Table of Contents
Corrosion Protection Solutions for Metal Enclosure in Marine Environment
- Betty
In the marine environment, metal enclosure face extremely severe corrosion challenges. Seawater is rich in various salts, dissolved oxygen, microorganisms, etc., which can cause electrochemical corrosion and chemical corrosion to metals, seriously affecting the performance and service life of metal enclosures.
Therefore, adopting effective anti-corrosion treatment solutions is crucial for protecting metal enclosures in the marine environment.
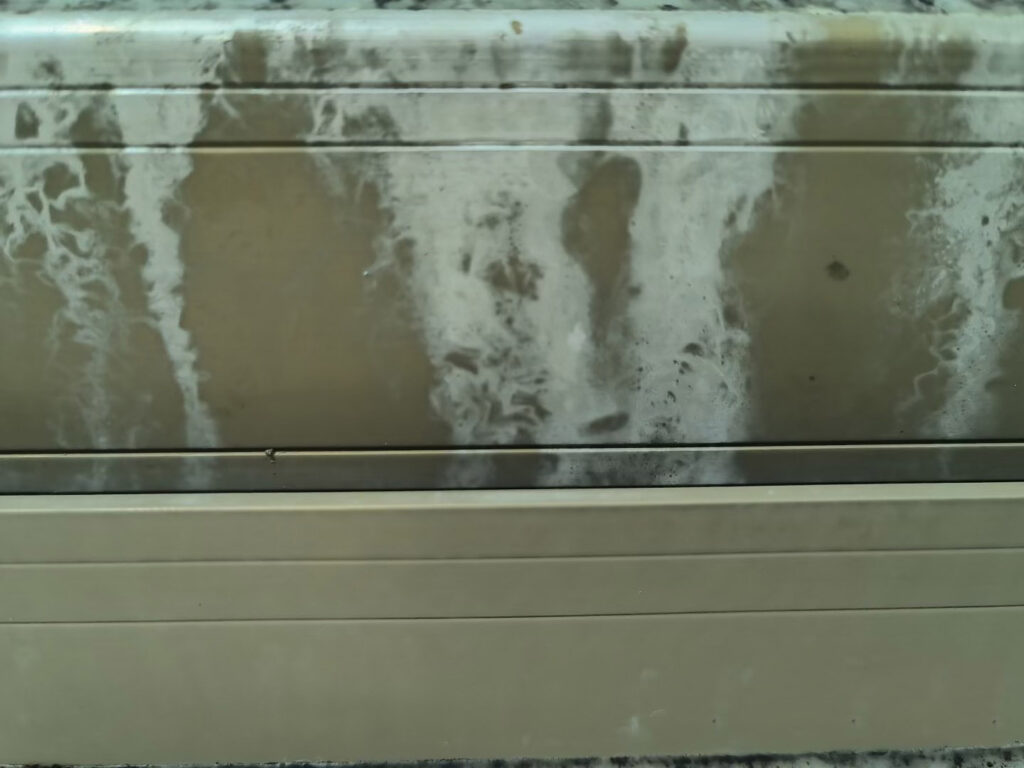
Figure No.1 Marine Corrosion Effect
Anti-Corrosion Treatment Scheme
Surface Coating Protection
Coating Selection
When selecting coatings for metal enclosures, we should adopt high-performance marine anti-corrosion coatings as much as possible, such as epoxy zinc-rich primer, chlorinated rubber finish paint, etc.
The epoxy zinc-rich primer has a good cathodic protection effect. Zinc powder can form a sacrificial anode on the metal surface to protect the metal substrate.
The chlorinated rubber finish paint has excellent resistance to seawater and chemical corrosion, as well as good adhesion.
Coating Process
Before painting, considering the highly corrosive characteristics of the marine environment, we should conduct strict pretreatment on the surface of the metal enclosure, including rust removal, degreasing, cleaning, etc., to ensure that the surface roughness meets the requirements.
After the pretreatment, we generally need to inspect the surface roughness to ensure that it meets the requirements of the painting process, so as to enhance the bonding force between the coating and the metal surface, enabling the coating to protect the metal enclosure for a longer time in the highly corrosive marine environment.
When spraying, according to the shape, size, usage environment of the metal enclosure in different projects, as well as the characteristics of the coating, we should flexibly select the spraying method. We must strictly control the thickness and uniformity of the coating. After the spraying is completed, we can use a coating thickness gauge for measurement to ensure the coating quality, so as to effectively isolate the metal from the contact with seawater and air in the marine environment.
