Table of Contents

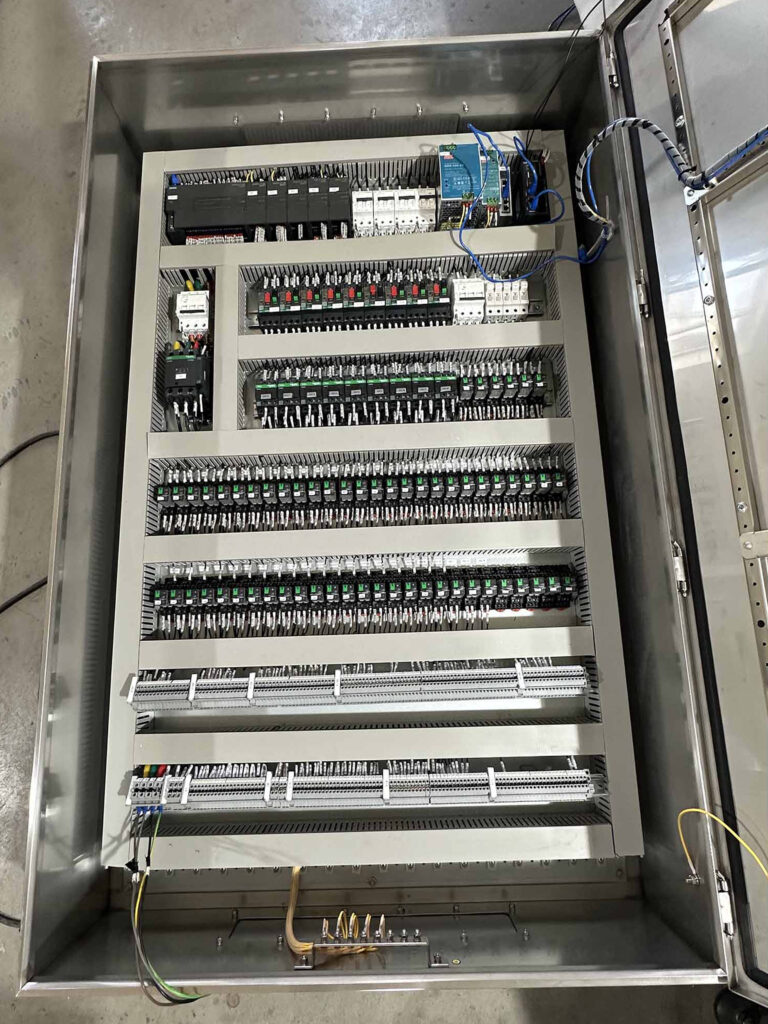
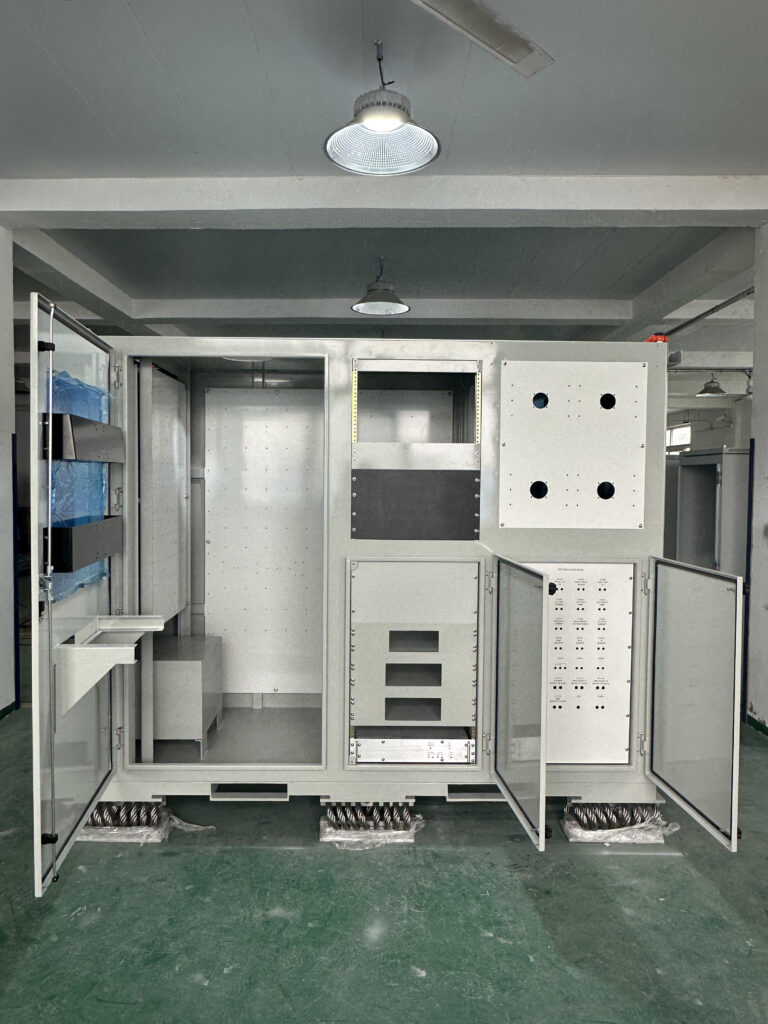
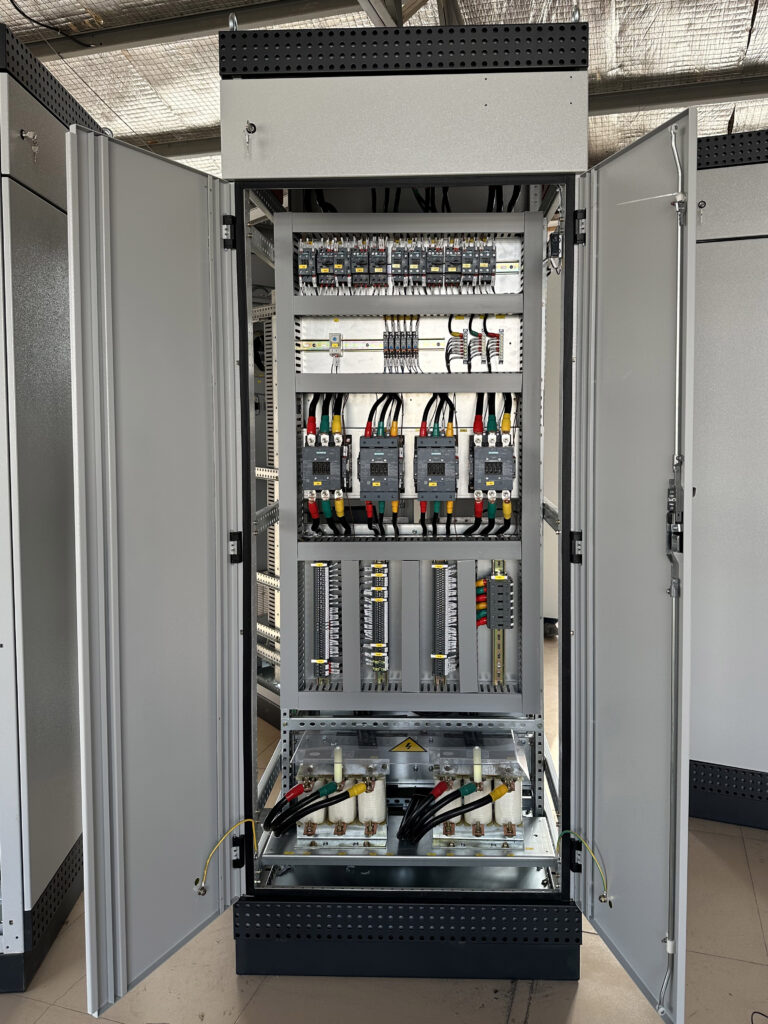
Sheet Metal Fabrication Cost Control Guide
- Betty
Sheet metal fabrication cost control requires addressing multiple aspects including design, processes, raw materials, production management, and suppliers. By optimizing each processes,we can achieve effective cost control.
