Sheet Metal Enclosure Manufacturer
- Multiple material options
- Quality assurance
- Personalized customization
Sheet Metal Enclosure Series Product
After 30 years of continuous development, we have continuously improved our sheet metal fabrication technology and product quality.
In the field of sheet metal enclosure processing, we have created many excellent customer cases. You can click here to view them.
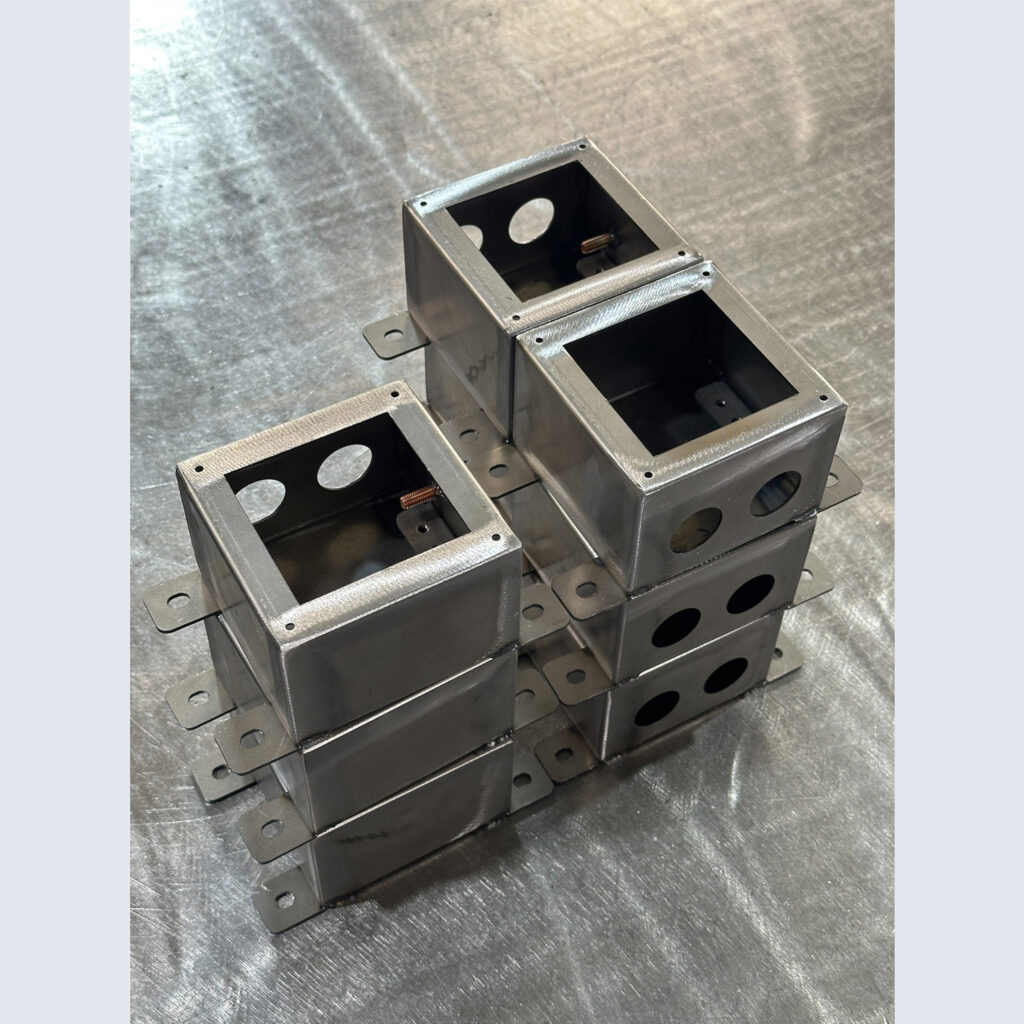
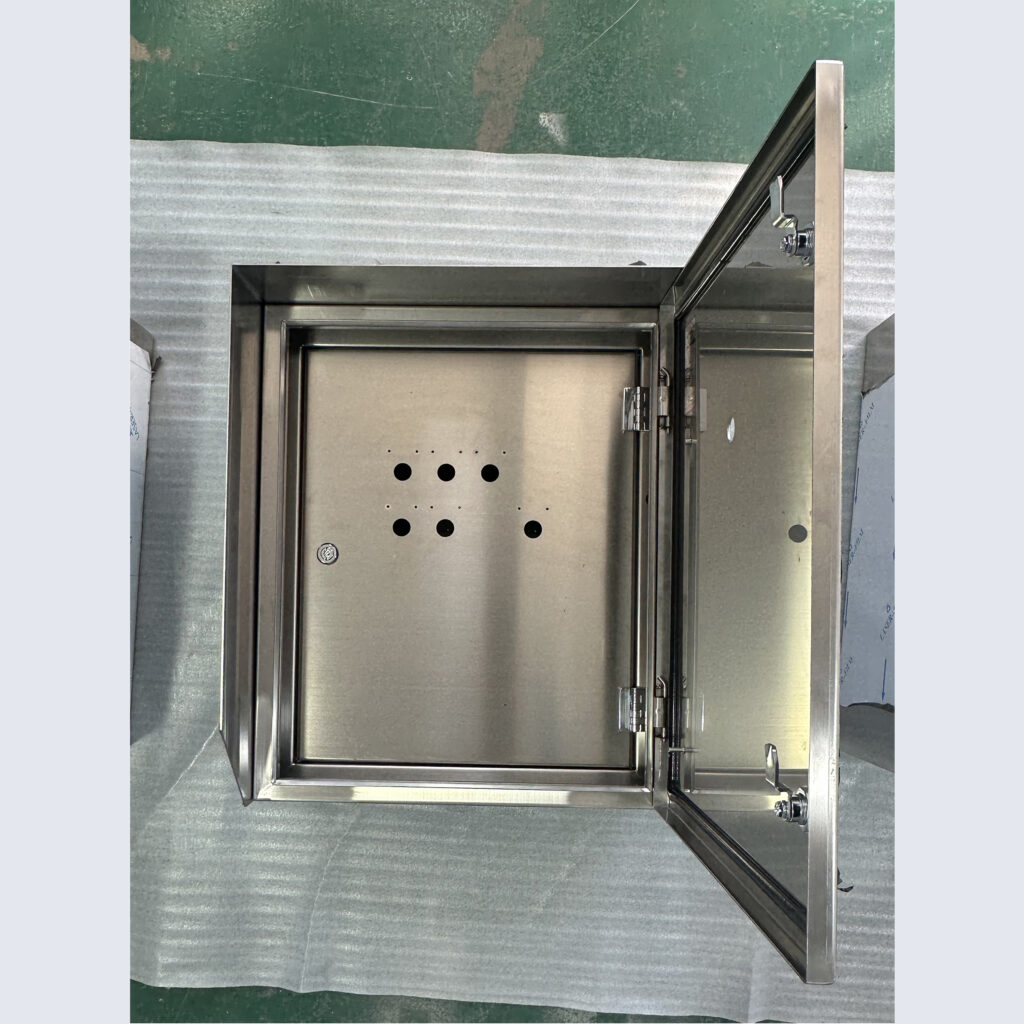
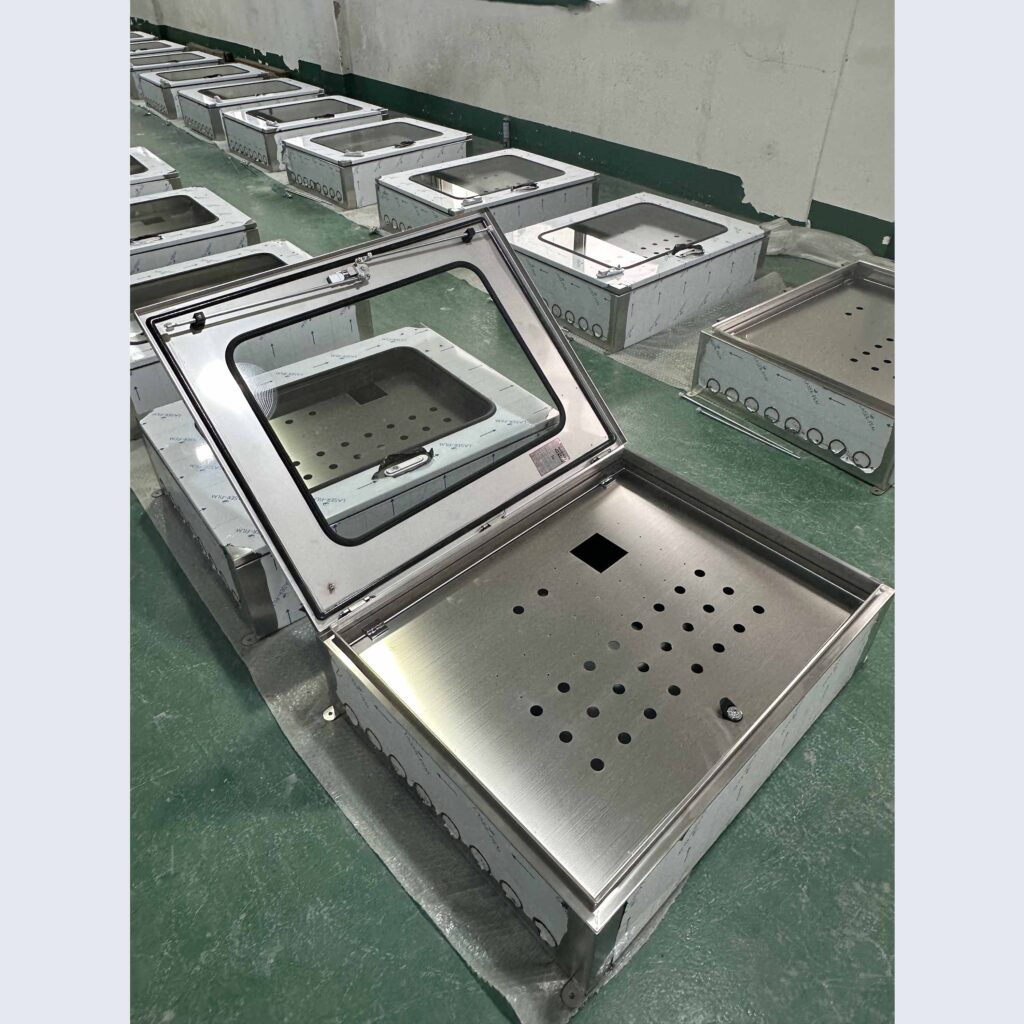
Sheet metal junction box
Weatherproof sheet metal enclosure
Wall mounted sheet metal enclosure
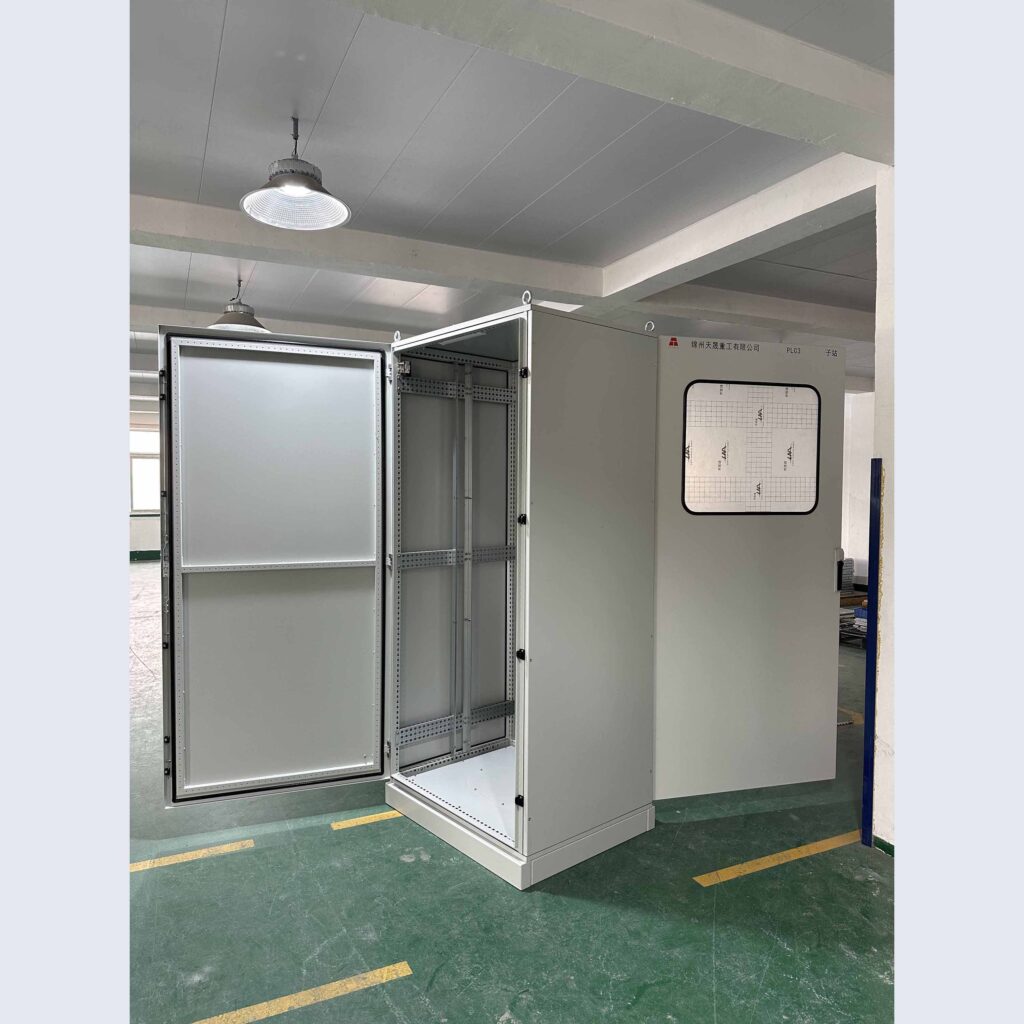
