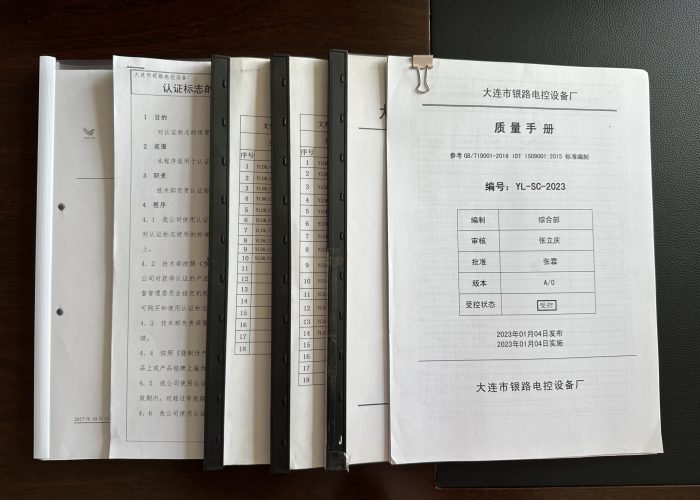
Figure NO.1 Quality control document
Supplier Management System
Supplier selection and evaluation
·We have established strict supplier selection criteria to evaluate suppliers’ quality assurance capabilities, delivery dates, and prices, and regularly conduct performance evaluations on suppliers to eliminate unqualified suppliers in a timely manner.
Supplier quality control
·We have signed a quality assurance agreement with suppliers, which clearly defines quality requirements and liability for breach of contract. We also conduct incoming inspections on raw materials and parts provided by suppliers to ensure that they meet quality standards.
Production process management system
Make production plan
·Formulate a reasonable production plan, optimize production scheduling, improve production efficiency and equipment utilization, and ensure on-time delivery of products.
Process Control
·Develop detailed sheet metal processing process documents to ensure process stability and consistency.Monitor and record key process parameters, such as cutting size, bending angle, welding parameters, etc.
Equipment management
·Establish equipment maintenance system, regularly maintain and maintain the equipment to ensure that the equipment is in good running condition.Calibrate and verify key equipment to ensure accuracy and reliability
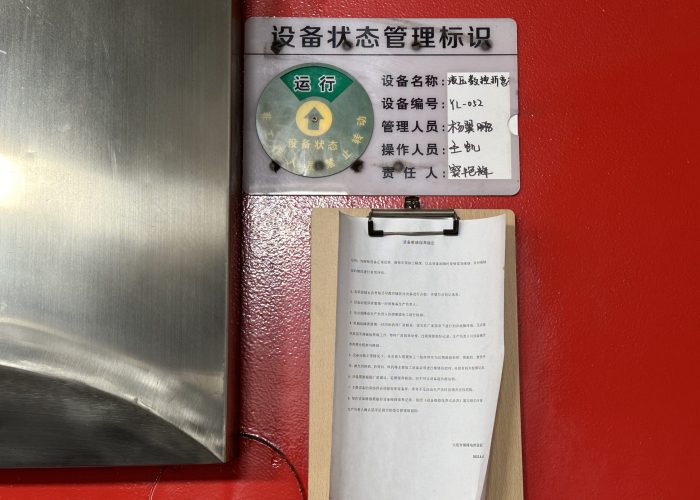
Figure NO.2 Equipment Management
Site Management
·Implement 5S management (finishing, rectification, cleaning, cleaning, quality) to keep the production site clean and orderly.Identify and manage work in progress during production to prevent confusion and misuse.
