Table of Contents
Electrochemical Polishing of Stainless Steel
Electrochemical polishing is an electrochemical machining process. Based on the principle of electrolysis, during the polishing process, stainless steel is immersed in a specific electrolytic solution.
After the power supply is connected, electrochemical dissolution occurs on the surface of the stainless steel, gradually making the surface smooth and shiny, thus achieving the polishing effect.
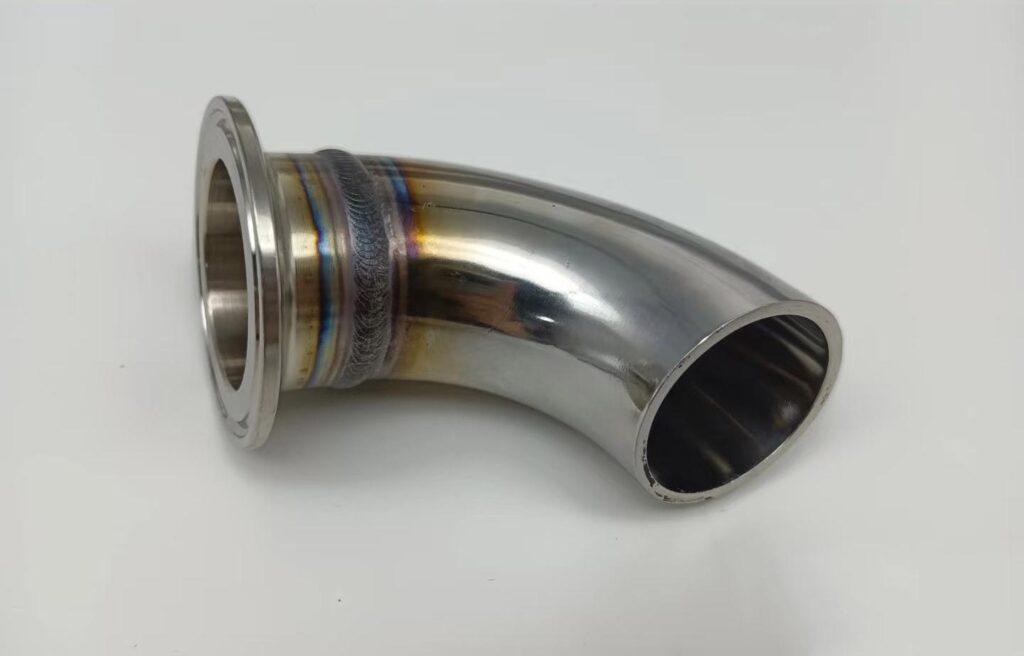
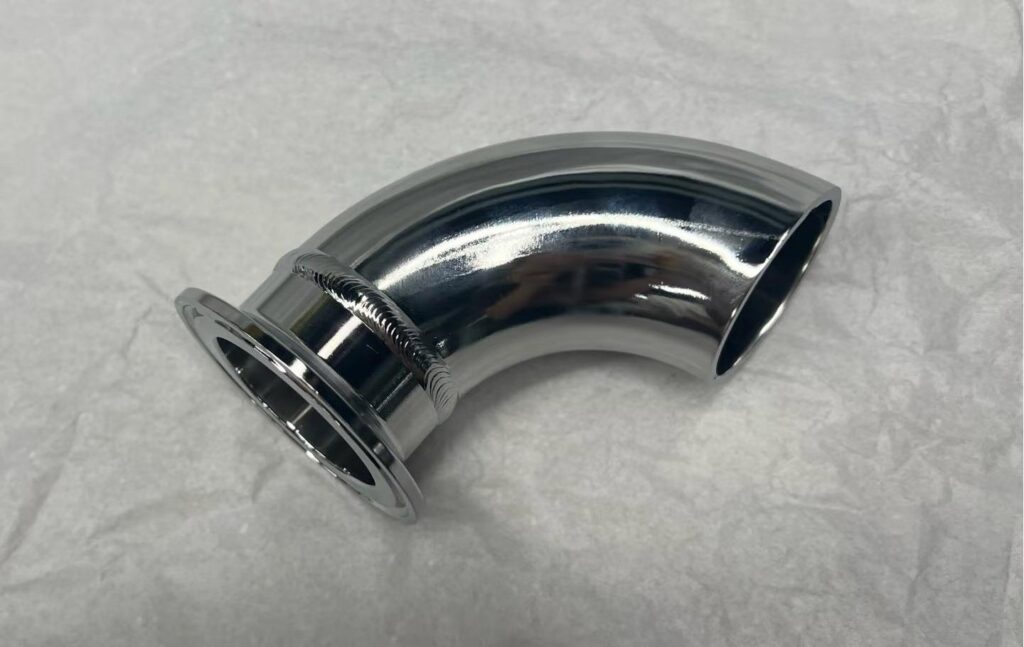
- Betty
Advantages of Electrochemical Polishing of Stainless Steel
High Surface Quality
It can achieve a more uniform, delicate and shiny surface, even reaching a mirror – like effect. Moreover, the surface flatness is superior to that of mechanical polishing and chemical polishing.
No Mechanical Stress
During the polishing process, there is no mechanical deformation or stress concentration.
High Processing Efficiency
For workpieces with complex shapes, we can polish multiple surfaces simultaneously. Compared with mechanical polishing, where we need to process each surface one by one, electrochemical polishing is much more efficient.
Good Consistency
In mass production, the polishing quality consistency among different workpieces is high, ensuring the stability of product quality.
