Custom sheet metal outdoor generator enclosure
In today’s diversified market environment, customers often need to think carefully when choosing the materials for product enclosures. We are glad to see that many customers have wisely chosen metal materials for their outdoor generator enclosure, and there are careful considerations and numerous advantages behind this decision. Especially, the sheet metal outdoor generator enclosure has demonstrated its great strength in practical applications.
Author: Betty Release Time: 2024-11-4
Background
Our client is a sizeable local water treatment company.By chance, Simon, the purchasing manager of their company, visited our official website.
After learning that we are a professional manufacturer focusing on research and development of sheet metal processing, he immediately became very interested.
Later, Simon took the initiative to contact us and had an initial communication. During the conversation, we introduced in detail our company’s strength, past successful cases and unique technical advantages in the field of sheet metal processing.
Through this communication, Simon got a deeper understanding of us and was impressed by our professional spirit and exquisite craftsmanship. He showed a very strong willingness and hoped that we could help him complete this crucial product.
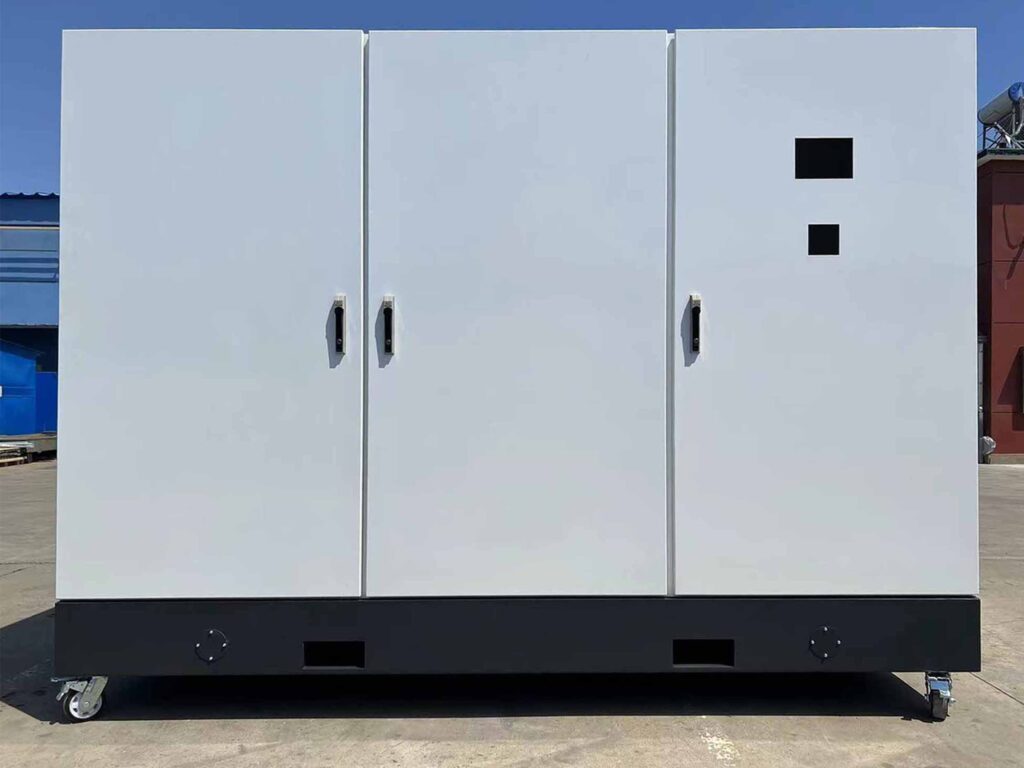
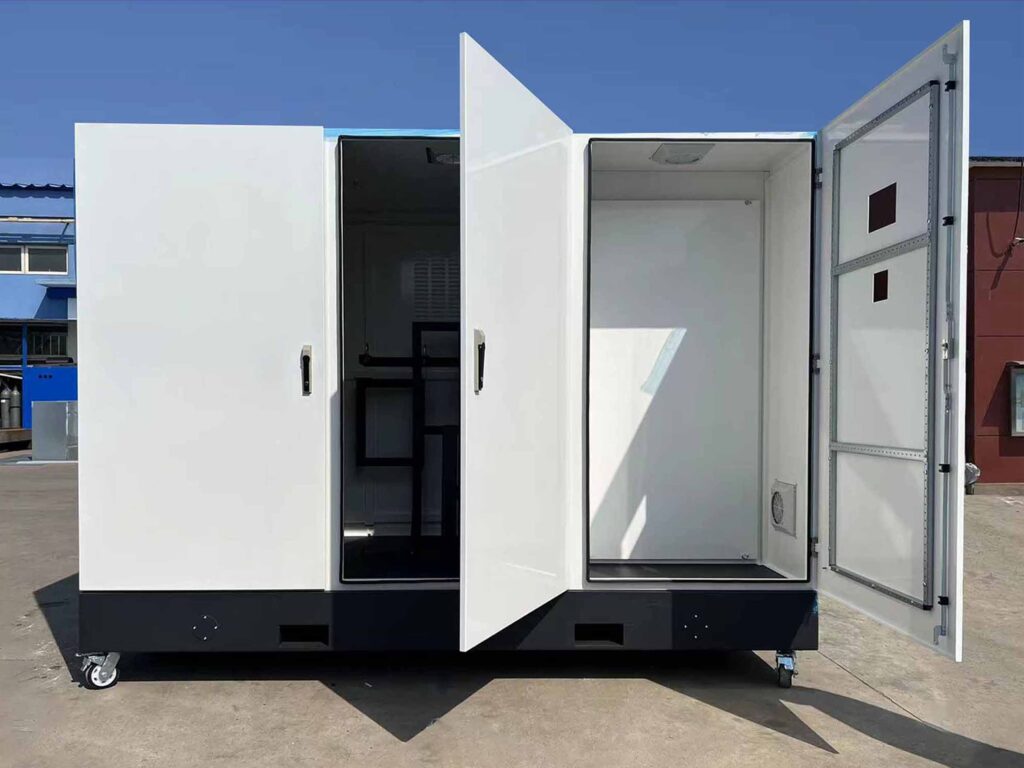
Figure NO.1 Product display
Challenge
·Water treatment equipment usually works in a relatively harsh environment, so it has extremely high requirements for the protective performance of sheet metal enclosures. This puts strict requirements on material selection and surface treatment processes.
