Table of Contents
A Comprehensive Guide to Surface Treatment Methods
- Betty
The main purpose of this article is to help you understand the surface treatment processes used in the sheet metal processing industry. It will summarize them in all aspects and present them to you in the simplest and easiest-to-understand way.
>>> Please continue reading
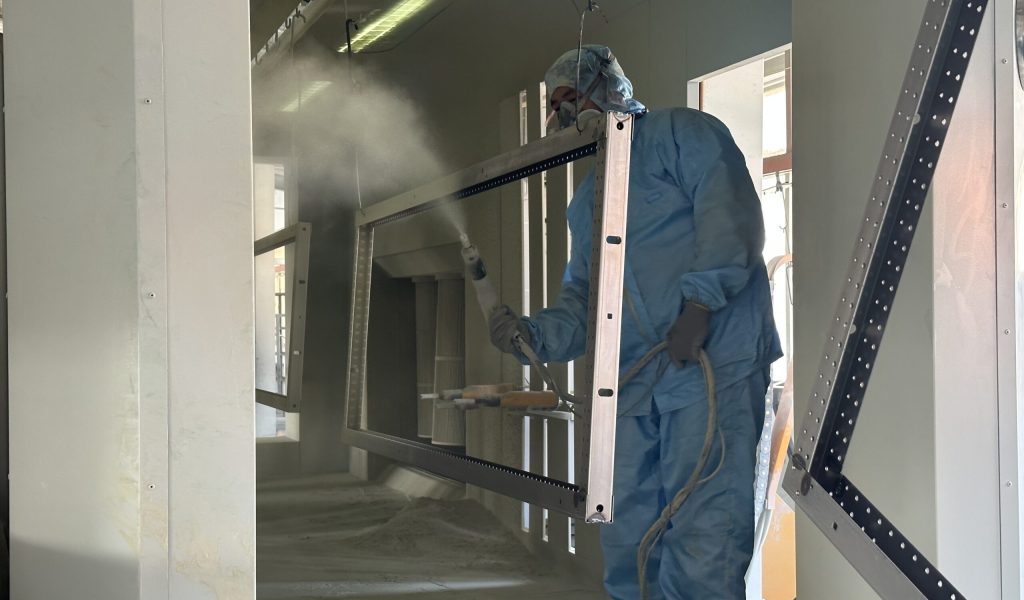
Figure No.1 Powder Coating
Surface treatment refers to the processing of the surfaces of metal or non-metal materials through physical, chemical or mechanical techniques to change their surface morphology, properties and so on.
Simply put, it means processing the surface to make it more durable and better-looking.
For example, metal objects are prone to rusting. At this time, surface treatment can make them less likely to rust and extend their service life.
What is surface pretreatment?
Surface pretreatment aims to ensure that the subsequent surface treatment can achieve better results.
Pretreatment can guarantee that the surface is smooth and even.
The surfaces of some metal materials may have problems like unevenness, protruding burrs and oxide scales. If surface treatment is carried out directly, good output results will definitely not be obtained.
Surface treatment processes used in sheet metal fabrication.
Mechanical treatment processes
Grinding: It focuses on removing the excess material on the surface of the workpiece with grinding tools to make the surface flat. For example, grinding wheels and other tools are used to grind the metal surface.
Polishing: Its main purpose is to make the surface of the object smoother and shinier. Usually, polishing pastes and other auxiliary materials are used together with polishing equipment to achieve this effect.
There are also various types of polishing methods. The most common ones are electrochemical polishing, mechanical polishing, and chemical polishing.
