Table of Contents
What solutions can Yinlu provide for galvanized sheet metal!
- Betty

Figure No.1 Galvanized sheet metal material
What is galvanized sheet metal
Galvanized sheet metal is a type of steel plate with a zinc coating layer on its surface. This protective layer enhances the performance of the steel plate, endowing it with excellent corrosion resistance so that it can still maintain good performance even in harsh environments.
Types of galvanized sheet metal
Classification according to galvanizing process
Hot-dip Galvanized steel plate
It is made after the steel plate is pretreated, the steel plate is put into the zinc liquid, the zinc is attached to the surface of the steel plate to form a zinc layer, and it is cooled.
Its zinc layer is thicker, so it is resistant to corrosion
Electro-galvanized steel plate
To ensure that the surface of the steel plate is free of impurities,
The steel plate as the cathode, zinc plate as the anode, into the electrolyte containing zinc ions.
The process by which the zinc layer is deposited on the surface of the steel plate through electrolysis by switching on the DC power supply.
Its zinc layer is thin and uniform, the surface quality is good, but the corrosion resistance is relatively weak
Alloy Galvanized steel plate
It is also needs to be pre-treated first, and the steel plate is immersed in the alloy molten liquid containing zinc and other alloying elements (such as aluminum, magnesium, etc.), so that the alloy is attached to form the alloy layer. Then it is made by cooling, leveling and other processing processes.
It has good corrosiveness, but also has the characteristics of self-repair of surface scratches under certain conditions
Characteristics of galvanized steel plate
- Corrosion resistance
The zinc coating of galvanized steel plate gives it excellent corrosion resistance. - Durability
The galvanized steel plate can endure harsh environmental conditions, and this also benefits from its sturdy zinc coating. - Aesthetic
It has a silver appearance and can also undergo powder coating treatment according to different situations. - Formability
It can ensure that no obvious cracking or damage occurs to the coating layer when being bent or cut.
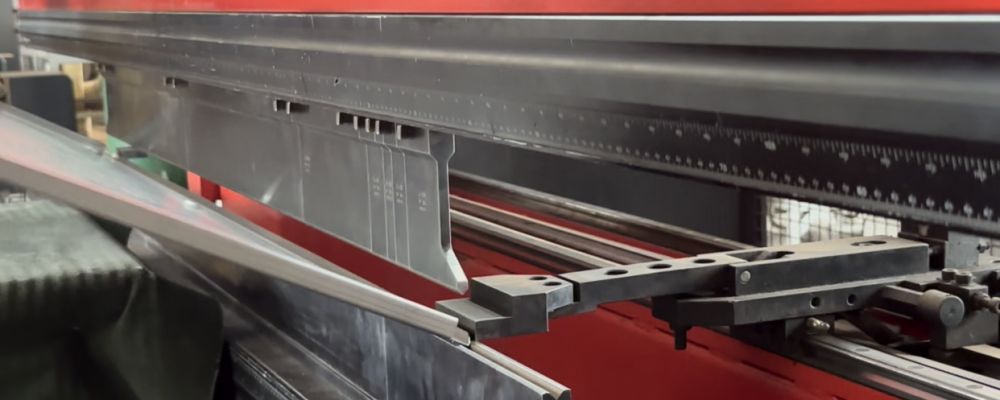
Figure No.2 Galvanized sheet metal bending process
How to control the thickness of zinc layer in the galvanizing process
Time control: In the hot-dip galvanizing process, the longer the steel plate stays in the zinc liquid, the thicker the zinc layer will be. Therefore, it is necessary to precisely control the zinc immersion time, which can be achieved through automated production line equipment. In this way, the residence time of the steel plate in the zinc liquid can be accurately controlled.
Temperature control: The temperature of the zinc liquid is also an important factor affecting the thickness of the zinc layer. Generally, a temperature range of 440 °C – 460 °C for the zinc liquid is more appropriate.
Adjustment of current density: In the electro-galvanizing process, the current density is a key parameter for controlling the thickness of the zinc layer. It is necessary to reasonably adjust the current density according to factors such as the material, size and galvanizing requirements of the steel plate.
Management of zinc ion concentration: Generally speaking, it is more appropriate to maintain the concentration of zinc ions in the electroplating solution within the range of 10 – 20 g/L.
