Table of Contents
Design Guide for Waterproof Structure Design of Electrical Cabinets
- Betty
Introduction
As an important component of the electrical system, the waterproof performance of electrical cabinets directly affects the normal operation and service life of electrical equipment. A well-designed waterproof structure can effectively prevent water from intruding, avoiding electrical failures and equipment damage.
Design Stage
During the waterproof structure design of electrical cabinets, it is essential to determine the following design objectives. These objectives are interrelated and jointly ensure the normal operation and safety of electrical cabinets in different environments.
- What level of waterproof rating should be achieved?
- Which internal electrical components need to be protected?
- Prevent the entry of other pollutants besides water, such as dust, sediment, chemical pollutants, etc.
- What structural strength needs to be achieved?
- What ventilation and heat dissipation performance is required?
- Installation and maintenance.
- Cost
- Relevant standards and specifications.
Material Selection Stage
Cabinet materials:
It is preferable to choose metal materials such as stainless steel, cold-rolled steel, and galvanized steel, which have good corrosion resistance and waterproof performance. Engineered plastics that have undergone special treatment (such as polycarbonate PC) can also be selected, as they have advantages like light weight and good insulation performance.
Sealing materials:
Use EPDM rubber strips, which have good elasticity, aging resistance and weather resistance. For sealants, silicone sealants can be chosen, as they have excellent sealing performance and can withstand high and low temperatures.
Tips:
The sealing between the cabinet door and the cabinet body is a crucial part of the waterproof structure design of electrical cabinets.
Materials of the sealing strips:
Silicone rubber: It can withstand temperatures ranging from -60°C to 200°C.
EPDM rubber: It is resistant to ozone and ultraviolet rays and is suitable for long-term outdoor use.
Foamed silicone rubber: Its compression rate is over 40%, and it is suitable for irregular joint surfaces.
Selection of sealants:
Polyurethane sealant: It has good elasticity and is suitable for dynamic joints.
Epoxy resin adhesive: It provides rigid sealing and is suitable for permanently fixed parts.
>>> Please continue reading:
Key Points of Structural Design
Cabinet Body Structure
- To achieve waterproof design of electrical cabinets,the cabinet body should use seamless welding or full-welding processes to ensure no leakage at the joints. After welding, grind the welds and apply anti-corrosion treatment.
- Design the corners of the cabinet body as rounded or chamfered to avoid water accumulation and stress concentration.
- Give the bottom of the cabinet body a certain slope to facilitate drainage.
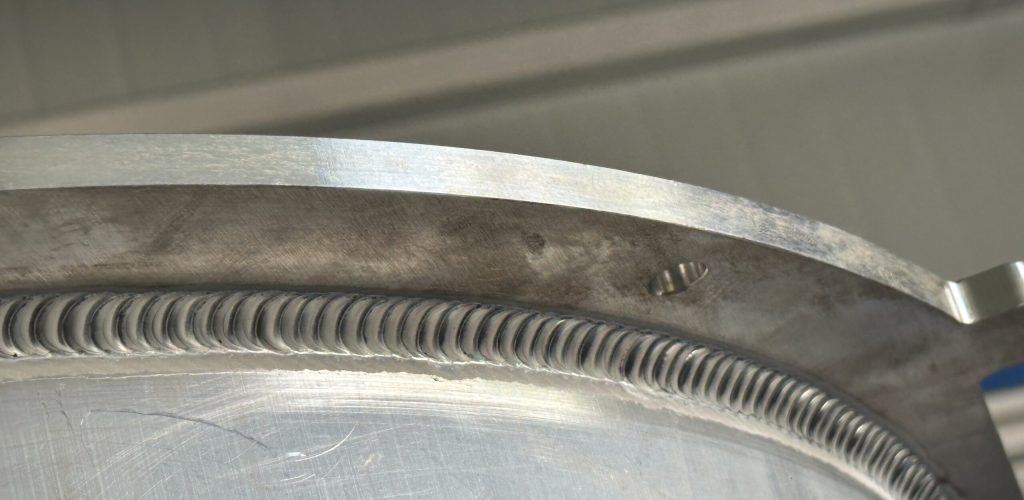
Figure No.1 Display of the Full Welding Effect
We have rich experience in the manufacturing of electrical cabinets. This article: Professional Electrical Enclosure Manufacturer
Sheet Metal Enclosure Fabrication—Complete Guide show you our entire processing flow and fabrication capabilities.
Cabinet Door
- Set a continuous sealing strip groove between the cabinet door and the cabinet body. Match the size of the strip groove with the sealing strip to ensure a tight fit after installing the strip.
- Reasonably design the closing mechanism of the cabinet door to ensure applying sufficient pressure after closing to fully compress the sealing strip and form a reliable seal. You can use multi – point locking devices or hinged pressing devices.
