Sheet Metal Fabrication Material Selection Guide
Appropriate material selection can ensure that the product has sufficient strength, good corrosion resistance, an attractive appearance, and a reasonable cost. Therefore, understanding the characteristics and selection methods of sheet metal processing materials is of great significance for those engaged in the sheet metal processing industry as well as enterprises and individuals who need to use sheet metal products.
Author: Betty Release Time: 2024-11-13
Considerations for material selection
·Usage
The specific performance requirements such as the strength needs, corrosion resistance, electrical conductivity, and thermal conductivity of the product should be taken into account.
·Cost
Prices of different materials vary greatly, and so do the processing costs. Therefore, we need to consider both the price of materials and the processing costs comprehensively to select the most economical materials.
·Process
The adaptability of different materials to processes such as cutting, stamping, and bending should also be taken into account. If the product requires welding, then materials with good welding properties need to be selected.
·Appearence
Different materials can undergo different surface treatments to achieve various appearance effects.

Figure No.1 Material Comparison
Sheet metal material classification
By type of material
- Cold rolled sheet metal material
- Galvanized sheet metal material
- Stainless steel sheet metal material
- Aluminum sheet metal material
- Copper sheet metal material
Yinlu offers a variety of sheet materials for customers to choose from, covering different types such as cold-rolled sheets, galvanized sheets, stainless steel sheets, and aluminum sheets. Each type of sheet has its own unique features and can meet the diverse needs of customers in different projects.
304
It is the most common austenitic stainless steel. Its chemical composition mainly contains about 18% chromium (Cr) and about 8% nickel (Ni), along with small amounts of elements such as carbon (C) and manganese (Mn).
The chromium element enables the formation of a dense chromium oxide protective film on the surface of the stainless steel, endowing it with excellent corrosion resistance.
316