The different thickness of zinc layer has influence on the properties of galvanized sheet metal
Corrosion Resistance:
Thin zinc layer (less than 10μm): It is suitable for indoor environments or outdoor environments with relatively low humidity.
Medium-thickness zinc layer (10 – 20μm): The zinc layer of this thickness can provide good corrosion resistance in various environments. The protection time can reach 5 – 10 years.
Thick zinc layer (more than 20μm): The thick zinc layer performs excellently in harsh corrosive environments. For example, in marine environments.
Processing Performance:
The galvanized sheet metal with a thin zinc layer is relatively easy to process. During the processing of the galvanized sheet metal with a medium-thickness zinc layer, attention should be paid to the adjustment of processing parameters. While the galvanized sheet metal with a thick zinc layer is relatively difficult to process and requires more professional equipment and precise process parameters during the processing.
Appearance Quality:
The galvanized sheet metal with a thin zinc layer usually has a bright and smooth appearance.
The galvanized sheet metal with a medium-thickness zinc layer has good appearance quality. The existence of the zinc layer can cover up some tiny flaws of the steel plate substrate and make the surface smoother.
The thick zinc layer may make the galvanized sheet metal look a bit bulky. If the zinc layer is uneven, there may be an uneven surface.
Maintenance cycles in different environments
- Indoor dry environment
Since the environment is relatively stable, a simple surface cleaning once a year will do. - Indoor humid environment
In an environment with relatively high humidity, there may be a certain threat of corrosion to the zinc coating. You can conduct an inspection once every three to six months. Meanwhile, try to keep the indoor humidity within a reasonable range ( <= 60%). - Outdoor mild environment
In a general natural environment, it is recommended to conduct an inspection once every six to twelve months. - Harsh outdoor environment
Sea water, strong winds, heavy rain, high humidity will cause erosion of galvanized sheet metal, so it is necessary to check and maintain in time. Usually 3-6 months or even less.
We have advanced powder coating equipment and technologies, which will help you further extend the service life of galvanized steel plate products. Contact Yinlu if you needed.
How to deal with rust
- Mild rust spot
You can mix a small amount of mild detergent with warm water to prepare a mild detergent solution. Dip a sponge into it and gently wipe the galvanized plate.
Finally, thoroughly rinse the galvanized plate with clean water. Or use a rust remover specifically designed for galvanized sheet metal surfaces. - Moderate to heavy rust spots
Use finer sandpaper to gently sand in a circular motion to remove the rust layer.
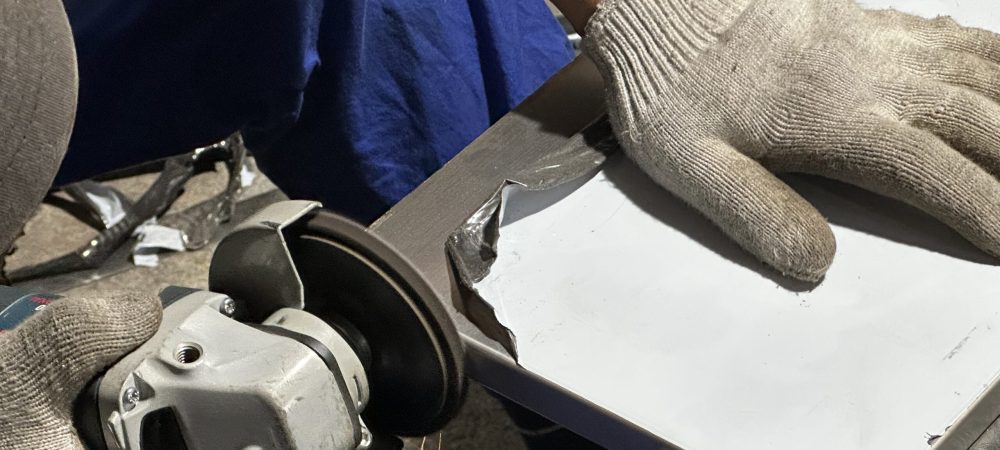
Figure No.3 Galvanized sheet metal rust removal process
Benefits of using galvanized sheet metal
Cost effective
Although the initial cost of galvanized sheet steel is slightly higher, its longer service life and lower maintenance requirements make it a cost-effective choice in the long run. Fewer replacements and repairs mean a reduction in overall costs.