Read our detail guide on Electrochemical Polishing of Stainless Steel
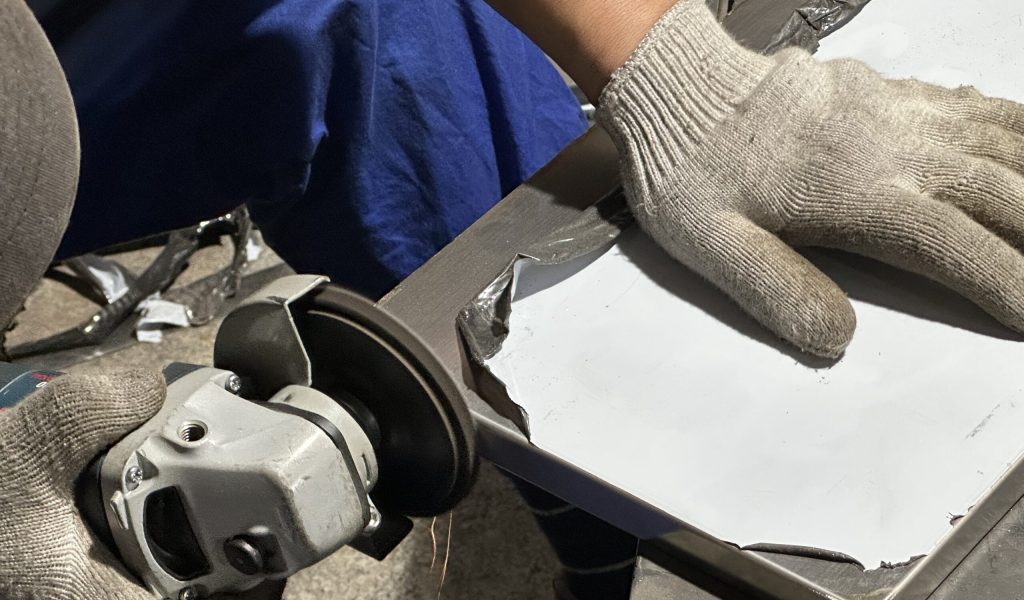
Figure No.2 Polishing
Sandblasting: It utilizes sand particles sprayed at high speed to impact the surface of the object, which plays roles in cleaning, roughening or changing the appearance of the surface.
Barrel finishing: Workpieces are put to roll together with abrasives in a barrel. Through the effect of mutual friction and so on, the quality of the workpiece’s surface is improved and the surface becomes smoother.
Brushing: Regularly rub the material surface repeatedly in a certain direction, and a filiform texture effect can be created on the material surface.
Chemical treatment processes
Pickling: It generally refers to a process that uses acidic solutions to remove impurities such as oxides and rust from the metal surface.
Alkali cleaning: It utilizes alkaline solutions to clean the surface of materials. It can remove oil stains, dirt and so on, and is often used for the surface pretreatment of metals and other materials.
Phosphating: It is mainly a chemical treatment process that forms a phosphate conversion film on the metal surface. It can enhance the corrosion resistance of metals and improve the adhesion of paint layers.
Passivation: It forms a passivation film on the metal surface through chemical methods, making the metal surface in a relatively stable and corrosion-resistant state.It can achieve better glossiness and color uniformity.
It is generally used for the surface treatment of stainless steel and other metals.
Degreasing: It aims to remove oil stains on the surface of metal sheets, laying a good foundation for subsequent electroplating and coating processes.
>>> Please continue reading
Electrochemical treatment processes
Electroplating: It refers to the process of plating a thin layer of other metals or alloys onto the surface of certain metals by using the principle of electrolysis. We take the metal parts to be plated as the cathode and put them in the electrolyte containing metal ions to be plated. Then, the metal ions deposit onto the surface of the parts under the action of electric current.
Anodizing: It is commonly used for metals like aluminum and aluminum alloys. We place the metal workpiece as the anode in an electrolyte solution. Through electrochemical action, an oxide film forms on its surface, which can improve the corrosion resistance, hardness and aesthetic appearance of the metal.
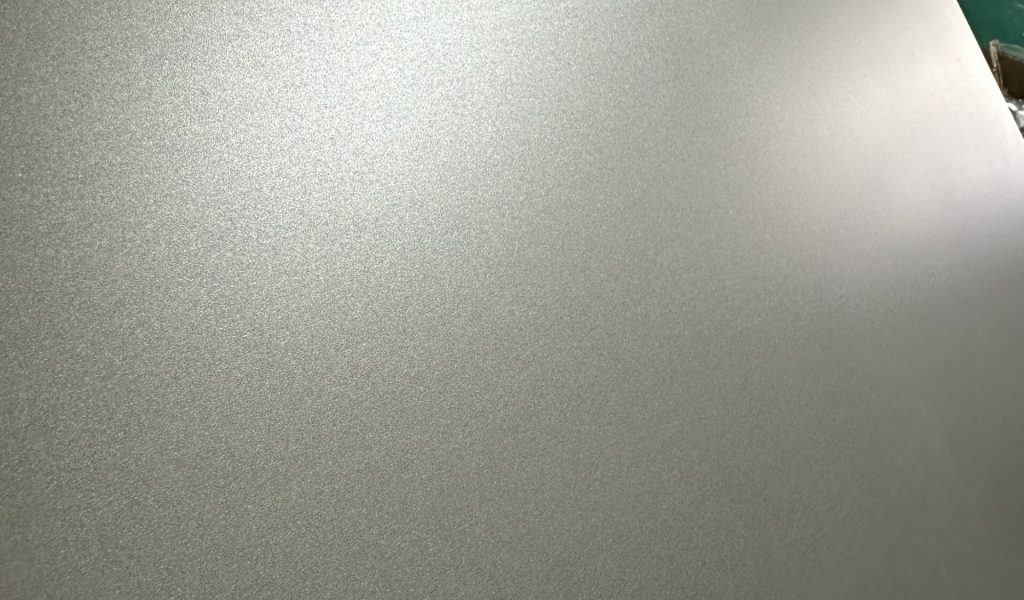
Figure No.3 Aluminum alloy hard anodized
Electroless plating: Also known as autocatalytic plating, it is a surface treatment method that does not rely on external current. Based on the principle of redox reaction, it uses appropriate reducing agents to make the metal ions in the solution reduce and deposit a metal coating on the surface of the workpiece with catalytic activity.