·The dimensional accuracy of the case is also a challenge. Water treatment equipment often needs to fit closely with other components, and any size deviation can lead to difficult installation or even unusable. Our engineers had to repeatedly measure and adjust the design to make sure that every size was accurate.
Customization process
Outdoor generator enclosure design stage
·After in-depth communication with Simon, we learned about their size requirements and functional needs for the sheet metal enclosure. According to the collected demand information, our team began to formulate an initial design plan.
·Using professional design software SolidWorks we drew the initial two-dimensional sketch of the enclosure to determine the approximate shape, size and structural layout.
·After the initial design plan was approved by the customer, we started to build a three-dimensional model. so that the customer can see the final effect of the enclosure more intuitively.
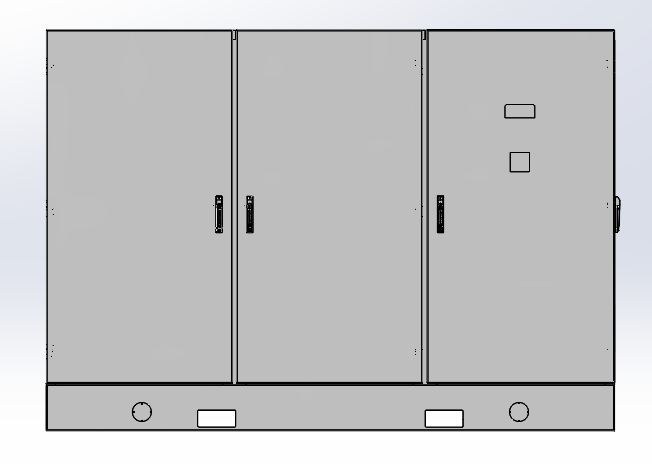
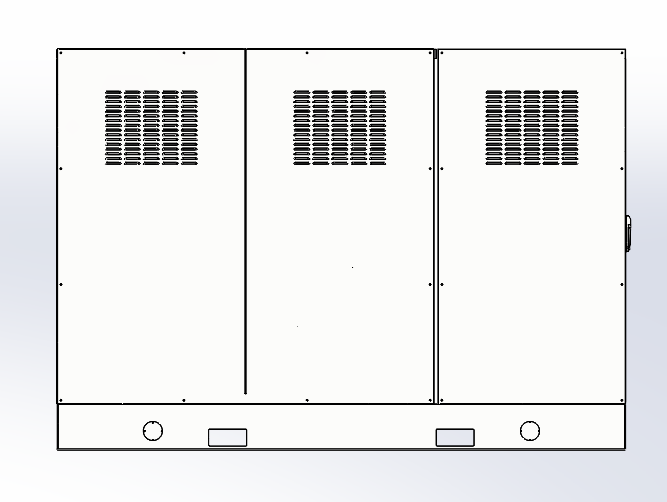
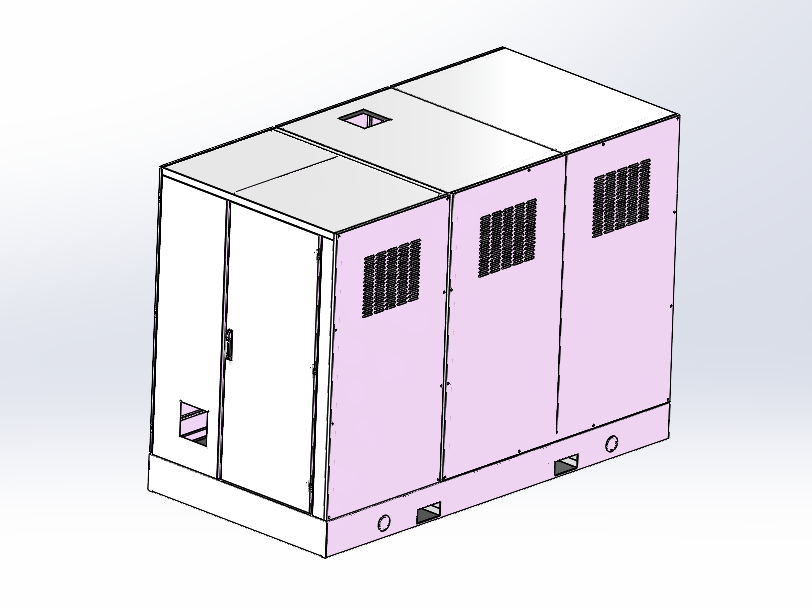
Figure NO.2 3D effect display
Outdoor generator enclosure material selection
·In the design of this outdoor generator enclosure, we divide the whole enclosure into two parts.
For the base part, we choose cold-rolled steel with a thickness of 5mm. The reason for choosing 5mm thick cold-rolled steel as the base is that the base needs to bear the weight of the whole enclosure and the internal equipment.
Thicker cold-rolled steel can provide stronger support and stability to ensure that the outdoor generator enclosure will not deform or shake in various usage environments.
·For the main body part, we use cold-rolled steel with a thickness of 2mm. The main reason for choosing 2mm thick cold-rolled steel as the material for the main body part is that while the main body part needs to meet certain strength requirements.
it also needs to be more lightweight and flexible for easy installation and handling. Thinner cold-rolled steel can reduce the weight of the whole enclosure and lower transportation costs.
At the same time, it can better realize the shape design and functional requirements of the outdoor generator enclosure under the premise of ensuring structural strength.
·For different situations, how to choose product materials can be found in the Sheet Metal Fabrication Materials Selection Guide article here to learn more about the relevant information
·First of all, we use high-precision laser cutting technology in material cutting. We ensure dimensional accuracy and edge smoothness. Then we bend the cut cold-rolled steel sheet according to the design requirements to form the various faces and structures of the shell.
·The welding process is also a key link in the manufacturing process. We use argon arc welding and carbon dioxide welding. During the welding process, we strictly control the welding parameters to ensure the quality and strength of the weld.
·At the same time, after welding, we polish and treat the weld to make the shell surface more smooth and beautiful.
·The surface treatment process is essential for the protective performance and appearance quality of the housing. We make the overall color RAL7035 and galvanize to enhance the rust resistance of the housing.