Environmental protection
The galvanizing process helps extend the service life of sheet steel, reducing the need for frequent replacements and thus saving resources.Moreover, both the sheet steel and the zinc coating can be recycled, which makes it an environmentally friendly choice.
Multifunction
The numerous applications of galvanized steel plate in various industries prove its versatility and value.
What products can galvanized sheet metal do
Due to the many products that can be made, the following only introduces the main products in the sheet metal fabrication industry
- Electrical enclosure
- Control cabinet
- Electrical cabinet
- Server cabinet
- Instruments
- Metal bracket
- Metal file cabinet
These are some of the products we produce, Yinlu can do more than just this, click here to learn more.
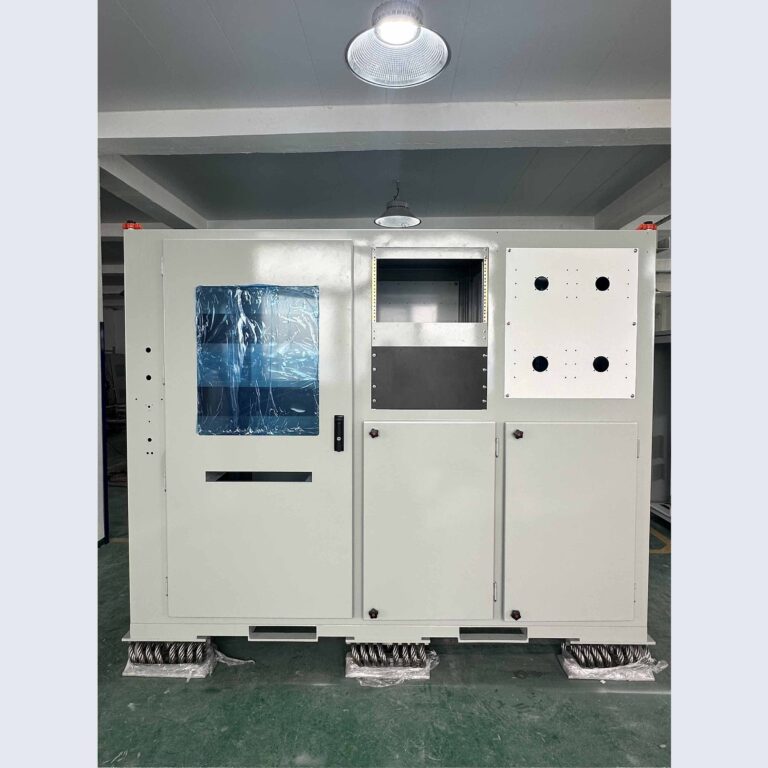
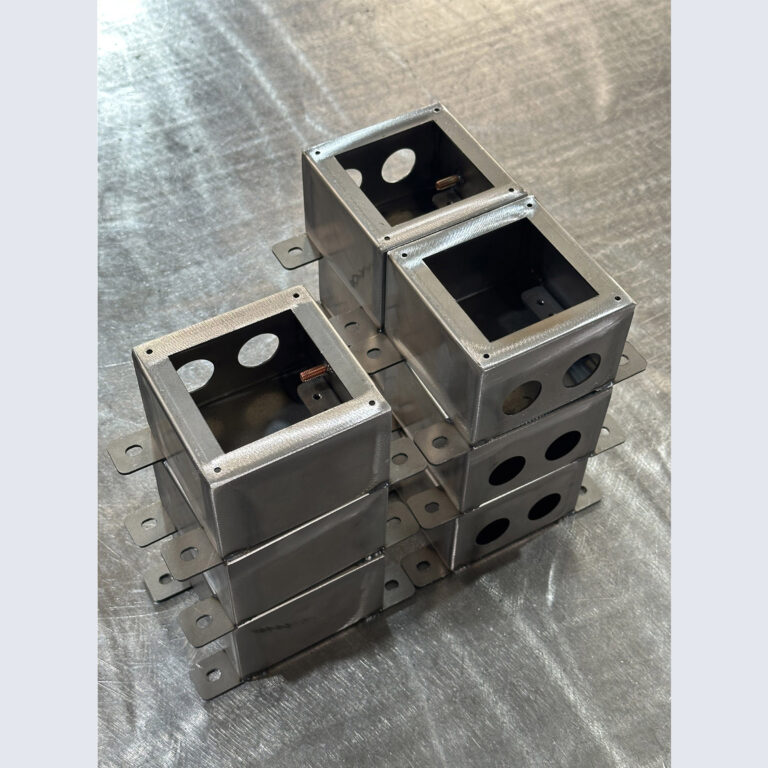
