Table of Contents
Sheet Metal Surface Treatment: A Simple Guide
- Betty
In modern manufacturing, sheet metal products can be seen everywhere. From the casings of industrial equipment to household appliances in daily life, sheet metal plays an important role.
The process of sheet metal surface treatment, which seemingly only modifies its appearance, actually has crucial significance and is closely related to the performance and quality of products in multiple aspects.
Why do metal surface treatment
Most sheet metal products are made of metal materials, such as steel plates, aluminum plates, and stainless steel. They are highly susceptible to corrosion due to oxygen, moisture and uncontrollable factors in the environment. As time passes, they will gradually rust, which leads to a decline in product performance and a weakening of the structure.
For example, the sheet metal casing of a distribution box used outdoors will not only affect its appearance but also cause some potential safety hazards if the raw materials are not properly metal surface treatment
- Improve corrosion resistance
- Enhanced wear resistance
- Improve appearance
- Add special features
Common metal surface treatment methods
Common metal surface treatment methods are roughly divided into three categories:
mechanical treatment、chemical treatment、electrochemical treatment
Mechanical Treatment
Grinding
Using abrasives (such as sandpaper, grinding wheels, abrasive belts, etc.), relative motion is carried out against the metal surface under a certain amount of pressure applied, and the grinding effect on the metal surface is achieved through the particles.
Grinding is the first step in metal surface treatment. After laser cutting, some burrs will remain on the sheet metal. These burrs are very dangerous as people may get stabbed by accident. Therefore, the main function of grinding is to remove burrs, oxide scales and old coatings on the surface of the sheet metal,etc.
Polishing
It usually continues to be processed on the basis of grinding. At this stage, the metal surface presents a mirror-like effect by the mutual cooperation between the polishing wheel and the polishing paste.
Sandblasting
Sandblasting requires professional sandblasting equipment to spray abrasives with a certain particle size onto the surface of the metal through a spray gun.
After these abrasives with a certain particle size impact the metal surface with strong force, they can remove the oxide layer, rust and other impurities on the surface. Therefore, the surface after sandblasting has a certain degree of roughness.
The surface roughness after sandblasting is beneficial for subsequent coatings, plating layers and so on to adhere to the metal better and helps improve the bonding strength.
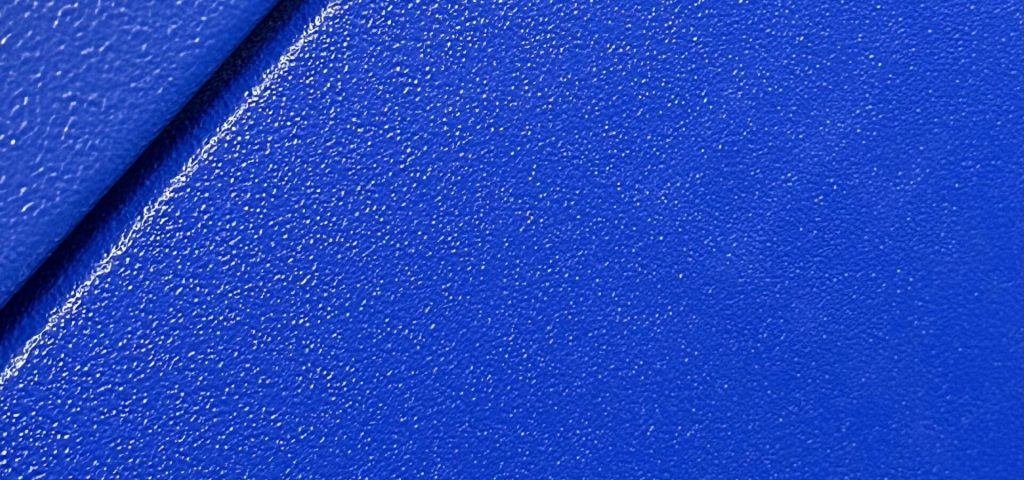
Figure No.2 Sandblasting
Chemical Treatment
Pickling
Immerse the metal workpieces that need to be treated in acidic solutions. These acidic solutions should be prepared according to different metal materials and treatment purposes. It should be noted that these acid solutions are highly corrosive, so make sure to take good protective measures during the operation process.