- Make the gap between the cabinet door and the cabinet body uniform and control it within a reasonable range (generally no more than 2mm).
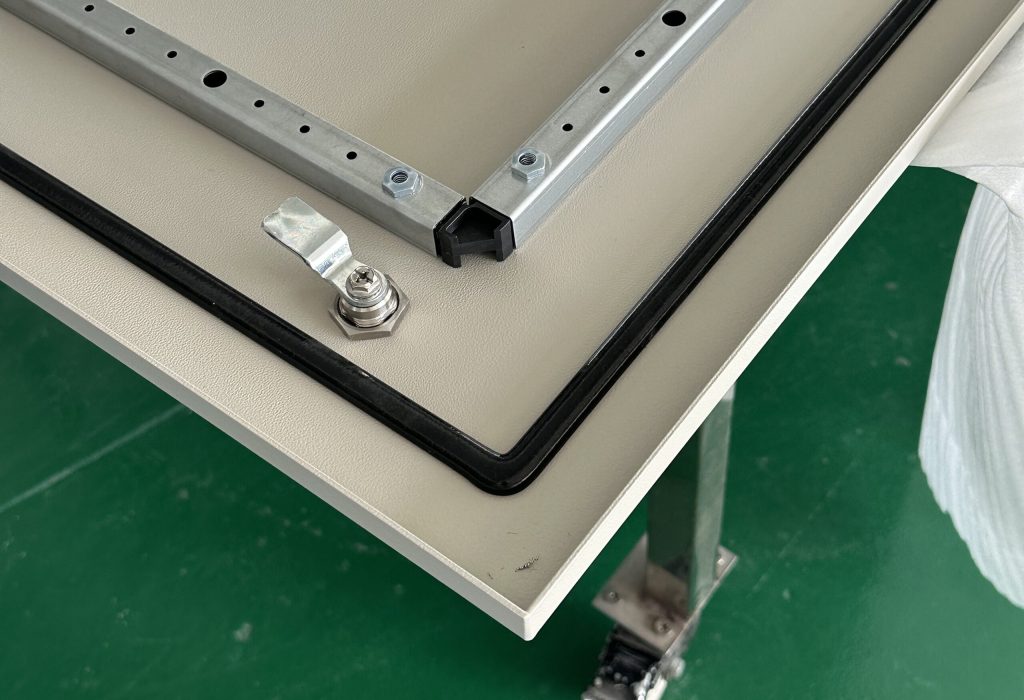
Figure No.2 Foamed Sealing Strips for Electrical Cabinet Door
The Inlet and Outlet Wire Holes
- Locate the inlet and outlet wire holes at the bottom or lower side of the cabinet body to prevent rainwater from directly pouring in.
- Install a waterproof connector (such as a gland) at each inlet and outlet wire hole to ensure a good seal between the cable and the connector.
For the centralized entry of multiple cables, use a waterproof junction box and fill the box with waterproof sealing compound. - Design the size of the inlet and outlet wire holes reasonably according to the diameter and quantity of the cables to avoid being too large or too small.
Ventilation Openings
- Install waterproof louvers at the ventilation openings. Design the angle of the louver blades reasonably to ensure that rainwater can’t enter and at the same time guarantee smooth air circulation.
- You can install an air filter inside the ventilation openings to further stop dust and sundries from getting in.
- For electrical cabinets needing forced ventilation, install waterproof devices like waterproof elbows and waterproof covers on the ventilation ducts.