This article focuses on sheet metal cost control methods to introduce Yinlu’s sheet metal fabrication cost control strategies, showcasing how we achieve cost reduction while maintaining product quality.
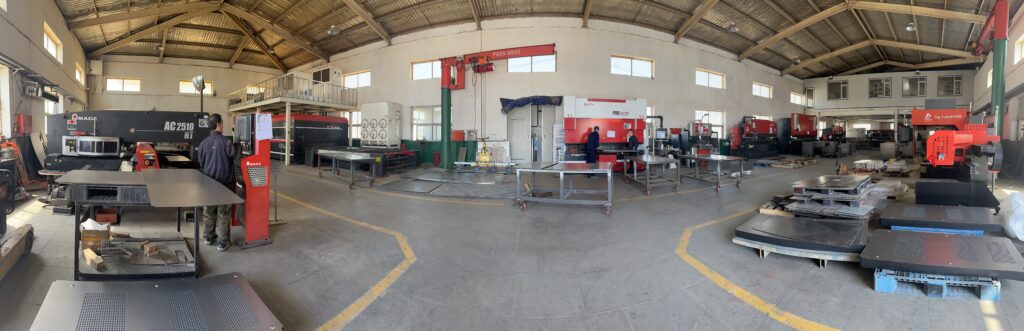
Figure No.1 Sheet Metal Fabrication Workshop
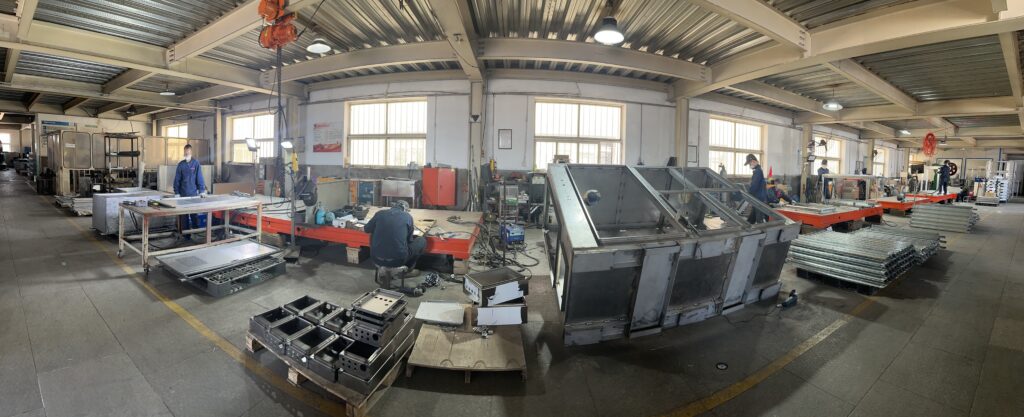
Figure No.2 Welding Workshop
Step 1: Optimize Design Solutions
Optimizing the design scheme is of vital importance in the sheet metal fabrication cost control. It can effectively reduce the labor, material and time costs during production by means of reasonably simplifying the structure, reducing the processing difficulty and material waste, etc., so as to achieve a balance between cost and quality.
The following three methods are commonly used.
Simplify the Structure
On the premise of meeting the product’s functions, try to simplify the structure of sheet metal parts and reduce unnecessary bends, holes, and complex shapes. Complex structures will not only increase the processing difficulty but also lead to an increase in processing time and costs.
Select Materials Rationally
Select appropriate materials based on the usage environment and performance requirements of sheet metal parts. The prices of different materials vary significantly. On the premise of ensuring quality, choosing materials with lower costs can effectively reduce overall expenses.