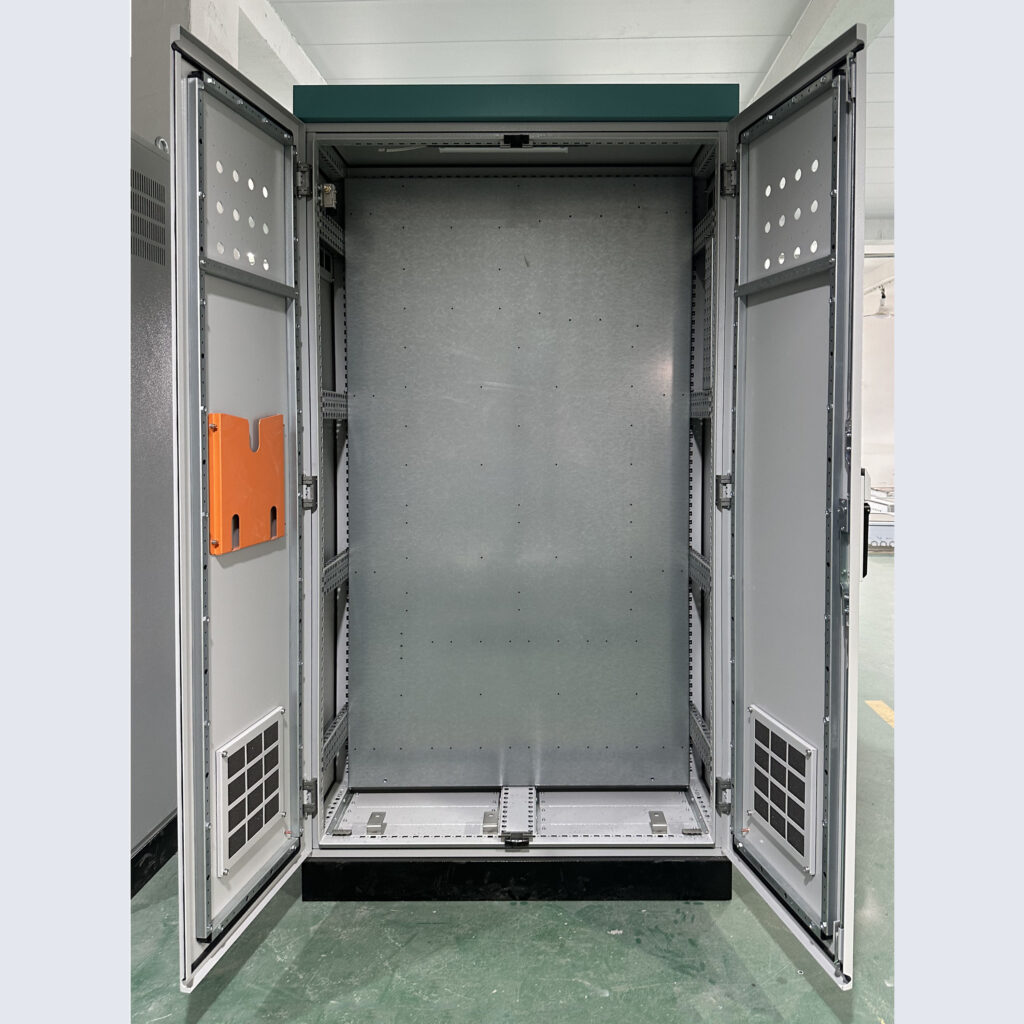
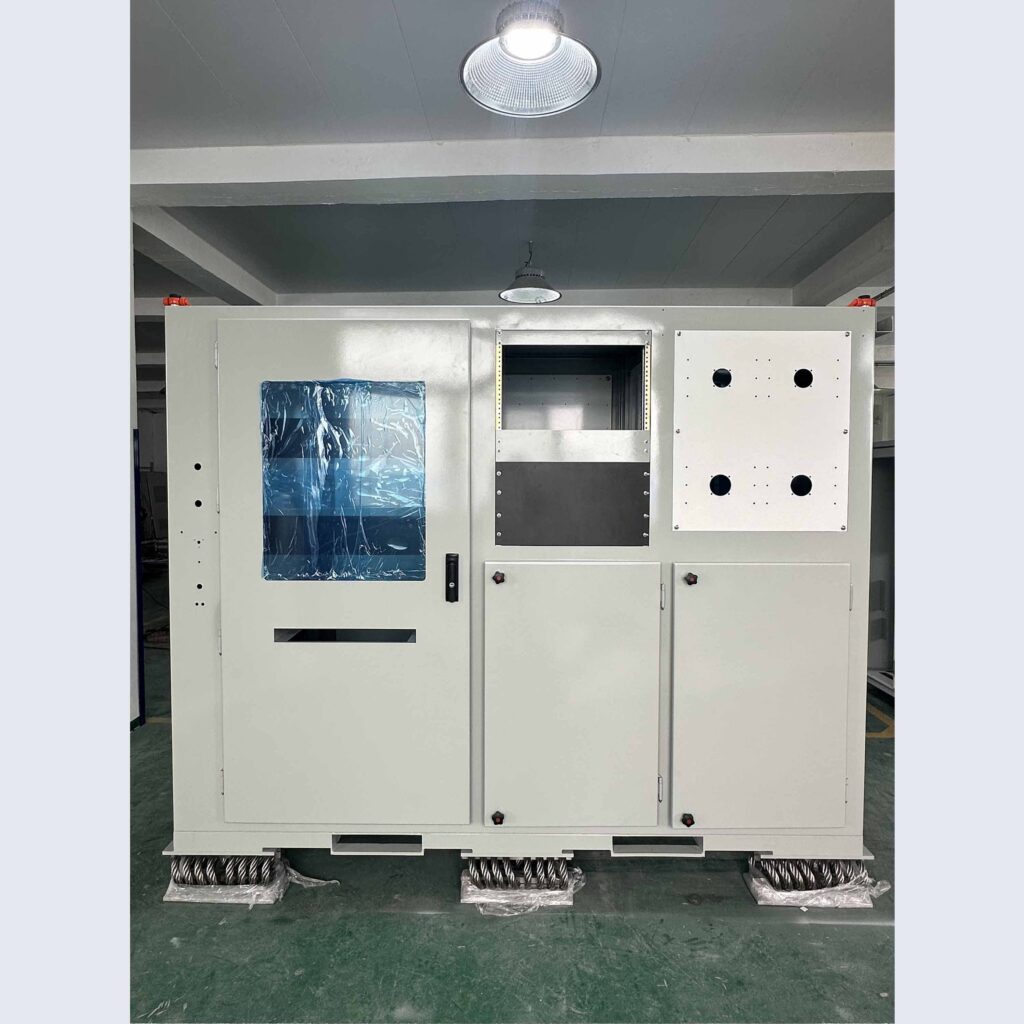
Floor standing sheet metal enclosure
Electrical sheet metal enclosure
Marine shock absorbing sheet metal enclosure
If the products listed don’t have what you want, that’s okay.
Yinlu has a professional R & D design team, regardless of the size of the product as long as you tell us your ideas, we will help your products into reality, choose Yinlu is definitely the most correct choice.
Sheet Metal Enclosure Fabrication Capacity
Table of Contents
Sheet Metal Enclosure Fabrication—Complete Guide
- Betty
The most crucial and important step before the production of sheet metal shells is to communicate with clients and finalize the design plan.
In this stage, the functions of the product will be clarified, and the materials and processing techniques to be used in the production process of the project will be determined.
During the prototype design stage of sheet metal enclosure, Yinlu will offer the best production methods and the most cost-effective solutions.
Step 2: Sheet metal enclosure cutting
There are numerous techniques for realizing sheet metal cutting.
Here, several of the most common and frequently used cutting methods will be introduced, including Shearing Machine Cutting, Plasma Cutting, Laser Cutting, and Water Cutting.