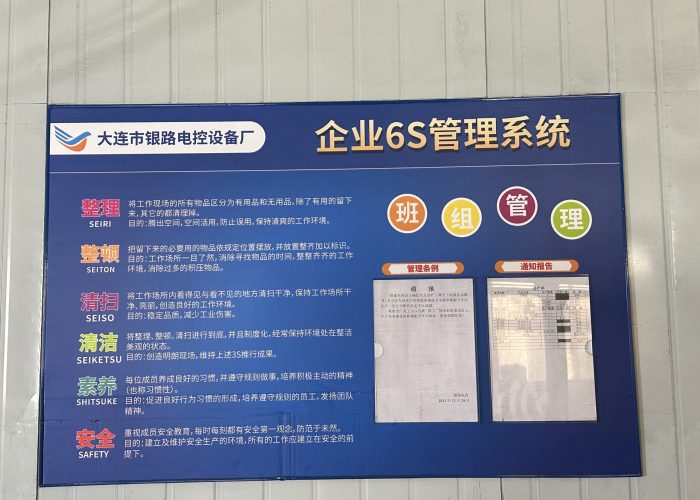
Figure NO.3 6S Site Management
Inspection and testing system
Incoming inspection
·Strict incoming inspection of raw materials and parts to ensure that their quality meets the requirements.
·Establish sampling inspection plan and conduct full inspection of key raw materials.
Process Inspection
·Set up a number of inspection points in the production process to check the key processes to ensure that the product meets the process requirements.
·Find and correct quality problems in time by means of first inspection, inspection and final inspection
Final inspection
·Conduct comprehensive inspection and testing of finished products to ensure that products meet quality standards and customer requirements.
·Issue inspection report, record inspection results and nonconformities.
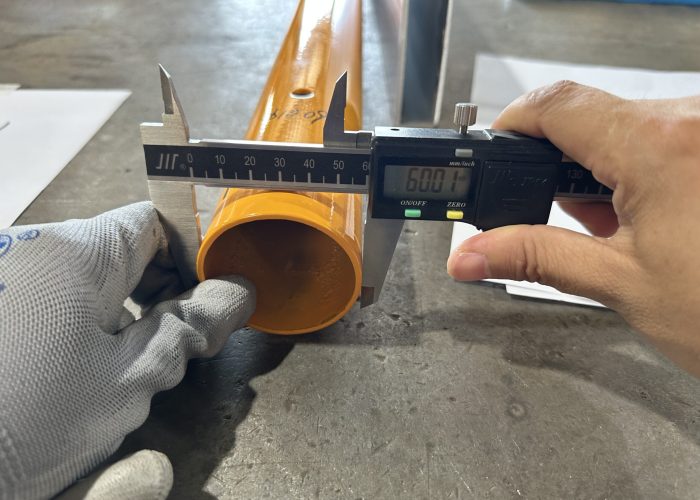
Figure NO.4 Quality Control Process”
Defective Product Management System
Identification and isolation
·Establish a nonconforming product identification mechanism to discover and identify nonconforming products in time.
·Isolate unqualified products to prevent them from being mixed into qualified products.
Review and Disposal
·Organize relevant departments to review nonconforming products and determine disposal methods, such as rework, repair, scrap, etc.
·Reinspect the products after rework and repair to ensure that they meet the quality requirements.
Correction and prevention
·Analyze the causes of nonconforming products, formulate corrective and preventive measures to prevent similar problems from happening again.
·Track and verify the implementation effect of corrective and preventive measures.
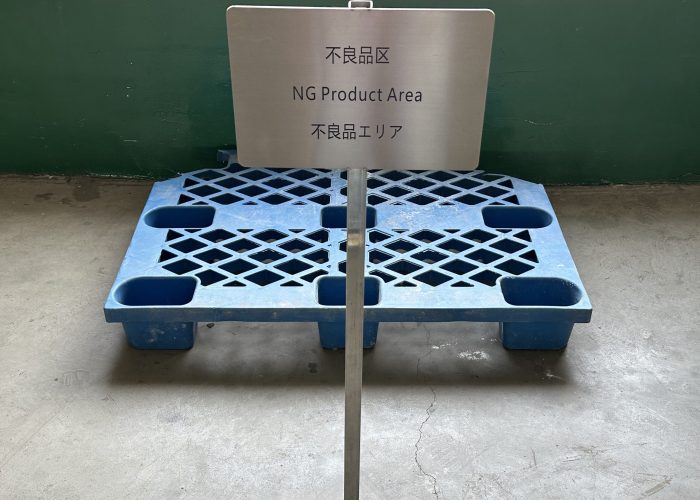
Figure NO.5 Defective Product Area