Coating processes
Brush coating: Use a paintbrush to dip in paint and then apply it on the surface of the workpiece according to certain painting methods, so that the paint evenly covers the workpiece surface. It is a relatively traditional coating method with relatively simple operation.
Spraying: With tools like spray guns, utilize compressed air or other power sources to spray materials such as paint and powder onto the surface of the workpiece in the form of mist, forming a uniform coating. This is a process with a relatively wide range of applications.
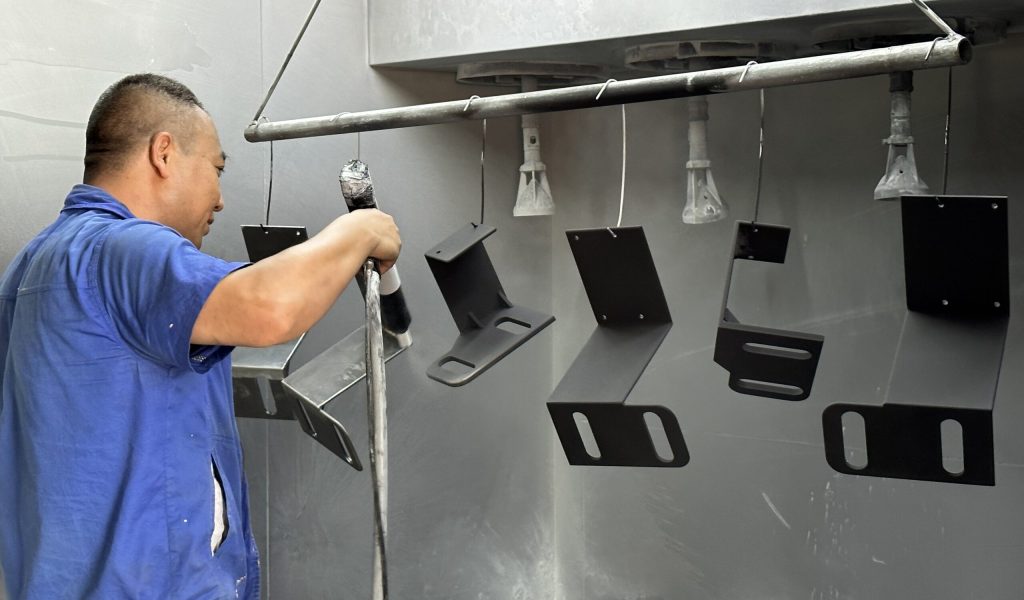
Figure No.4 Spray powder with a manual spray gun.
Electrophoretic coating: Immerse the workpiece in the water-based electrophoretic solution containing electrophoretic paint and then apply direct current. This makes the charged paint particles move towards the surface of the workpiece under the action of the electric field and deposit to form a coating. It is often used for coating in industries such as automobiles and home appliances.
Vapor deposition processes
Physical Vapor Deposition: Abbreviated as PVD, it is a process that, under vacuum conditions, uses physical methods (such as evaporation, sputtering, etc.) to convert source materials into gaseous atoms, molecules or ions, and then deposits them onto the substrate surface to form thin films.
Chemical Vapor Deposition: Abbreviated as CVD, it is a process that, under conditions like high temperature and vacuum, enables gaseous chemical substances to generate solid thin films on the substrate surface through chemical reactions.
Article summary
Generally speaking, grinding, polishing, sandblasting and barrel finishing are often used as surface pretreatment methods to improve the surface flatness and roughness of sheet metal parts.
They also lay the foundation for subsequent operations and ensure that the coating can adhere evenly and firmly to the surface of sheet metal parts when more precise surface treatments are carried out.
If there are problems such as oil stains, rust and oxide layers on the surface of raw materials, it is very useful to choose pickling or alkali cleaning before spraying work.
To prevent the paint layer from peeling off, phosphating can be carried out before painting. In this way, it can not only enhance the adhesion of the paint but also improve the corrosion resistance.
Passivation can further improve the corrosion resistance of stainless steel and galvanized steel, so that they are not easily corroded even in marine or harsher environments.