Shearing Machine Cutting:
Hydraulic pump in the hydraulic shearing machine, which is used to apply pressure. Under the action of the pressure, the slide block will be pushed to move up and down along with the blade.
In this way, it can provide stable and powerful shearing force, making it suitable for cutting relatively thick plates.
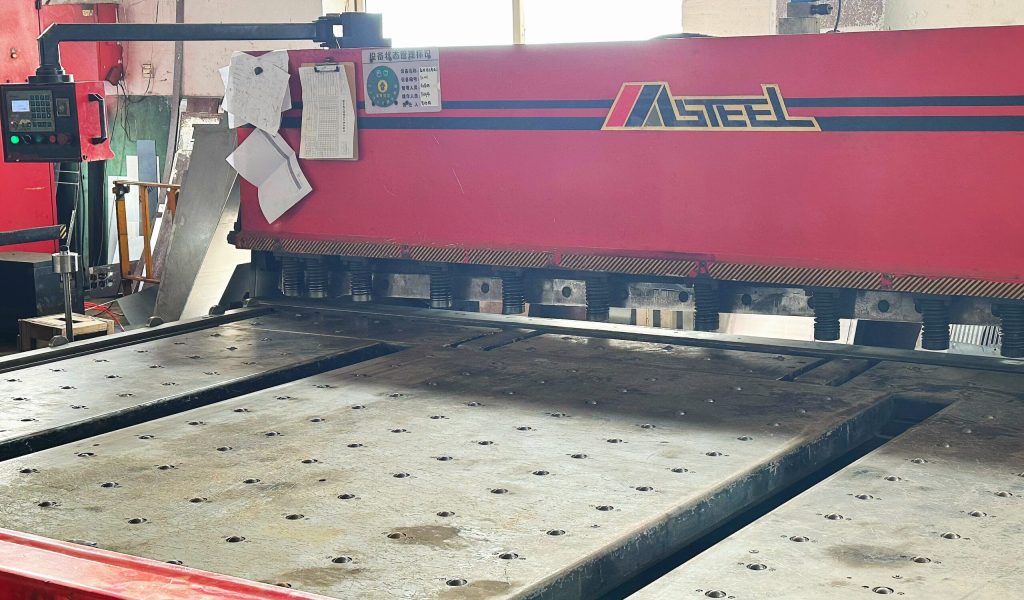
Figure No.1 Shearing machine cutting
Plasma Cutting
Plasma arc has the characteristics of high temperature, high energy density and high speed, which can quickly melt and vaporize metals. Plasma cutting technology precisely utilizes this feature to achieve the cutting of metal sheets.
When operating, it is necessary to set appropriate cutting current, voltage and gas flow parameters according to the material and thickness of the workpiece. During plasma cutting, generally, the width of the cutting seam can be controlled within 1 – 5 mm. The narrower the cutting seam is, the less material will be wasted, and it can effectively reduce the cost of sheet metal enclosure manufacturing.
Plasma cutting can cut almost all metal materials, such as carbon steel, stainless steel, aluminum, copper and so on. For different materials, just pay attention to the appropriate cutting parameters when cutting. Auxiliary gas can also be used to make the cutting surface smoother.
Although plasma cutting technology can achieve relatively good cutting quality, compared with laser cutting technology, the roughness of the plasma cutting surface is still relatively higher. In the manufacturing of some precision instrument shells, further grinding, polishing and other processing procedures are still required.
Laser cutting technology utilizes a laser beam with high energy density to irradiate metal sheets. The surface of the irradiated material will absorb the energy generated by the laser, and the temperature will rise sharply, thus melting and vaporizing instantly.
At this time, with the effect of auxiliary gases, the excess molten parts will be blown away, thereby achieving the cutting of metal sheets.
Common auxiliary gases include oxygen, nitrogen, argon and so on.
Oxygen can significantly increase the cutting speed through chemical reactions with metals, making the cutting process more efficient.
Nitrogen is an inert gas. During the cutting process, it can keep the original chemical properties of the cutting surface and also make the surface smoother.
The subsequent process of sheet metal enclosure processing will feature high surface smoothness and aesthetics.
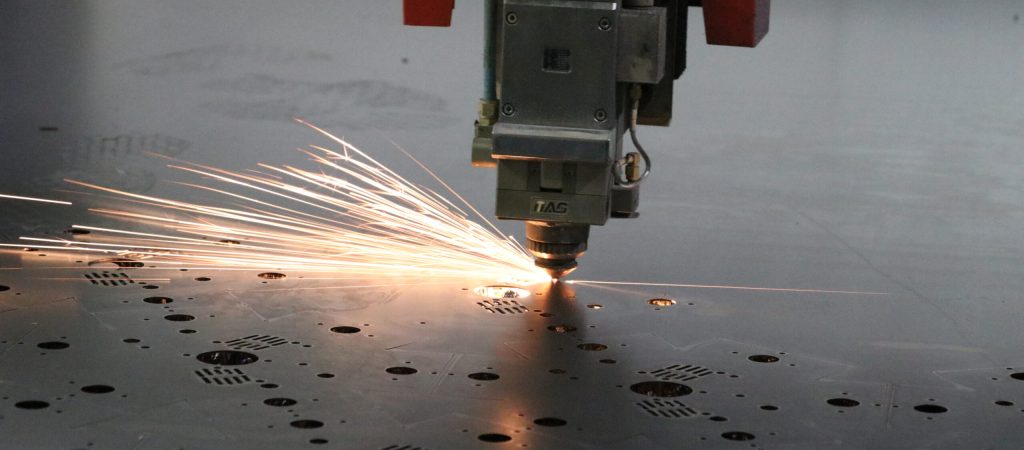
Figure No.2 Sheet metal enclosure laser cutting
Water Cutting
Water cutting is different from plasma cutting and laser cutting. It is a cold cutting technology.
The principle is that water is pressurized to an extremely high pressure state, so that it gains huge kinetic energy. Then, high-speed water flows are formed through tiny water outlet nozzles to carry out cutting.
Due to the cooling effect of water, the heat-affected zone of the material during the cutting process is very small, almost negligible. Therefore, there won’t be the problem that the performance of the material is reduced due to deformation caused by high temperature.
Step 3: Sheet metal enclosure bending
In the manufacturing of sheet metal enclosures, bending is an essential and crucial step. Through reasonable bending design, the structural strength of metal shells can be greatly enhanced.
Figure No.3 Sheet metal enclosure bending
V Bending
This is one of the most common bending methods.
Put the metal sheet between the V-shaped upper die and the lower die, and realize the bending effect by means of extrusion.
The structure of the V-shaped die is relatively simple and has strong universality. In the manufacturing of large mechanical sheet metal enclosure or electrical control cabinets, the edges formed by V-shaped bending can well protect the internal structures and enhance the overall structural strength.
