A process in which a solid powder coating is uniformly attached to the surface of the sheet metal workpiece by electrostatic adsorption and then cured by heating to form a strong coating.In the sheet metal parts after cutting, bending, welding and other processes, powder coating can play a role in protection and beautification.
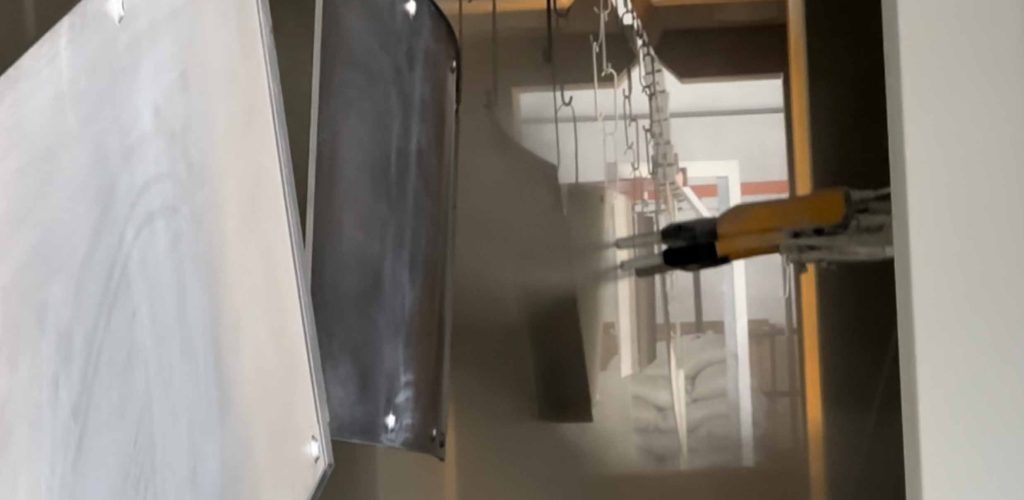
Figure No.1 Our Automatic Powder Coating Line
Classification of powder coating
Each type of powder coating has its own characteristics and applicable fields. In actual applications, we can select the appropriate powder coating type according to the specific requirements of the object to be coated, such as appearance, performance, and environment.
They have the characteristics of environmental protection, good coating performance, diverse appearance and high efficiency and energy saving
Thermosetting powder coating
- High strength
- Excellent corrosion resistance
- Good performance for 5-10 years or even longer
Thermoplastic powder coating
- Good flexibility
- Recyclable
- It can usually maintain an effective life of 3-8 years.
Powder coating workflow
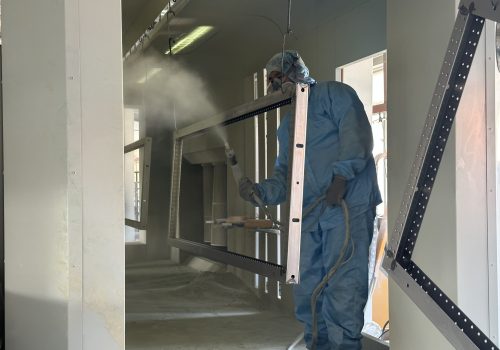
Surface pretreatment
Before applying the powder coating, we need to pretreat the surface of the object to be coated (usually metal products, such as sheet metal parts). This step is of crucial importance. The purpose is to ensure that the surface is clean, dry, and has good adhesion so that the powder coating can attach better. Common pretreatment methods include:
- Degreasing
- Derusting
- Phosphating or Passivating.
Electrostatic powder coating
This is the core step in the powder coating process. We use electrostatic action to evenly spray the powder coating onto the surface of the object that has gone through pretreatment.
Leveling treatment
After the electrostatic powder spraying is completed, the powder coating particles on the object’s surface are only initially attached together. Their distribution may not be very even, and the surface may not be smooth enough. At this time, leveling treatment is required.
The purpose is to make the powder coating particles further integrate and flow under the action of their own gravity and surface tension, thus making the surface smoother and flatter.
Curing treatment
Although the powder coating on the object’s surface is relatively evenly distributed after the leveling treatment, it hasn’t formed a firm coating yet. We need to complete this transformation through heating and curing.
Post-treatment
After the curing treatment is completed, steps like cooling in the post-treatment process are still required to ensure that the quality and appearance of the coating meet the requirements.