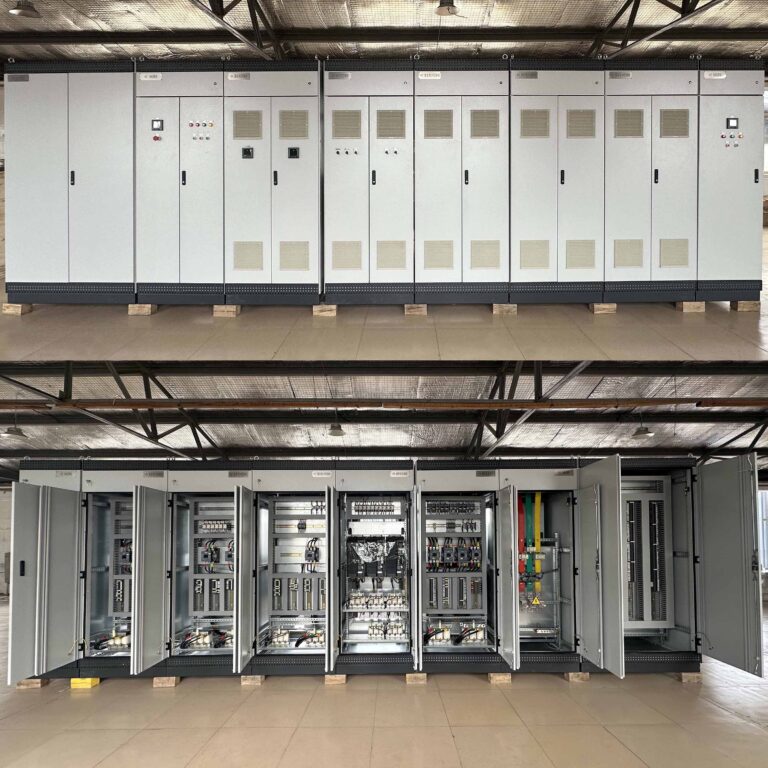
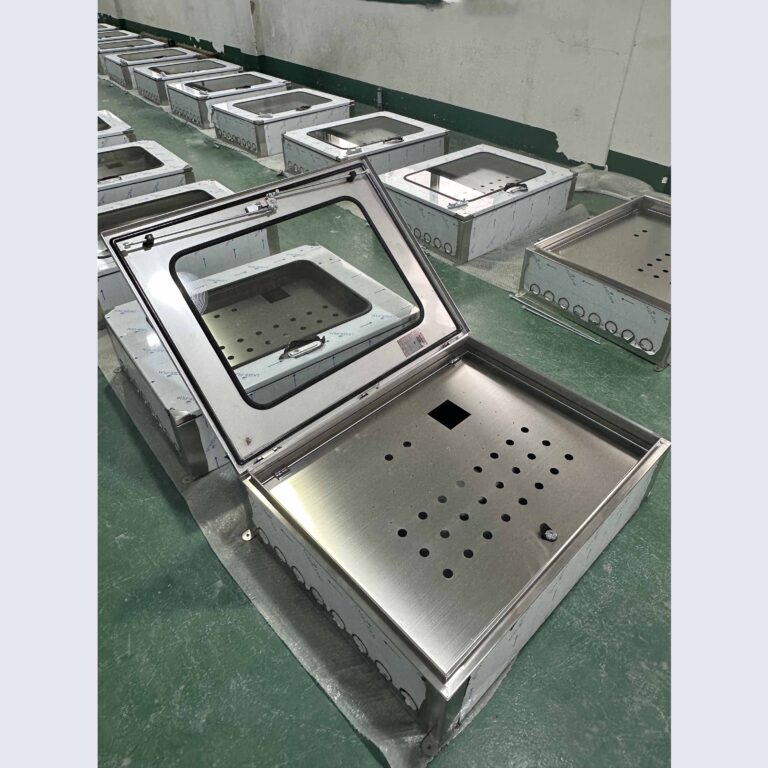
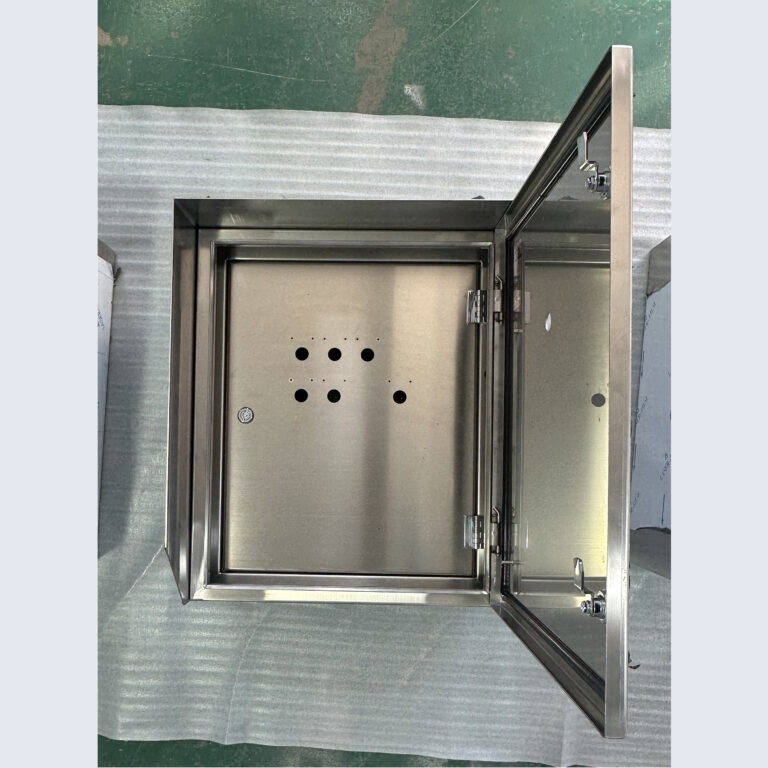
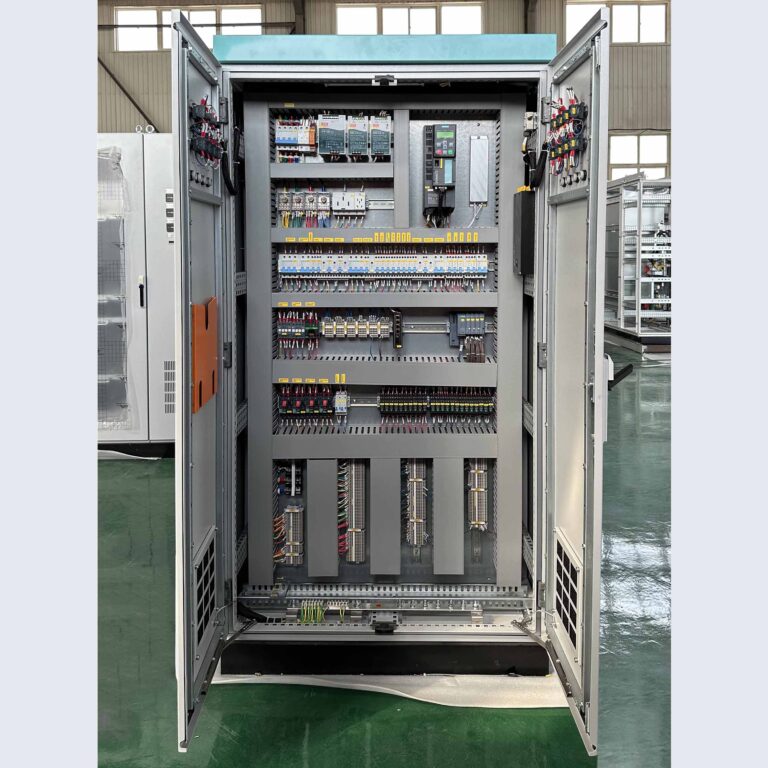
Conclusion
Galvanized sheet is an excellent material, no matter what industry you are engaged in, you can make full use of it, at Yinlu we ensure that it plays the best performance in your project,so contact us now.The most cost-effective solution awaits you.