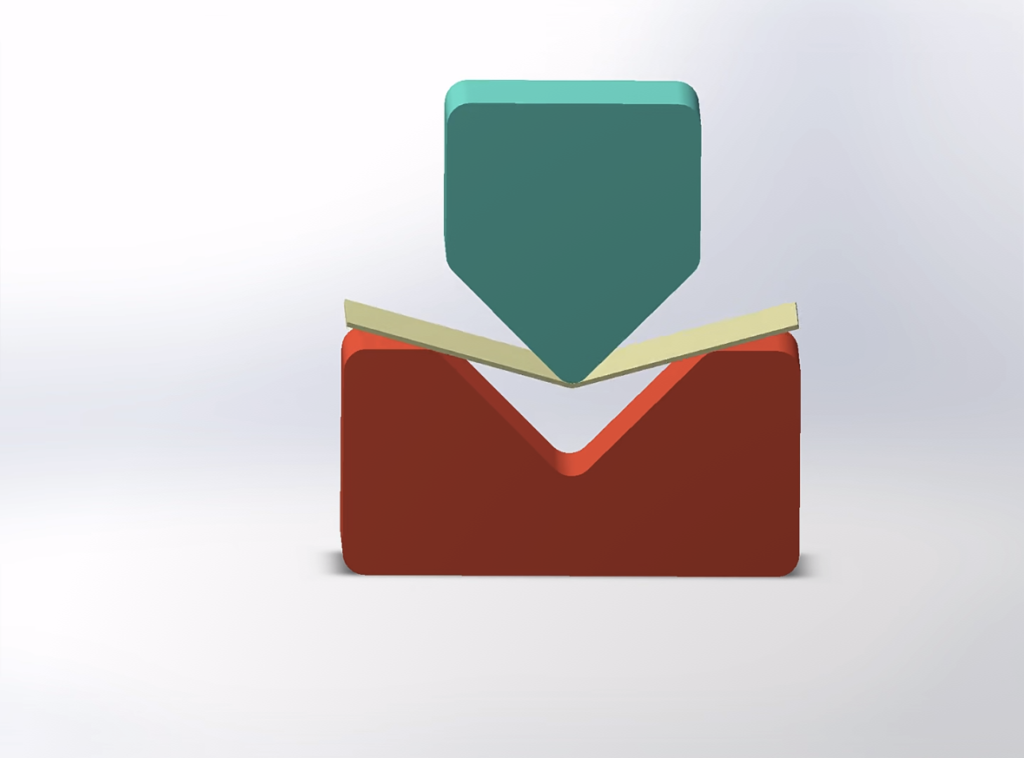
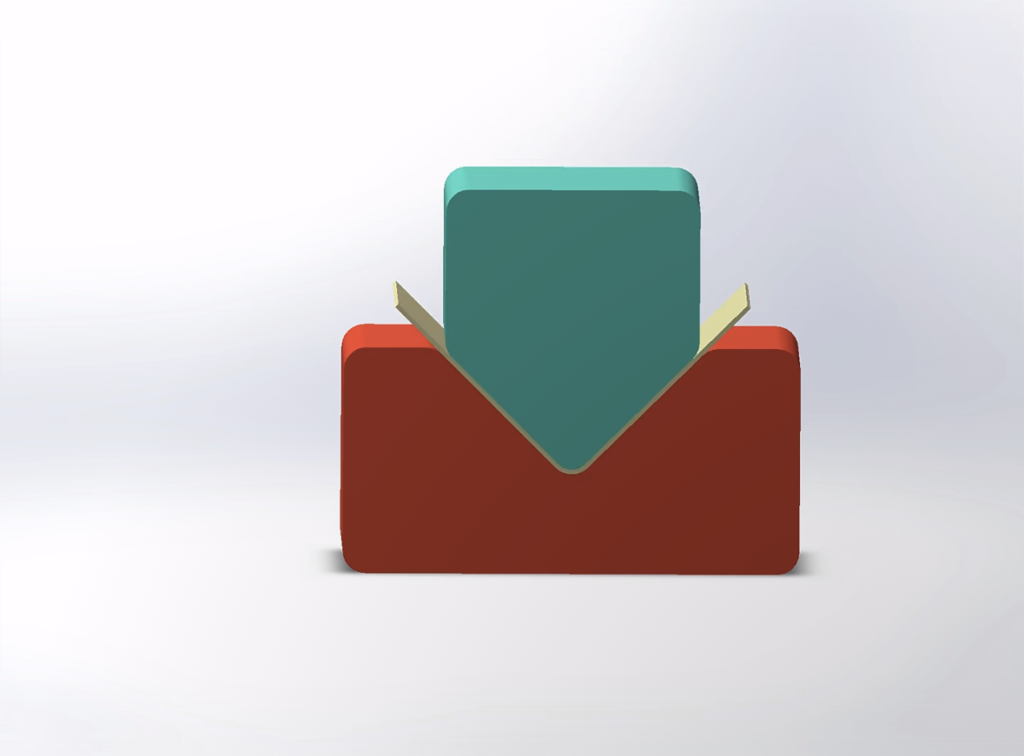
Figure No.4 V-Bend demonstration
Z Bending
Z-shaped bending is developed on the basis of the V-shaped bending. Special Z-shaped dies are required. During the operation, the metal sheet first undergoes the first bending through the first protrusion and groove, and then has the second reverse bending on the same die, thus forming a “Z” shape.
Z-shaped bending can create more installation planes and connection structures within a limited space, which helps to optimize the internal space layout of equipment. This is very important for those metal shells that require a certain amount of internal storage space.
U Bending
U-shaped bending also requires the use of specialized U-shaped dies. The upper die is generally a convex die in a U shape, and the lower die is the corresponding concave die in a U shape. During the operation, the metal sheet is placed between the upper and lower dies. The upper die presses down to make the sheet bend into a U shape around the shape of the dies.
The structure after U-shaped bending forms a semi-closed or approximately closed space and has a good accommodating function.
When manufacturing various container-type sheet metal enclosure products, such as distribution boxes, this U-shaped structure can well protect the internal structures from external interference and enable convenient installation and wiring of internal components.