All the surface treatment processes mentioned in this article fall within the processing scope of Yinlu.
Since we are a professional customized sheet metal prototype manufacturer, we can provide you with one-stop full-process services from design to final delivery for your stainless steel enclosures, steel enclosures, electrical equipment and metal enclosures in various industries.
FAQ about surface treatment
Why is the pretreatment step before surface treatment important?
Pretreatment (such as cleaning, degreasing, and sandblasting) can remove surface impurities and improve the adhesion of the coating or plating layer. Ignoring this step may lead to blistering, peeling, or the failure of the process.
Stainless steel surface treatment methods
Mechanical polishing and electrolytic polishing: They can make the surface of stainless steel present a mirror-like shiny effect.
Wire drawing: The filiform lines formed on the surface add a unique texture to stainless steel.
Sandblasting: It can achieve a matte or frosted appearance.
Etching: It is able to create exquisite patterns on the surface of stainless steel, making it more artistically ornamental.
Spraying paint or powder spraying: They can achieve various color effects and enhance the overall aesthetics.
Pickling, passivation and electroless plating: They can enhance the corrosion resistance of stainless steel, making it durable for a long time.
Which surface treatment method can increase the hardness of aluminum surface?
Hard anodizing: It is an electrochemical treatment method that can effectively increase the surface hardness of aluminum or aluminum alloy materials. It greatly enhances the ability to resist friction and impact and effectively prolongs the service life.
Nickel plating is also an effective way to enhance the surface hardness of aluminum. The nickel layer itself has relatively high hardness. After being deposited on the surface of aluminum through electrolysis, it significantly improves the hardness. Meanwhile, it can also enhance the wear resistance, corrosion resistance and other properties of aluminum.
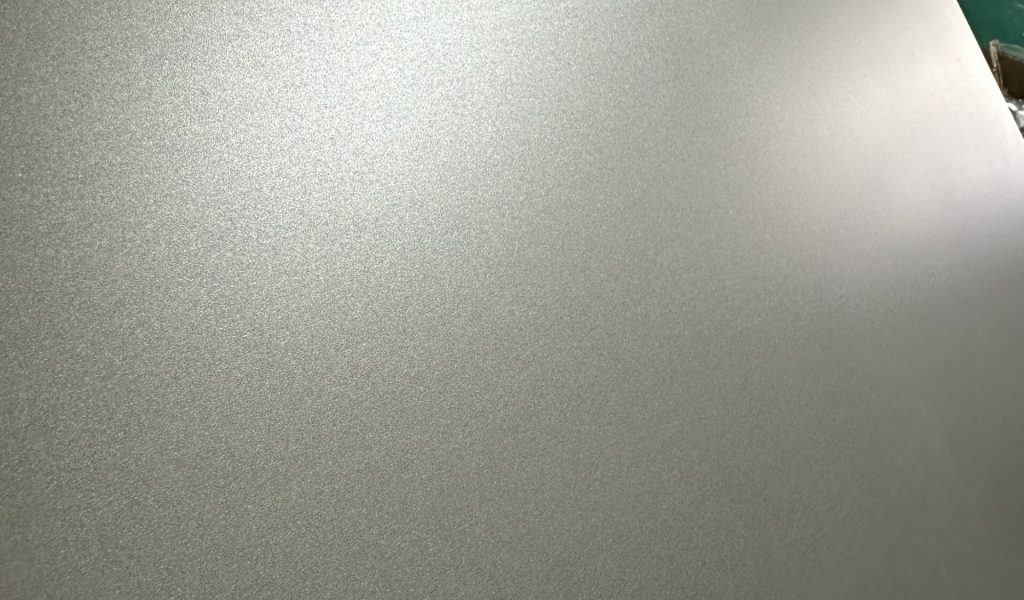
Figure No.5 Aluminum Alloy hard anodized
What are the differences between anodizing and electroplating?
Anodizing generates an oxide film on the surface of a metal through electrolysis (such as the oxide layer of aluminum), which is mainly used to enhance corrosion resistance and aesthetics.
Electroplating deposits metal ions onto the surface of the base material through electrolysis (such as nickel plating and chromium plating), and it is often used to improve electrical conductivity or for decorative purposes.
Is special maintenance required after surface treatment?
Yes. For example, electroplated parts need to avoid contact with corrosive liquids. The anodized surface should be cleaned regularly to prevent the accumulation of stains, and the sprayed coating may need to avoid being scratched by hard objects.
Whether you need small-batch trial production or large-scale processing, our customized sheet metal fabrication services can meet your precision and technological requirements. Contact us to get free technical consultation!