For example, for components with low strength requirements, common carbon steel materials can be selected to replace stainless steel materials.
Reduce the Processing Procedures
Reduce the processing procedures of sheet metal parts through optimized design. For example, combine multiple components into a whole to reduce the assembly procedures; or adopt the one-time forming process to decrease the subsequent processing steps.
Step 2: Sheet Metal Process Optimization Strategies
Optimizing the sheet metal processing technology is of great significance for the sheet metal fabrication cost control. It can reduce equipment wear and tear, labor and material costs by rationally selecting processing techniques, improving processing efficiency, and reducing the reject rate, etc., and enhance the comprehensive competitiveness of enterprises in terms of both cost and quality.
Laser cutting offers advantages such as high precision, fast speed, and excellent cutting quality, making it suitable for manufacturing sheet metal parts with complex shapes. Although the investment in laser cutting equipment is significant, its high efficiency can reduce unit costs during large-scale production.
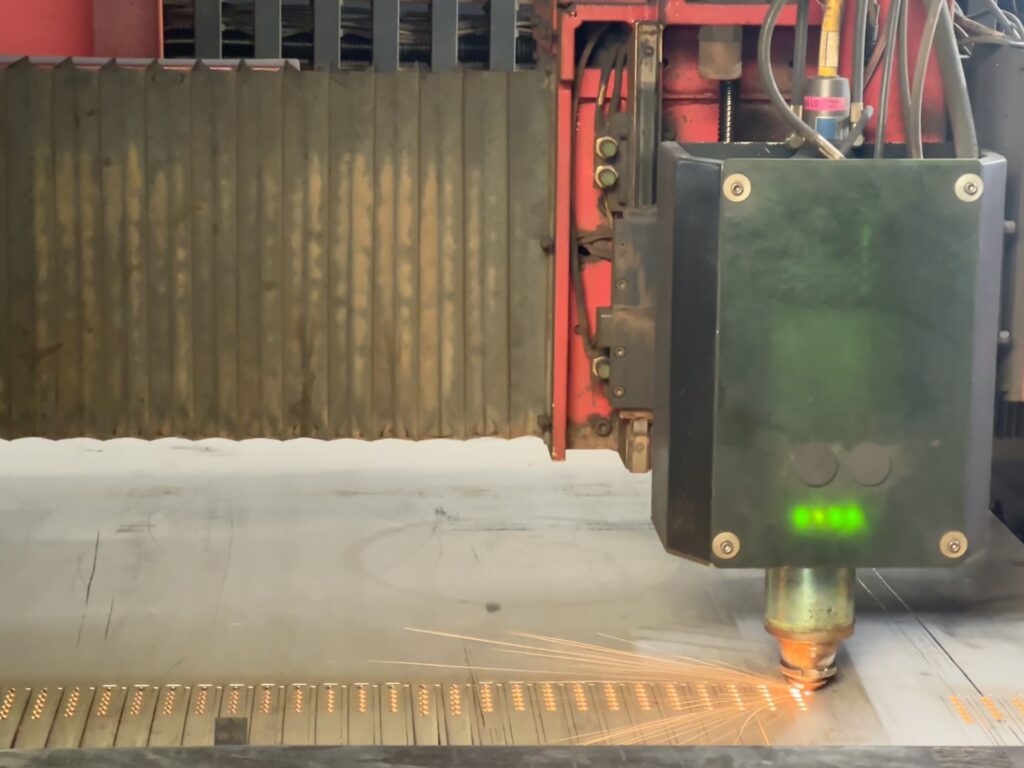
Figure No.3 AMADA LCG3015 3.5KW CO2 Laser
CNC press brakes can precisely control bending angles and dimensions, improving bending accuracy and efficiency. Implementing CNC bending technology reduces scrap rates and lowers costs.
Tips
- Sufficient bending clearance should be reserved to avoid precision problems caused by material springback.
- Avoid mutual interference of adjacent bends.