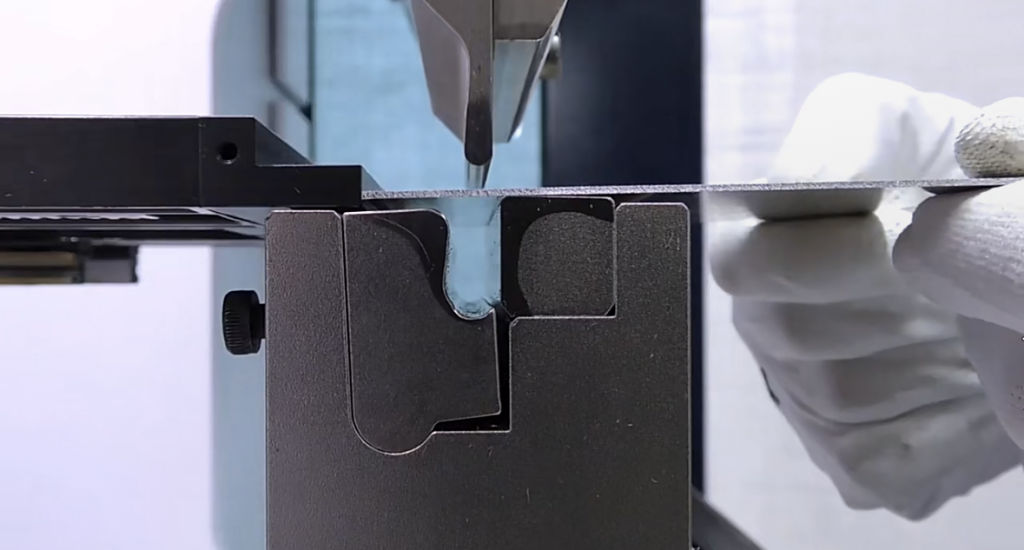
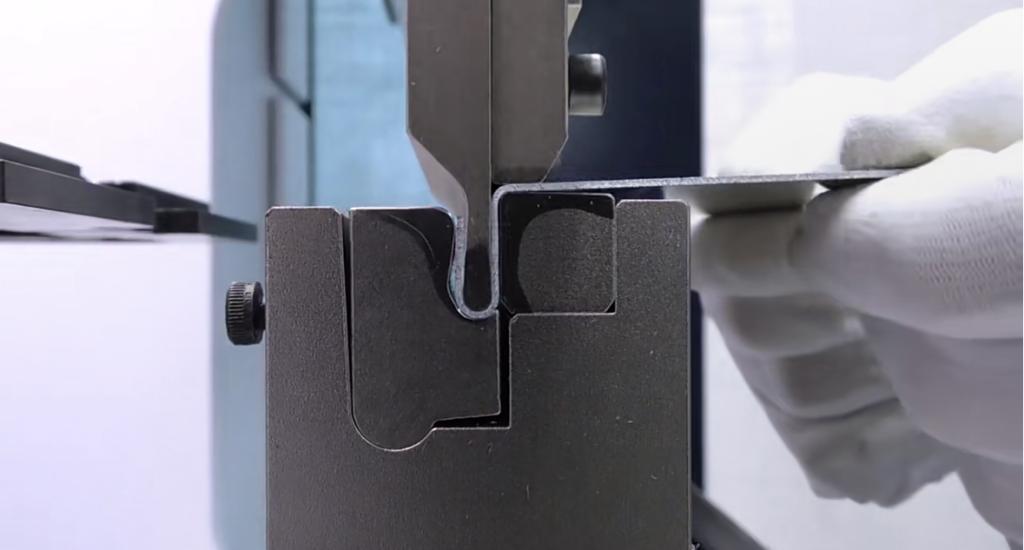
Figure No.5 U-Bend demonstration
Step 4: Sheet metal enclosure welding
There is a wide variety of choices for materials in the selection of sheet metal enclosure. Different materials can be selected for processing according to specific functions and usage environments, such as carbon steel, stainless steel and so on.
Since the processing materials are different, the welding methods will also vary.
The following are three of the most common welding methods.
Please continue reading.
Tig Welding
TIG welding is a method that uses a tungsten electrode and conducts welding under the protection of inert gases like argon. TIG welding can precisely control the welding heat input, making the weld seam smooth in appearance and of high quality. Moreover, thanks to the protection of argon, the weld seam also has good corrosion resistance.
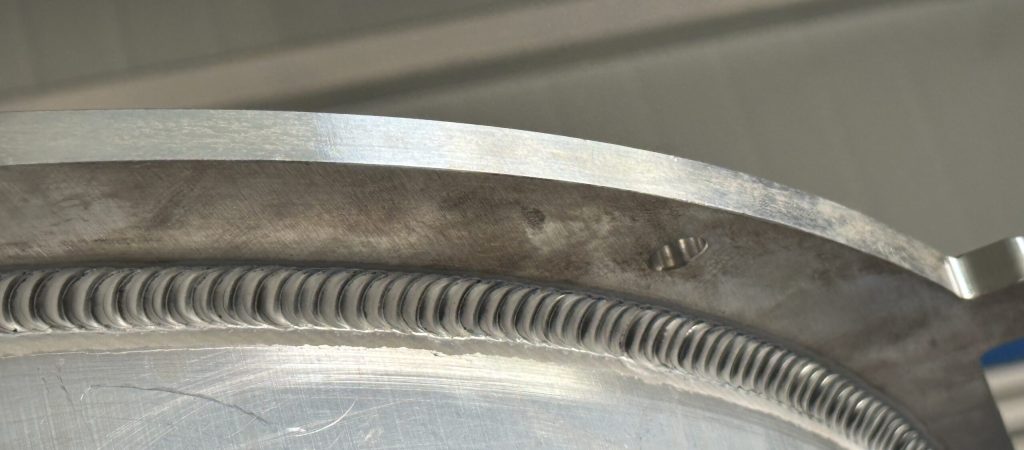
Figure No.6 Welding effect display
Mig Welding
The electrode of MIG welding is a consumable welding wire. Different from TIG welding, the filler metal in MIG welding is continuously supplied through an automatic wire feeding method. It has a relatively high welding speed and greatly improves work efficiency.
Laser Welding
Laser welding utilizes a laser beam with high energy density as the heat source for welding. Laser welding can minimize thermal deformation to the greatest extent and achieve high-precision welding.
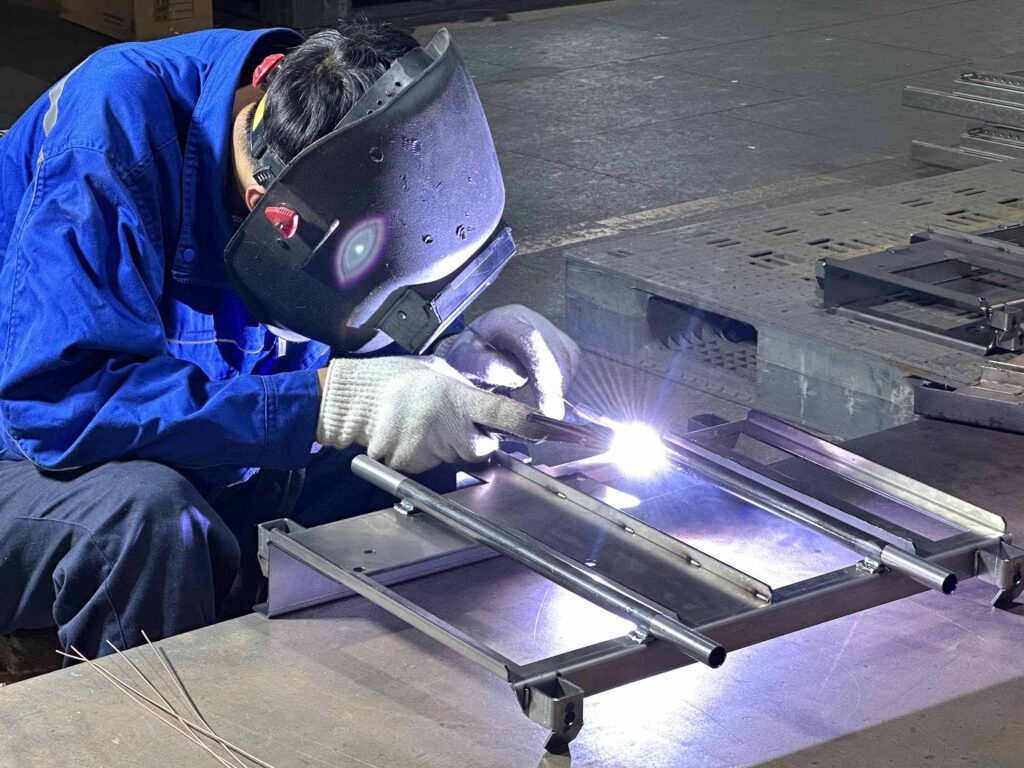
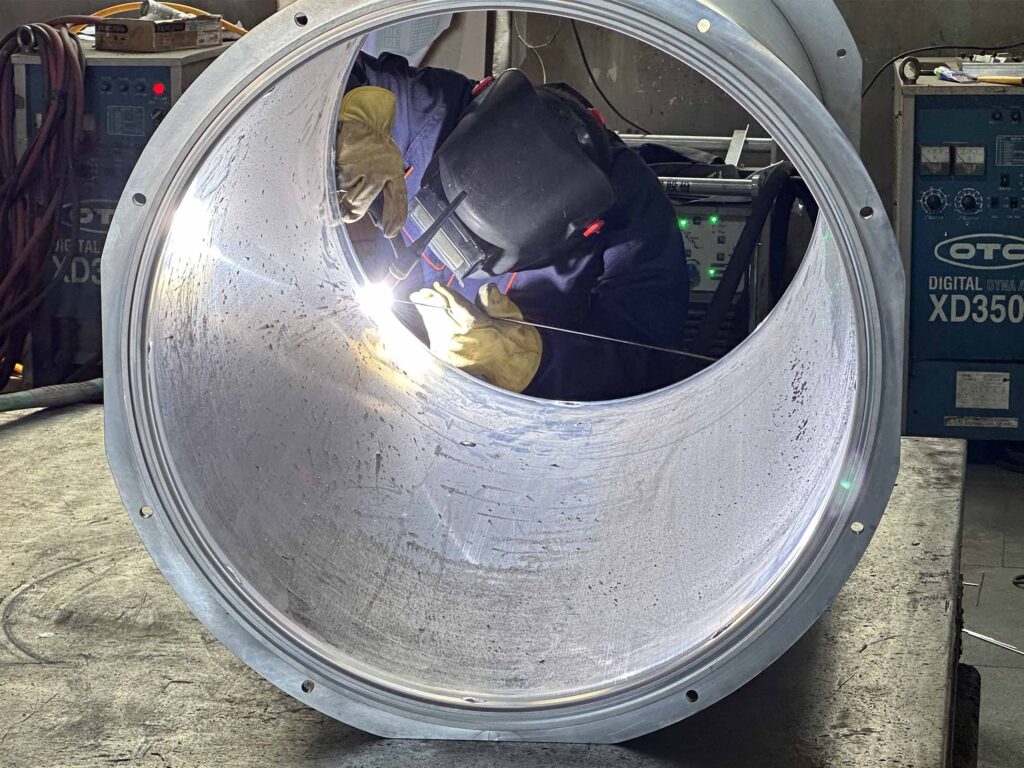
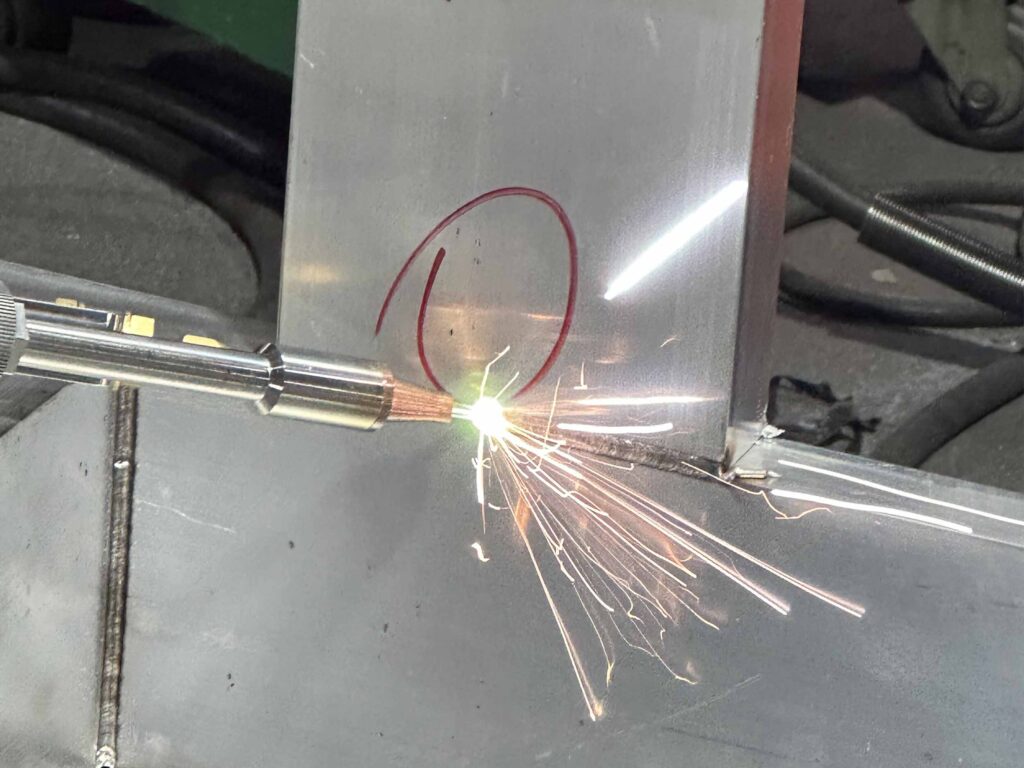
Figure No.7 Sheet metal enlosure welding diplay
Surface treatment is a crucial step in the later stage of the processing process, and it plays a decisive role in the appearance, function and protection of the product.