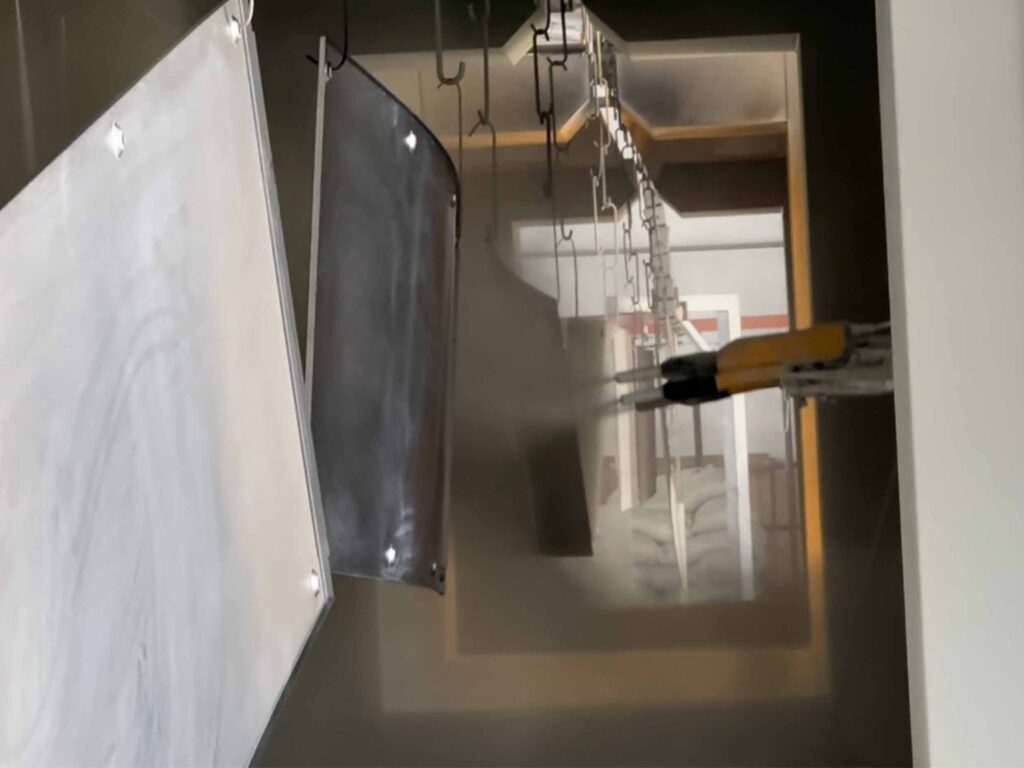
Figure No.2 Powder Coating Process
Metal Plating Protection
Galvanizing
Hot-dip galvanizing is a commonly used method for metal plating. We immerse the metal enclosure in molten zinc to form a dense zinc layer on the metal surface.
This zinc layer not only isolates the metal from seawater but also acts as a sacrificial anode to provide protection to some extent.
Nickel Plating
Nickel plating can enhance the hardness and corrosion resistance of the metal surface. It is especially suitable for metal enclosures that require high standards in terms of appearance and wear resistance.
The nickel-plated layer has good chemical stability and can effectively resist the corrosion of seawater.
Anodic Protection
Sacrificial Anode Method
In the marine environment, due to the fact that seawater is rich in various salts and has good electrical conductivity, metal enclosures are extremely prone to corrosion. In order to effectively protect the metal enclosures, we can install sacrificial anodes, such as zinc alloys and magnesium alloys.
As time goes by, the anodes continuously dissolve in the seawater and keep releasing electrons. These electrons will flow towards the metal shells, protecting them and effectively preventing the corrosive effect of seawater on the metal shells.
It is just like putting on an invisible “protective coat” for the metal enclosures to resist the erosion of seawater.
Impressed Current Method
In the complex and changeable marine environment, the impressed current method is an effective means to further enhance the protection of metal enclosure.
An external power source applies cathodic current to the metal enclosures, making the metal shell act as a cathode in seawater and thus suppressing the corrosion of the metal.
Antifouling Treatment
Antifouling Coatings
Antifouling coatings, such as organotin antifouling coatings and tin-free self-polishing antifouling coatings, are applied to the surface of the metal shell. The active substances in the antifouling coatings can inhibit the attachment and growth of marine organisms on the metal surface, reducing the impacts of microbial corrosion and biological fouling.
Mechanical Antifouling
We use mechanical devices such as scrapers and brushes to regularly remove the dirt and biological attachments on the surface of the metal shell, maintaining the cleanliness of the metal surface.
Evaluation of Anti-corrosion Effect
Appearance Inspection
Regularly inspect the appearance of the metal shell. Observe whether there are phenomena such as peeling, cracking, and blistering of the coating, and check if there are situations like corrosion and discoloration of the metal plating.