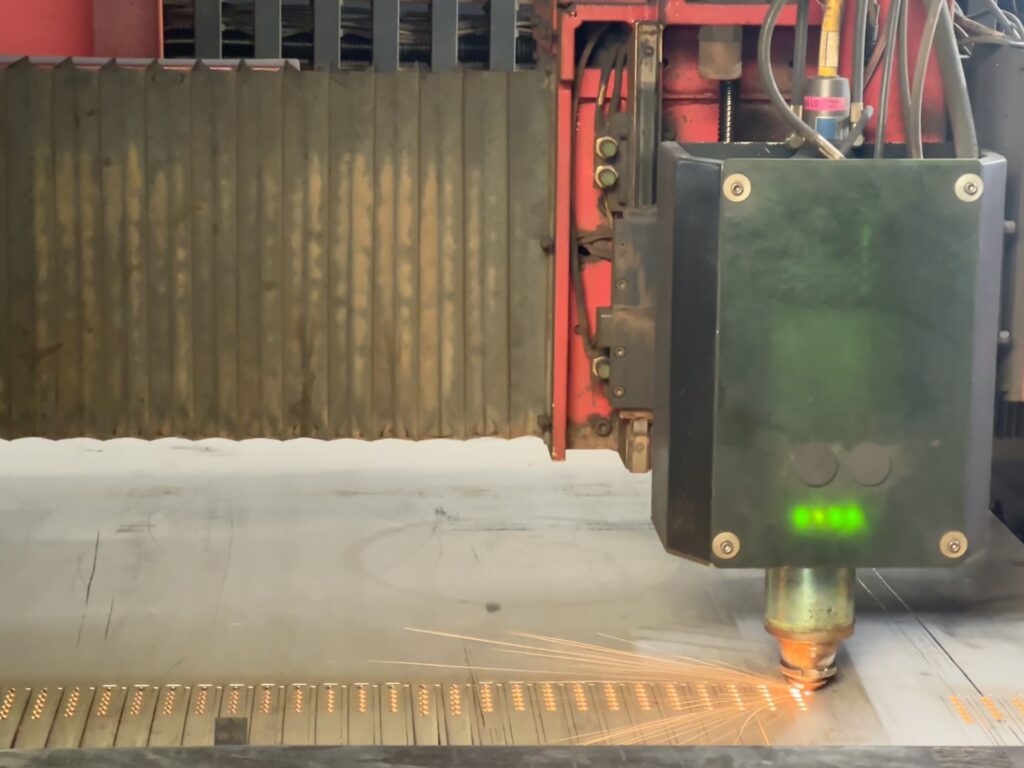
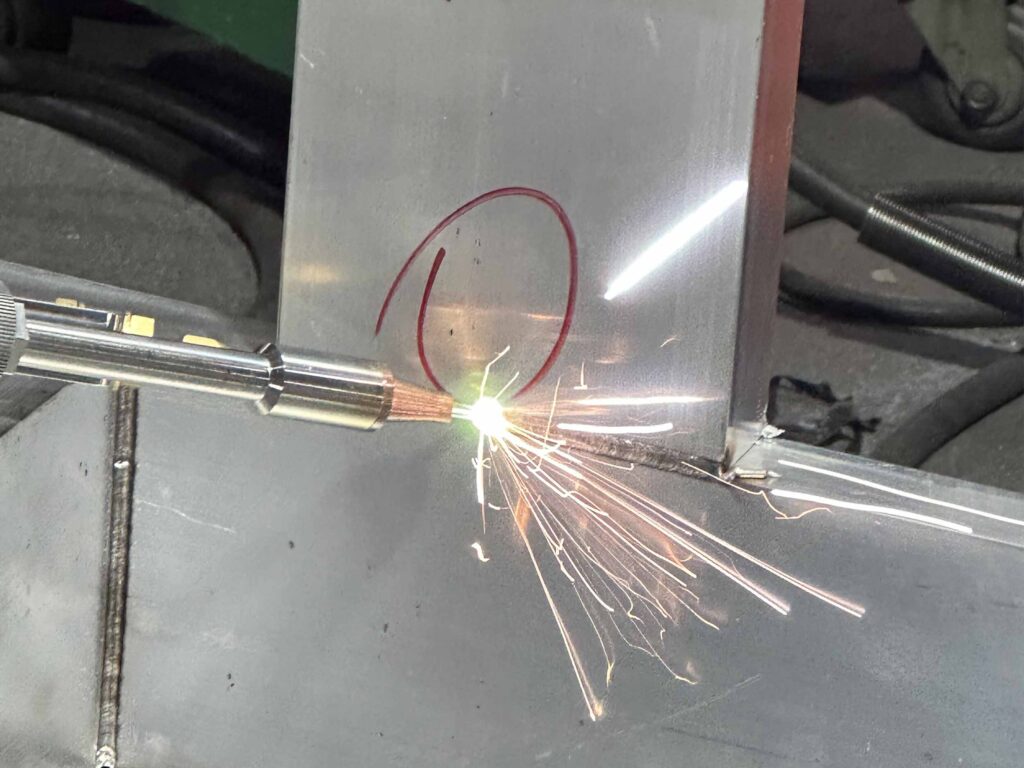
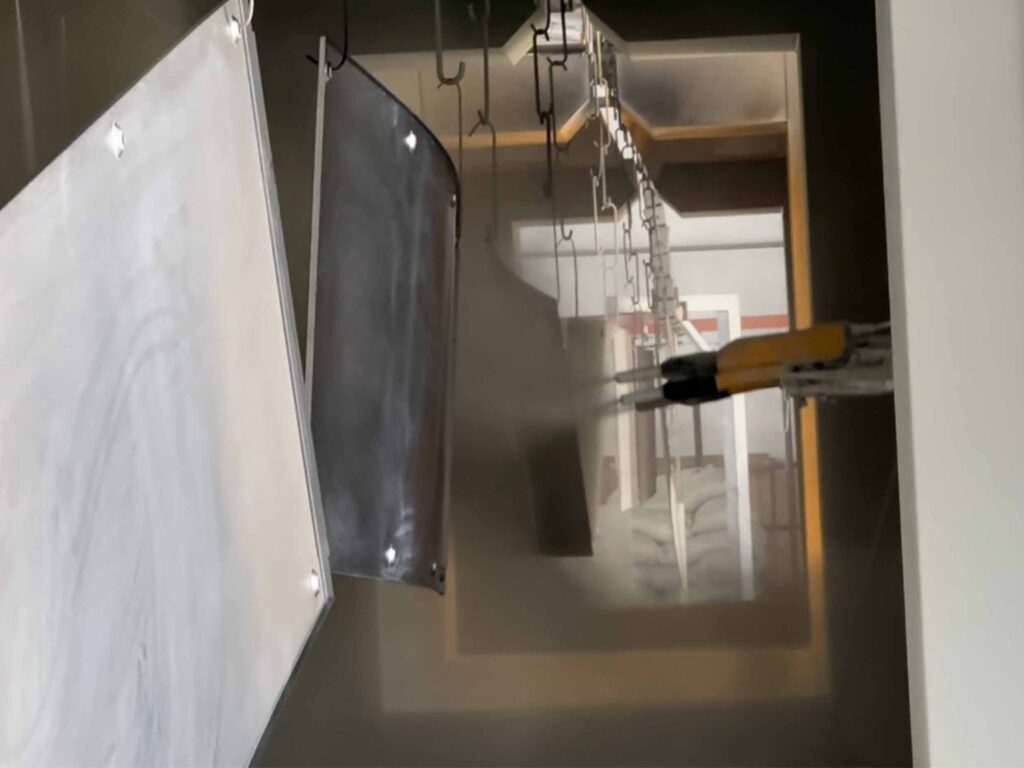
Figure NO.3 Cutting、Welding、Coating Display
Conclusion
Simon was very happy after receiving the product. We have reached a cooperation on this product. In any case, using sheet metal enclosures as the outer casings for various large outdoor equipment is a very correct choice.
With the continuous progress of technology, sheet metal enclosures have broad development prospects in the future.
On the one hand, material innovation will continue to advance. New sheet metal materials with high strength, light weight and good corrosion resistance will continue to emerge, providing more reliable protection for large outdoor equipment.
On the other hand, intelligent design will gradually be integrated into sheet metal enclosures. For example, integrating sensors to monitor equipment status and environmental changes in real time can improve the operating efficiency and safety of equipment.
Looking ahead, this approach will definitely achieve greater success and continuous progress. Sheet metal enclosures will play an increasingly important role in the field of large outdoor equipment and provide a solid guarantee for the development of various industries.
If you want to learn more about sheet metal enclosure fabrication services, you can visit our website 【yinlu-sheetmetal.com】for more details.