Improved Corrosion Resistance
Through electrochemical polishing, we can remove surface impurities and defects and form a denser oxide film, enhancing the corrosion resistance of stainless steel.
What are the Components and Proportions of the Electrolytic Solution?
The main components of common electrolytic solutions for electrochemical polishing of stainless steel include phosphoric acid, sulfuric acid, chromic acid (due to environmental protection issues, some processes have reduced or avoided its use), additives, etc.
Taking the phosphoric acid-sulfuric acid type electrolytic solution as an example, the common proportioning range is roughly phosphoric acid (60%-80%), sulfuric acid (10%-30%), with the rest being water and a small amount of additives (such as corrosion inhibitors, brighteners, etc.).
The specific proportioning will be adjusted according to factors such as the material of the stainless steel, the polishing requirements, and the equipment conditions.
How to Maintain and Replace the Electrolytic Solution?
Maintenance:
Regularly detect parameters such as the density, component concentration, and temperature of the electrolytic solution. Promptly replenish the water and components of the electrolytic solution that have been lost due to evaporation and consumption.
Remove impurities and precipitates in the electrolytic solution through filtration to keep the electrolytic solution clean. Control the current density and time during the polishing process to avoid excessive consumption of the components of the electrolytic solution.
Replacement:
When the impurity content in the electrolytic solution is too high and we cannot effectively remove the impurities through methods such as filtration, which affects the polishing quality;
Or when the component ratio of the electrolytic solution is seriously out of balance and we cannot restore it to an appropriate range even after replenishment and adjustment, we need to replace the electrolytic solution.
Generally, we determine the replacement cycle according to the number of workpieces produced, the polishing effect, and the detection situation of the electrolytic solution.
How does the Corrosion Resistance of the Stainless Steel Surface Change after Electrochemical Polishing? And by How Much can it be Improved?
After electrochemical polishing, electrochemical polishing will significantly improve the corrosion resistance of the stainless steel surface.
On the one hand, the polishing process removes active sites such as surface impurities, micro – cracks, and defects, reducing the starting points of corrosion. On the other hand, electrochemical polishing forms a more uniform and dense passive film, which hinders the contact between the corrosive medium and the substrate.
The specific degree of improvement varies depending on factors such as the material of the stainless steel, the composition of the electrolytic solution, and the parameters of the polishing process. Generally speaking, in the same corrosive environment, the corrosion resistance can be improved by 2 – 5 times or even more.
What are the Precautions for the Subsequent Treatment after the Electrochemical Polishing of Stainless Steel?
Cleaning:
Use deionized water or distilled water to rinse the surface multiple times. Make sure you completely remove all the residual electrolytic solution on the surface, and prevent the residual electrolytic solution from corroding the stainless steel surface.
During the cleaning process, pay attention to the direction and strength of the water flow to avoid damaging the polished surface.
Passivation:
Carry out passivation treatment with an appropriate passivation solution (such as a nitric acid solution, etc.) to further improve the corrosion resistance of the stainless steel. Adjust the passivation time and temperature according to the material of the stainless steel and the formulation of the passivation solution. Generally, the passivation time is 10 to 30 minutes.
After passivation, you should rinse the stainless steel thoroughly again with deionized water and dry it in a timely manner to prevent rust from forming on the surface.
How to Achieve an Environmentally Friendly Electrochemical Polishing Process?
Use Chromium-Free Electrolytic Solutions: Avoid using electrolytic solutions containing heavy metals such as chromium. Develop and apply environmentally friendly electrolytic solution formulations, such as those based on organic acids.
Recycling and Treatment of Electrolytic Solutions: Establish an electrolytic solution recycling system to treat and regenerate the used electrolytic solutions, reducing the discharge of electrolytic solutions.
Wastewater Treatment: Effectively treat the wastewater generated during the electrochemical polishing process. Remove heavy metal ions and harmful chemical substances through methods such as neutralization, precipitation, and filtration to make the wastewater meet the discharge standards.
Optimize Process Parameters: Reasonably adjust parameters such as the current density, time, and temperature during polishing to improve the utilization rate of the electrolytic solution, and reduce the consumption and pollution of the electrolytic solution.
What are the Factors that Affect the Polishing Efficiency?
Stainless Steel Material: Different grades of stainless steel have different chemical compositions and microstructures, which will also lead to differences in the speed and effect of electrochemical polishing. For example, stainless steel with a relatively high nickel content is relatively easier to polish.
Composition of the Electrolytic Solution: The composition and proportioning of the electrolytic solution directly affect the polishing speed and quality. Appropriate components of the electrolytic solution can improve the polishing efficiency, while inappropriate ones will reduce it.
Current Density: Within a certain range, increasing the current density can accelerate the polishing speed. However, an excessively high current density will lead to defects such as over-polishing and burning of the surface. Therefore, it is necessary to control it within an appropriate range.
Temperature: The temperature of the electrolytic solution has a significant impact on the polishing efficiency. Appropriately increasing the temperature can accelerate the diffusion rate of ions and improve the polishing efficiency. However, if the temperature is too high, problems such as excessive evaporation of the electrolytic solution and changes in its composition will occur.
Shape and Size of the Workpiece: For workpieces with complex shapes, due to the uneven distribution of current, some areas may be under-polished or over-polished, affecting the overall polishing efficiency. Large workpieces require a larger current and a longer time to complete the polishing.
Electrode Layout: A reasonable electrode layout can make the current distribution more uniform and improve the polishing efficiency. Conversely, an unreasonable electrode layout will lead to uneven current distribution, affecting the polishing effect and efficiency.
>>> Back to Surface Treatment Guide