Only when the sheet metal enclosure have undergone good surface treatment can they be assembled more easily with other components, and problems such as rough surfaces and burrs can be minimized to the greatest extent.
The following are some surface treatment processes. Yinlu has a powerful surface treatment capability. Please feel free to contact us if you have any questions.
Spray Painting
Spray painting can not only achieve a wide variety of colors but also bring good glossiness.
It can effectively cover some slight scratches on the surface of sheet metal enclosure.
In terms of protective performance, it can effectively prevent metal enclosure from rusting and corroding.
For sheet metal enclosures produced on a large scale, spray painting can effectively control costs while ensuring quality.
Compared with spray painting, powder coating is more environmentally friendly, and the utilization rate of the coating can usually reach more than 95%.
Under the action of electrostatic adsorption, it can efficiently adhere to the surface of workpieces and has relatively high hardness and wear resistance.
The powder coating can provide good anti-corrosion protection for sheet metal enclosures and effectively extend their service life.
Electroplating
Electroplating can provide sheet metal shells with a shiny, smooth and metallic-looking appearance. It improves the hardness and wear resistance of the surface and meets the requirements of those sheet metal enclosure that need good electrical conductivity.
Anodizing
Anodizing is mainly used for aluminum and aluminum alloy sheet metal enclosure.
The oxide film generated by anodizing has relatively high hardness, so it significantly improves the wear resistance of the surface and provides a good adhesion basis for subsequent surface treatment processes such as painting and printing.