Alkaline cleaning
Contrary to pickling, alkaline cleaning uses alkaline solutions to clean oil stains, grease and dust on the metal surface. Alkaline solutions are also corrosive, so it’s necessary to take good protective measures and reasonably control the concentration, temperature and cleaning time of the alkaline solutions.
Phosphating
The main component of the phosphating solution is phosphate. Through the chemical reaction between the metal and phosphate, the adhesion of paint, coatings, powder coatings and so on to the metal surface can be significantly enhanced.
Electrochemical Treatment
Electroplating
Electroplating is a surface treatment technology based on electrochemical principles. The metal parts to be plated is taken as the cathode, and the metal material to be plated onto it is regarded as the anode. They are placed together in an electrolyte containing metal ions of the plating metal. After the direct current is switched on, a layer of metal plating is formed under the action of the electric field.
Anodizing
Put the metal parts as the anode into the electrolyte. When direct current is connected, an oxide film will accumulate and form on the metal surface. This method is mainly applied to non-ferrous metals such as aluminum and magnesium.
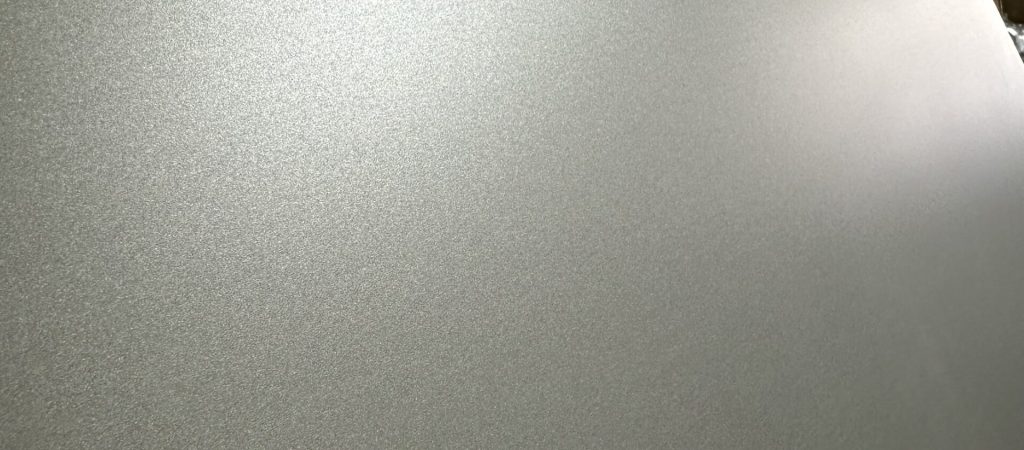
Figure No.3 Aluminum Alloy hard anodized effect
New metal surface treatment technology
Thermal spraying
Thermal spraying is a process method in which heat sources are used to heat spraying materials and then spray them onto the metal surface to form coatings.
Vapor deposition
It can be divided into two types according to its application methods:
Physical vapor deposition (PVD):
In a vacuum environment, these are converted into gaseous state through physical means like evaporation. Under the action of an electric field, the gas particles move to the surface of the metal and deposit there, gradually forming a thin film.
Chemical vapor deposition (CVD):
Some gaseous compounds with specific chemical structures undergo chemical reactions in a high-temperature environment and then deposit on the metal surface to form a thin film.
Conclusion
Metal surface treatment encompasses numerous processing methods.
Different treatment approaches are applicable to different metal materials, application scenarios and the purposes intended to be achieved.
At Yinlu, we offer you the most advantageous metal surface treatment services. Please feel free to contact us at any time.