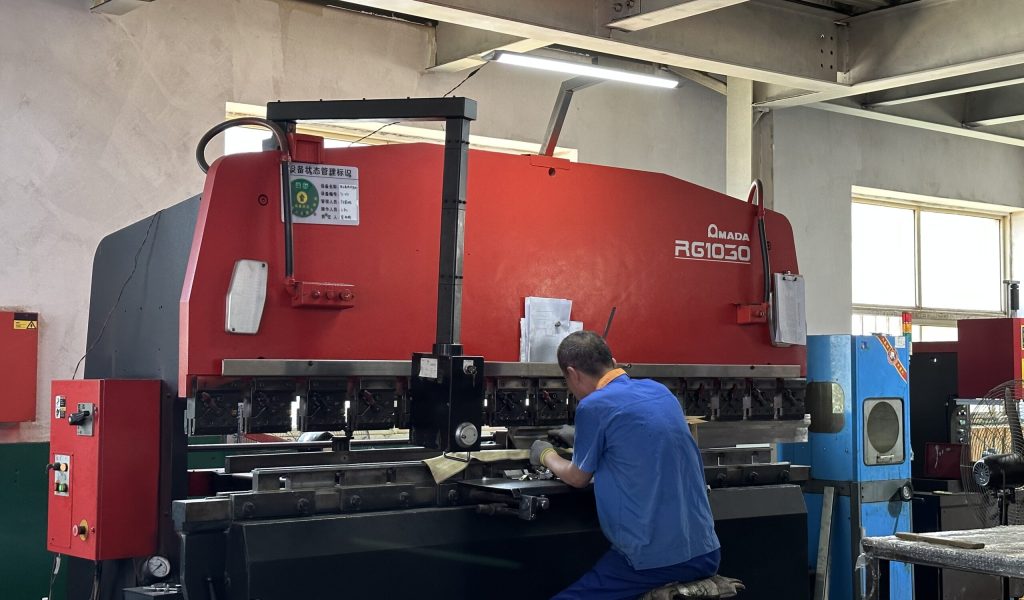
Figure No.4 AMADA RG1030 150T CNC Bender
Stamping
For mass-produced sheet metal parts, stamping provides an efficient and cost-effective manufacturing method. While stamping dies require substantial investment, the die costs can be amortized across each part during large-volume production, thereby reducing unit costs.
>>> Please Continue Reading
Step 3: Material Cost Managment
Optimize the Nesting Plan
Before sheet metal processing, use computer-aided design (CAD) software to optimize the nesting of raw materials, plan the arrangement of parts rationally, and reduce the waste of raw materials.
Recycle and Reuse Scrap Materials
Classify, recycle, and reuse the scrap materials generated during the processing.
Arrange the Production Plan Reasonably
According to the order requirements and production capacity, arrange the production plan rationally to avoid overproduction or underproduction. At the same time, optimize the production process, reduce the waiting time and waste in the production process, and improve production efficiency.
Control the Inventory Level
Control the inventory levels of raw materials and finished products reasonably to prevent inventory backlogs from tying up funds and storage space. By establishing a good cooperative relationship with suppliers, achieve the timely supply of raw materials and reduce inventory costs.
Improve the Equipment Utilization Rate
Regularly maintain and service the production equipment to ensure its normal operation and improve the equipment utilization rate. At the same time, arrange the equipment usage time reasonably to avoid equipment idleness and waste.
Step 4: Sheet Metal Supply Chain Cost Saving
Look for High-quality Suppliers
Select suppliers with good reputations, stable quality, and reasonable prices, and establish long – term and stable cooperative relationships. Through cooperation with suppliers, you can obtain better procurement prices and services, thereby reducing procurement costs.
Make Bulk Purchases
By purchasing raw materials and components in bulk, you can get more favorable prices. Negotiate with suppliers to formulate a reasonable procurement plan to ensure the stable supply of raw materials while reducing procurement costs.