Thickness Measurement
Use a coating thickness gauge to measure the thickness of the coating and the plating layer to ensure that their thickness meets the design requirements.
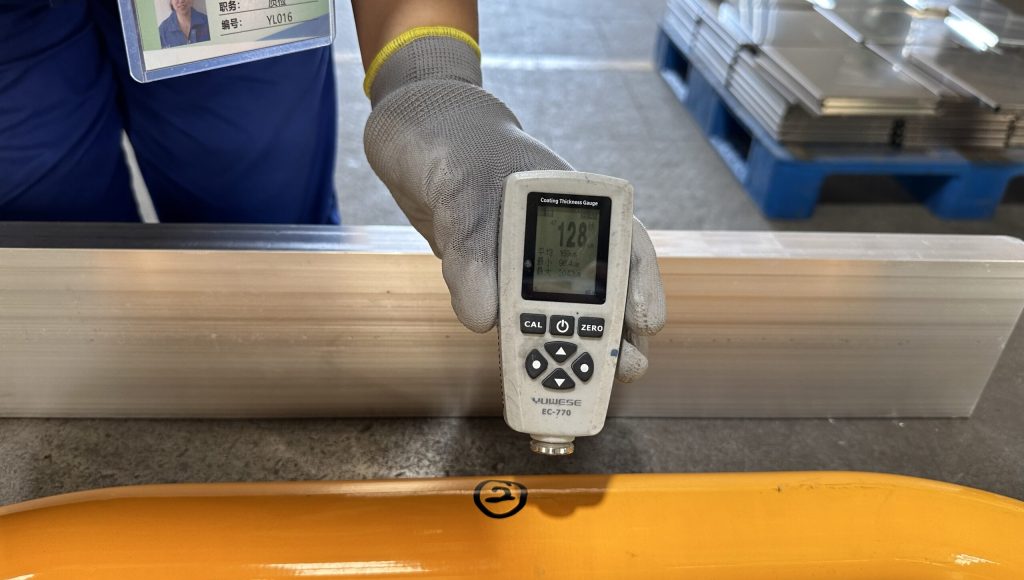
Figure No.3 Coating Thickness Measurement
Electrochemical Testing
Adopt electrochemical methods, such as potential measurement and polarization curve testing, to evaluate the corrosion rate and protection effect of the metal enclosure.
Biological Fouling Inspection
Check the biological fouling situation on the surface of the metal shell and evaluate the effectiveness of the antifouling treatment.
Analysis of Corrosion Characteristics of Different Metal Materials in Marine Environments
Carbon Steel
Carbon steel undergoes general corrosion in seawater due to electrochemical action, with an annual corrosion rate of 0.1–0.3 mm/a.
When in contact with metals having a more positive potential such as copper and stainless steel, carbon steel acts as the anode, leading to accelerated corrosion. For example, when steel is coupled with copper, the corrosion rate of steel increases by 3 to 5 times.
Stainless Steel
In marine environments, the corrosion of stainless steel mainly takes the form of localized corrosion and galvanic corrosion. In stagnant seawater, the rate of pitting depth growth is approximately 0.05–0.1 mm/a.
When coupled with titanium alloys or copper alloys, stainless steel acts as the anode, leading to accelerated corrosion. In the coupled system, for each doubling of the cathode-to-anode area ratio, the corrosion rate of stainless steel increases by 1.5 to 2 times.
Galvanized Steel
The corrosion of galvanized steel is predominantly sacrificial anode corrosion of the zinc layer. When the zinc layer is damaged, it initiates accelerated galvanic corrosion.
The surface of galvanized steel is coated with a zinc layer, which acts as the anode and preferentially dissolves, slowing down further corrosion.
However, once the zinc layer is damaged, galvanic corrosion accelerates. In this case, the annual corrosion rate of zinc increases from 0.08 mm to 0.3 mm, and red rust appears on the steel beneath the zinc layer within 3 months. When coupled with copper or stainless steel, the corrosion rate of zinc increases by 2 to 3 times.
Aluminum and Aluminum Alloy
The corrosion of aluminum in marine environments is primarily characterized by localized corrosion and galvanic corrosion triggered by oxide film damage.
Aluminum quickly forms a dense aluminum oxide protective film on its surface in marine environments, which can prevent further corrosion to a certain extent.
This material is similar to galvanized steel—when the protective film is damaged, its corrosion resistance drops rapidly, with the pitting depth growth rate reaching approximately 0.05 mm/a. When aluminum is coupled with steel, copper, or stainless steel, it acts as the anode, causing its corrosion rate to increase by 5 to 10 times.