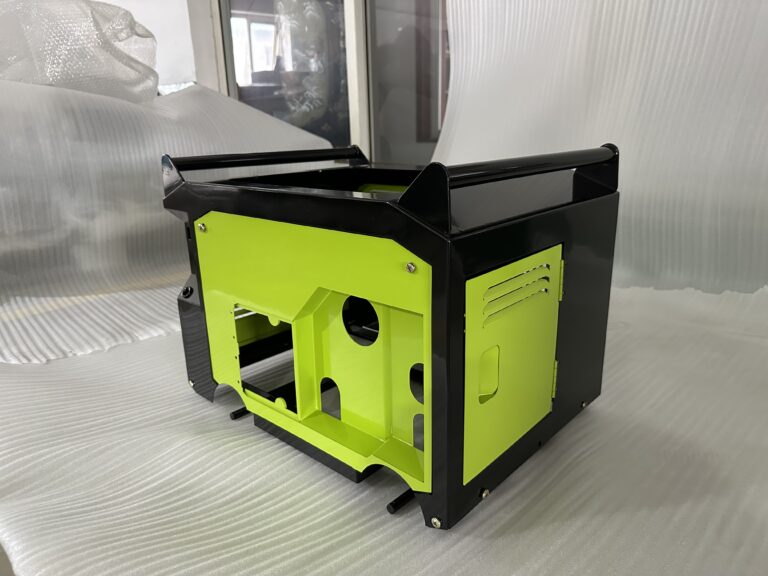
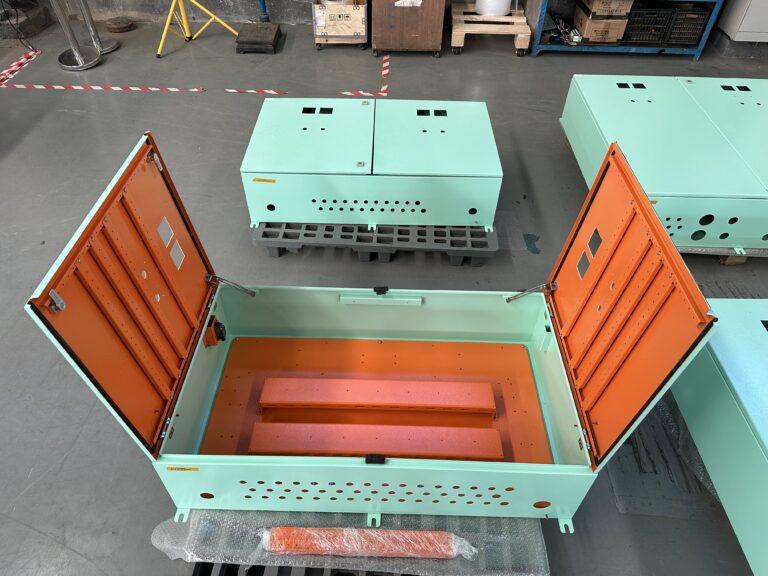
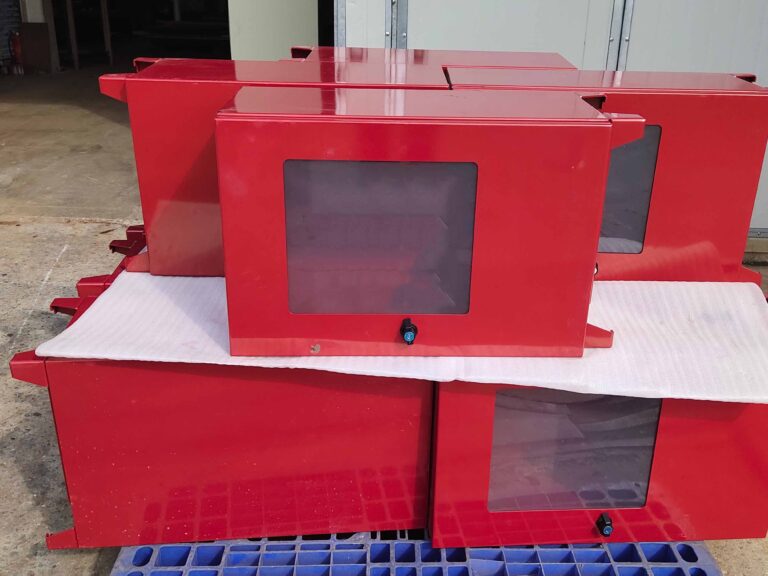
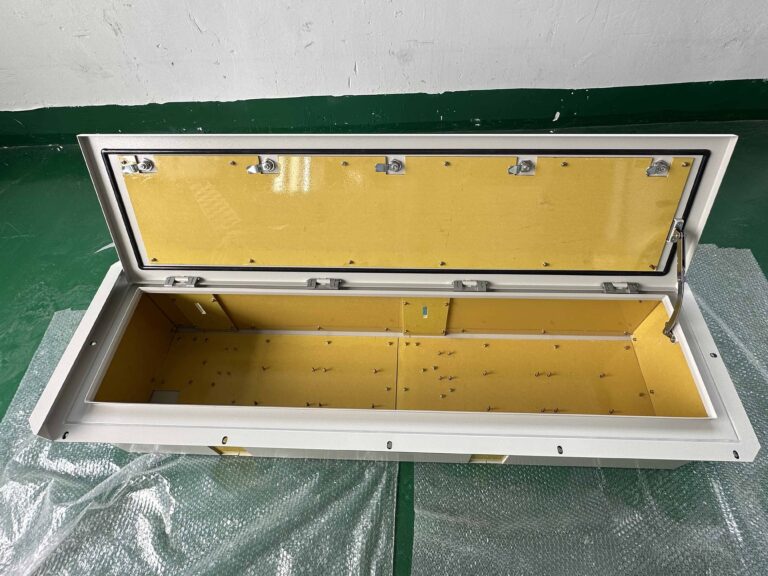
Figure No.2 Multiple powder coating color options
Application in sheet metal fabrication
Improve the appearance quality of sheet metal parts:
1.Available in a variety of colors and effects
2.Achieve a uniform and beautiful coating
Enhance the durability of sheet metal parts
1.Excellent corrosion resistance
2.Excellent wear resistance
Meet environmental requirements
1.Low volatile organic compound (VOC) emissions
2.Recyclable
Improve production efficiency
1.Quick spray and one molding
2.Simplified process flow
Conclusion
Powder coatings are applicable to various metal materials, such as iron, aluminum, copper, zinc, etc., as well as metal products of different shapes and sizes, including flat surfaces, curved surfaces, and complex structures.
Whether it is large metal structural components or small metal parts, powder coating can be adopted for them.
You can learn more on our website yinlu-sheetmetal.com