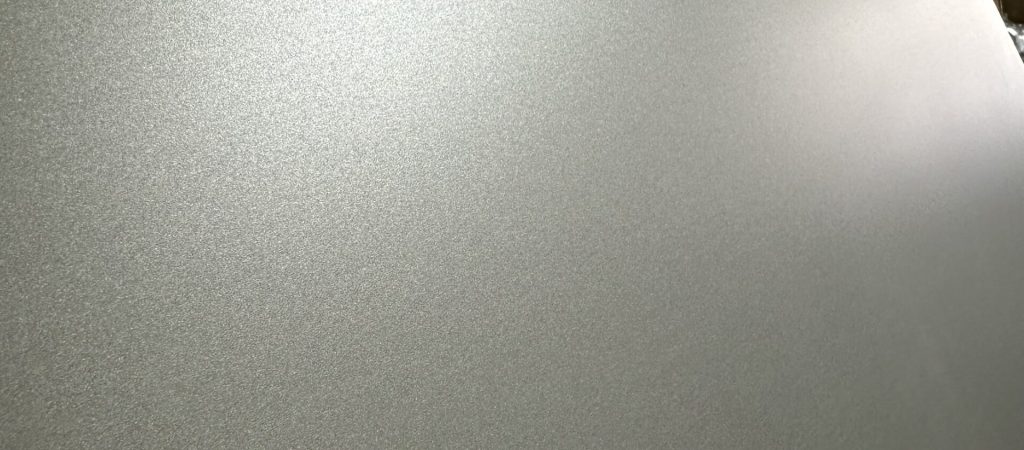
Figure No.8 Aluminum Alloy hard anodized
Screen Printing
Screen printing can print designed patterns, texts, logos and other information onto the surface of sheet metal shells. It is applicable to various materials and shapes.
Polishing
Polishing removes the tiny scratches on the surface of the shell and can make the surface as shiny and smooth as a mirror.
Figure No.9 Polishing Video
Phosphating
The phosphating film itself has a certain protective effect on metals and can prevent rusting and corrosion to a certain extent. This film is porous and has a rough surface, providing good adhesion for subsequent painting.
In this article A Comprehensive Guide to Surface Treatment Methods,we introduce a more complete and comprehensive surface treatment process, you can click to read or contact us.
- In terms of dimensional accuracy: We use measuring tools (such as calipers and micrometers) to measure all aspects of the shells.
- In terms of surface quality: Yinlu has professional coating thickness gauges and surface roughness testers and other tools to ensure the surface quality of sheet metal shells.
- In terms of material properties: We adopt methods like tensile tests and hardness tests to ensure that the material strength meets the design requirements.
- In terms of protection level: We evaluate the dustproof and waterproof capabilities of sheet metal shells through the IP protection level.
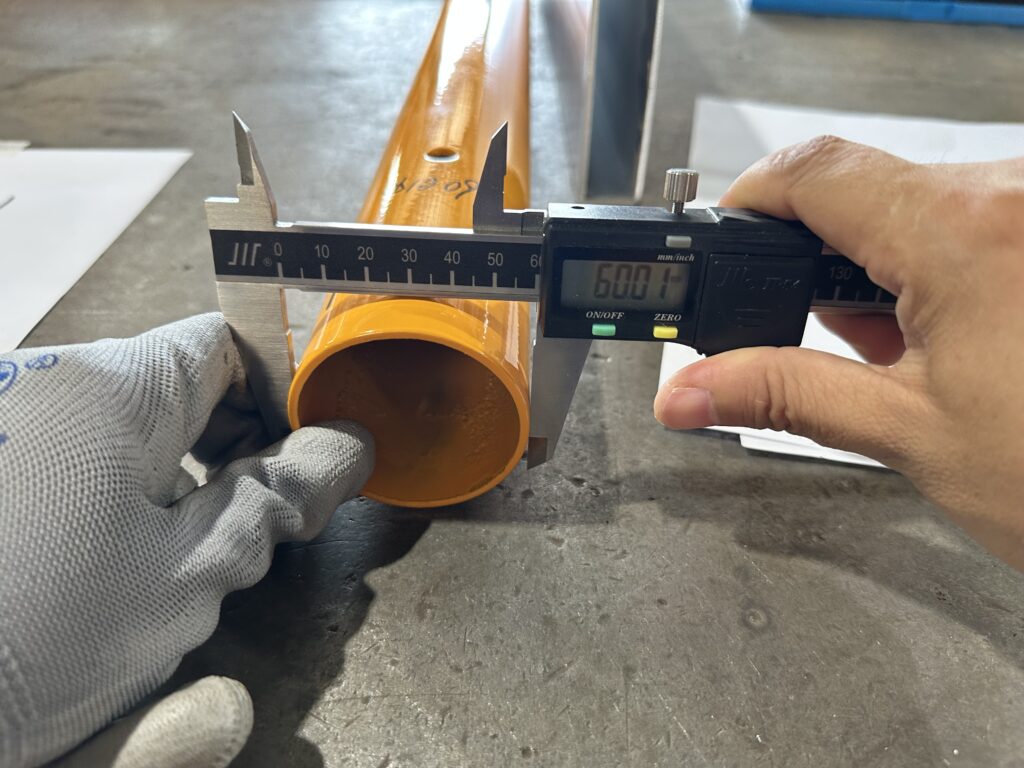
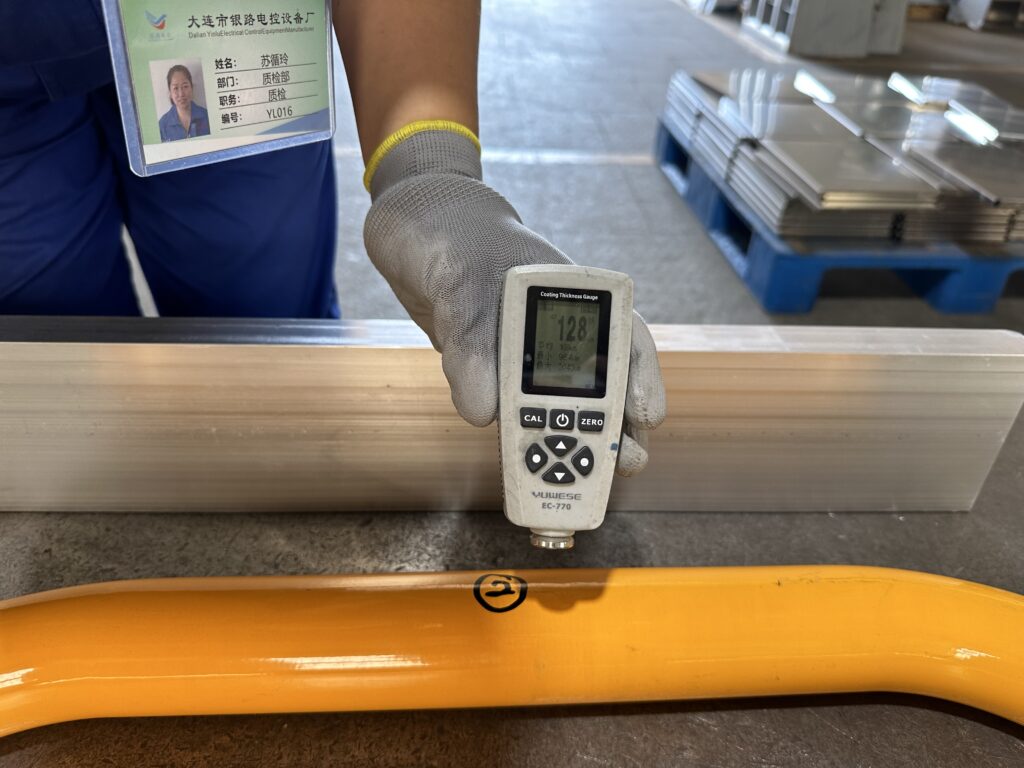
Figure No.10 Product Quality Inspection
Conclosion
Yinlu is definitely the most trustworthy manufacturer of sheet metal enclosure for you.
If you have any purchasing needs recently, please feel free to contact us.