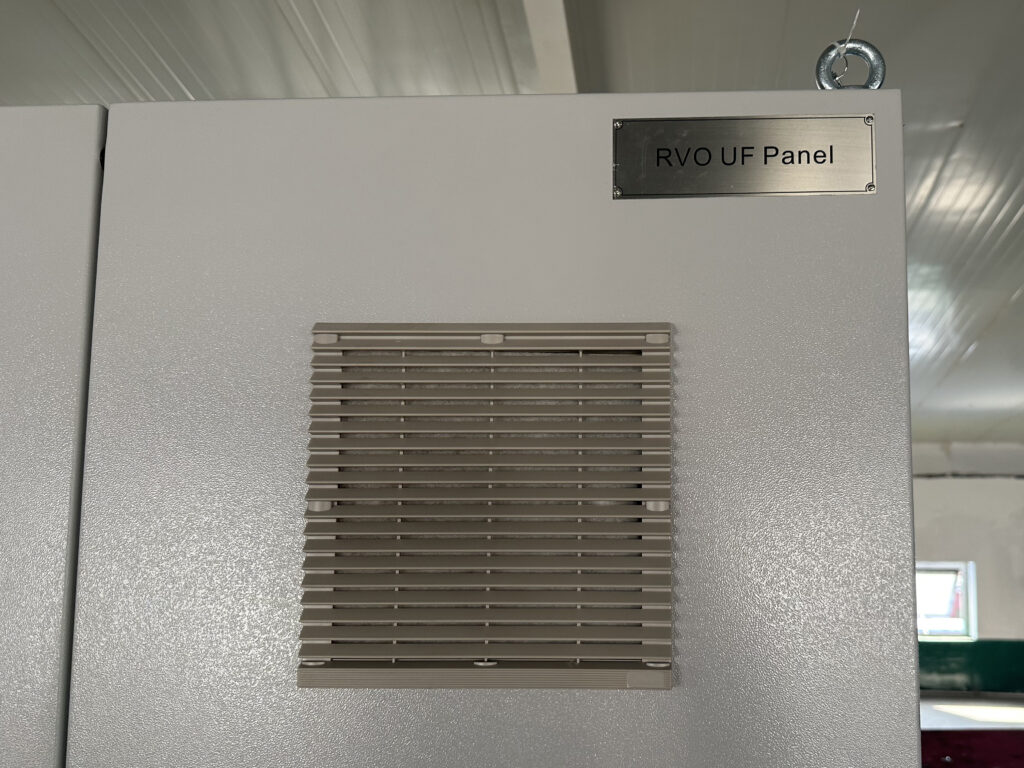
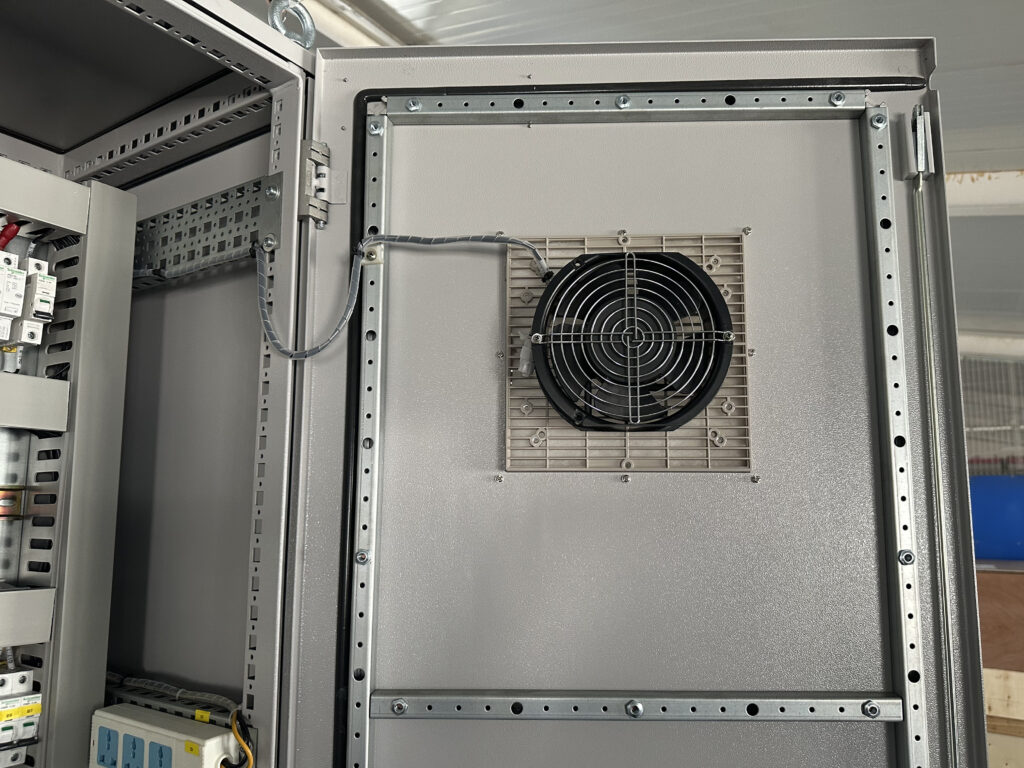
Figure No.3 Heat Dissipation Fan
Drainage design
- Set drainage holes at the bottom of the cabinet body. Reasonably design the number and size of the drainage holes according to the size of the cabinet body and the possible amount of water that may enter. Install waterproof plugs on the drainage holes to prevent dust and debris from entering.
- Set a drainage trough or drainage pipe below the drainage holes to guide the water to a suitable place for discharge. Make the drainage pipe have a certain slope to ensure smooth drainage.
Cable entry device
- Match the waterproof protection level of the cable entry device with the overall waterproof requirements of the electrical cabinet.
- Ensure that the cable entry device has good sealing performance to make sure there is no gap between the cable and the device.