In terms of chemical composition, besides containing chromium (about 18%) and nickel (about 10% – 14%) in proportions similar to those of 304 stainless steel, it also has about 2% – 3% molybdenum (Mo) added.
The addition of the molybdenum element further enhances the corrosion resistance of the stainless steel in highly corrosive environments such as seawater and chlorine-containing media.
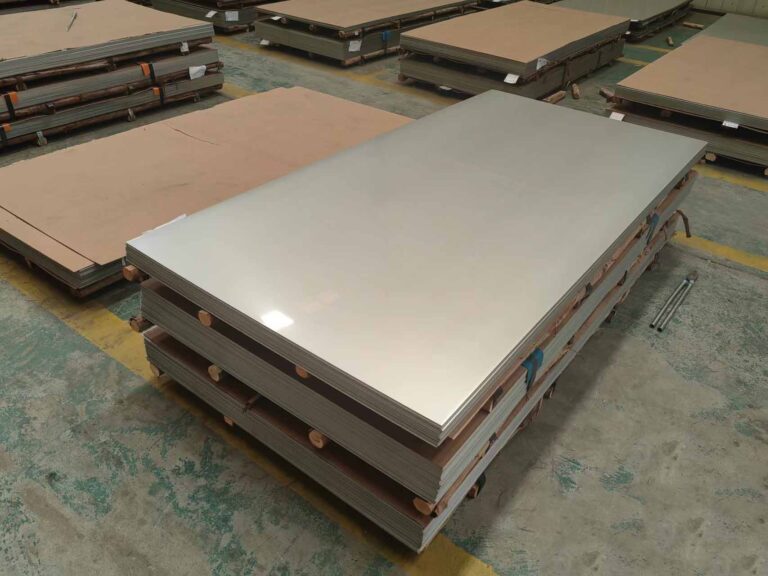
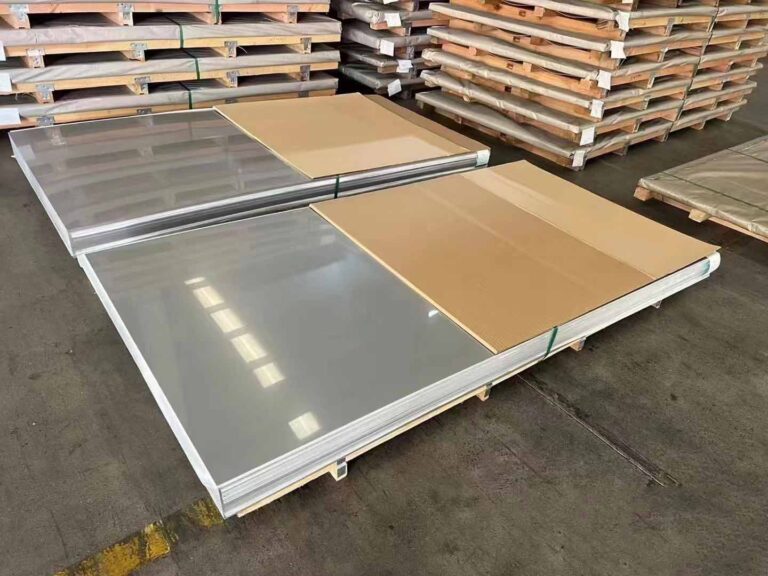
Figure No.2 Stainless Steel Material Display
Aluminum
6061
The main alloying elements are magnesium (Mg) and silicon (Si), and it also contains small amounts of elements such as copper (Cu), manganese (Mn), and iron (Fe).
It is at a medium strength level among aluminum alloys, possessing good toughness, excellent formability, weldability, and machinability, and is also easy to form.
Excellent corrosion resistance
Good oxidation resistance
7075
The main alloying elements are zinc (Zn), magnesium (Mg) and copper (Cu). It belongs to high-strength aluminum alloys, and the proportion of its alloy components endows it with unique performance characteristics.
It is one of the aluminum alloys with relatively high strength, much higher than that of 6061 aluminum alloy. Besides its high strength, it also has a relatively high hardness, which makes it perform excellently in terms of wear resistance and deformation resistance.
Relatively poor machinability
Specific welding requirements
General corrosion resistance
Good oxidation resistance
In sheet metal processing, 6061 aluminum alloy is widely used due to its good comprehensive performance. While 7075 aluminum alloy, relying on its characteristics such as high strength and high hardness, has important applications in specific fields where extremely high requirements for strength and hardness are imposed.However, it also has a relatively high processing difficulty.
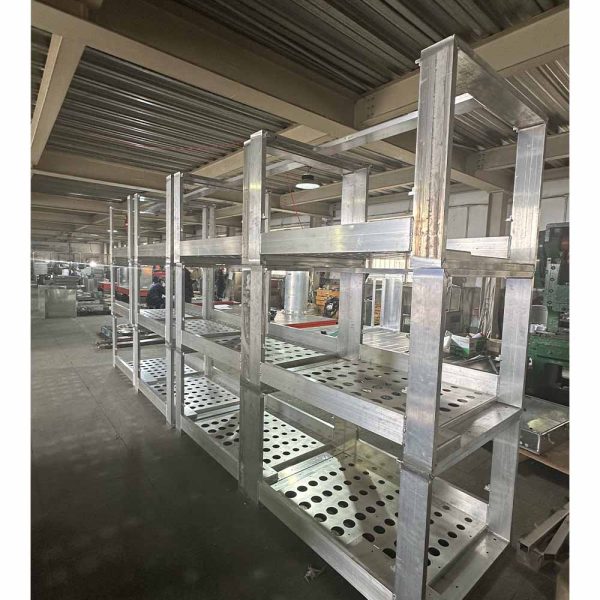
Figure No.3 Aluminum Frame
Conclusion
Material selection is a crucial step in the sheet metal processing, which directly affects the quality, performance and cost of the products. When choosing materials, we need to consider factors such as the use of the products, performance requirements and cost comprehensively to select the most suitable ones.
If you need our assistance, you can contact us at www.yinlu-sheetmetal.com.