- For electrical cabinets used outdoors, take additional protective measures for the cable entry device, such as installing a waterproof cover.
Observation Window
- Adopt a structure with good sealing performance for the observation window, such as double-layered glass or seal it with sealing strips.
- Connect the frame of the observation window tightly to the cabinet body to prevent water from seeping in.

Figure No.4 Observation Window
>>> Please continue reading:
Fabrication and Installation
- During the processing of the waterproof design structure of the electrical cabinet, one should strictly follow the design drawings to ensure that the dimensional accuracy and shape meet the requirements.
- The installation of the sealing rubber strips should be flat, continuous, without twisting or breaking.
- The installation of components such as waterproof connectors and ventilation openings should be firm and well – sealed.
The electrical cabinet must be installed in a dry and well-ventilated place.
Testing of Waterproof Structure Design of Electrical Cabinets
Waterproof performance testing
Before delivery, to ensure whether the waterproof structure design of electrical cabinet meets the requirements, you can use the water spray test or rain test methods to simulate the rain conditions in the actual usage environment and conduct a waterproof performance test on the electrical cabinet.
The test duration and water spray intensity should be determined according to relevant standards and the actual usage environment.
After the test, check whether there is water intrusion inside the electrical cabinet and whether there are any leakage phenomena at the sealing parts.
Maintenance of Electrical Cabinets
Regular Inspections:
Regularly inspect the sealing performance of components such as the sealing rubber strips, waterproof connectors, and ventilation openings of the electrical cabinet. If any damage or aging is found, replace them in a timely manner.
Regularly clean the drainage holes, drainage channels, and drainage pipes to ensure smooth drainage.
Surface Maintenance:
Regularly clean and apply anti-corrosion treatment to the surface of the electrical cabinet to prevent the cabinet body from rusting and corroding.
Conclusion
By following this guide for the waterproof structural design of electrical cabinets, you can effectively improve the waterproof performance of the cabinets and ensure the safe and reliable operation of electrical equipment. In the actual design and manufacturing process, you should make appropriate adjustments and optimizations to the design scheme according to the specific usage environment and requirements.
If you have any needs or questions, please feel free to contact us at any time. We will reply to you as soon as we receive your message.
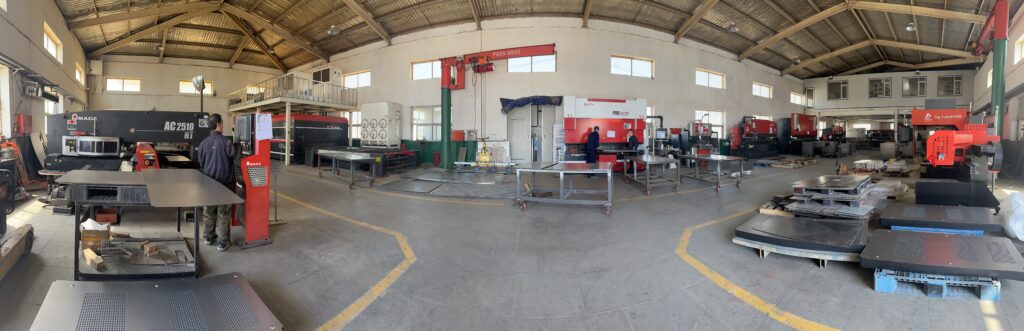
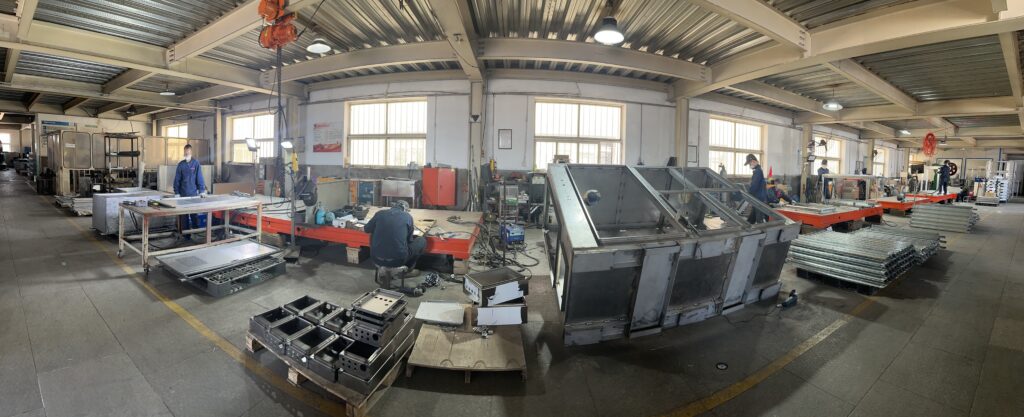
Figure No.5 Yinlu-Fabrication Workshop